ABSTRACT
It is argued that engineering and economics are not as integrated as they should be, even though the one needs the other, that the maintenance function is an outstanding example of this undesirable separation, and that engineering economics would benefit from the knowledge, practice and ideas of engineering asset management, in general, and of maintenance engineering in particular.
INTRODUCTION
Arthur Wellington is recognized as the founder of Engineering Economics (EE) on account of his seminal work, published in 1877, The Economic Theory of the Location of Railways. In it, he showed his disgust with his fellow engineers who took no account of the economic aspects of investment decisions regarding engineering assets. More than a century later, economics and engineering still live as if worlds apart. And yet, the one needs the other. This must change. One outstanding example of this long lived separation concerns the maintenance function. What happens and why?
ENGINEERING ECONOMY AND MAINTENANCE ENGINEERING
One basic concept in EE is the capacity of an asset, or group of assets, to deliver an output of goods and/or services. Consider the case of having to decide whether or not to acquire a new machine. How much is it worth? Basic economics tell us that any asset is worth the discounted value of its expected cash flow over its life cycle. However, the asset’s ability to deliver goods or services and therefore to produce a healthy cash flow depends on the physical capacity it puts at the organisation’s service. And this capacity depends on the maintenance services it gets. An obvious connection you might think? But not, it seems, to everyone.
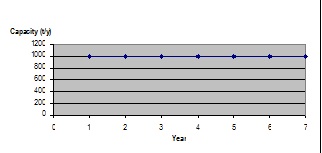
Until now, most EE textbooks implicitly assume that maintenance activities ‘just happen’ and keep capacity constant until the very last moment of an asset’s existence. Then, this capacity suffers ‘sudden death’ and thus stops creating revenue and incurring costs. This extraordinary behaviour of an asset’s capacity has been called – after the poem by Oliver Wendell Holmes – the ‘One Hoss Shay’ model of physical depreciation (see Figure 1).
This approach is an obvious simplification of a problem that is undoubtedly much more complex. EE textbooks devote many pages to describing different models, of the depreciation of fixed assets, that do not reflect physical reality. A few pioneers, a long time ago, recognized the issue and tried to include in their writings some useful information concerning real depreciation or, better still, real capacity decay. Recently, this idea has surfaced again in discussions among specialists in engineering asset management. It certainly deserves more attention and might well stimulate the joining of forces of Engineering Asset Management (EAM) – encompassing Maintenance Engineering (ME) – and EE. (As far as I can see, engineering economists are not aware of the rapid advancement of EAM. They should be) There is a lot more to say about the lack of realism in EE, a deficiency that could be cured by some injections of good engineering knowledge and practice – but for now let us see how ME interfaces with EE.
MAINTENANCE ENGINEERING NEEDS ENGINEERING ECONOMY
ME, as an engineering function, demands resources that cost money, at the same time as it promises benefits that are badly needed by any organisation. Its worth derives from a positive balance between what it produces (benefits) and what it costs (sacrifices). It must therefore be subjected to financial screening, just like any other commitment of resources. An association of ME with EE is thus of extreme importance, be it to help to choose among alternative maintenance programmes or to gain proper recognition of how much ME costs and produces. To add tasks of financial planning, evaluation and control to the maintenance function is bound to face opposition. Resistance to change is everywhere, why should it be different here? ME already has a long history of conflict with operations management, to the point of being considered a ‘necessary evil’. Although entirely disagreeing with this, I know it is a real and widely diffused prejudice. I am also convinced that every engineering function should be more involved in the financial aspects of its activities. To support this view, I will argue that –
- All those who believe that any ME is worth more than it costs must bring the evidence for this.
- It is time to improve the financial toolbox accepted and used by many authors in the ME field. It is embarrassing to admit that many tools are being imported from the textbooks on EE that lag behind the more advanced state of the art.
MAINTENANCE ENGINEERING DESERVES BETTER FINANCIAL TOOLS
ME mixes old fashioned and modern financial tools. Old stuff includes ROI (Return on Investment), a coefficient that expresses a measure of gain (return as profit or cash flow) as a percentage of sacrifice (investment). To complicate matters still further all these variables are measured in more than one way. Also, a simple payback rule that ignores the time value of money is no adequate solution. EE and Corporate Finance can offer better resources.
There are proven discounted cash flow methods – NPV (Net Present Value), IRR (Internal Rate of Return), LCC (Life Cycle Cost), B/C (Benefit /Cost Ratio) and DPB (Discounted Payback), not to mention the more refined Real Options tools. All those require two (hard to get) inputs: the investment-expected cash flow and the corresponding discount rate (adjusted by the systematic risk of the investment). This toolbox can certainly be upgraded to better satisfy the needs of any area of application. There is no reason to use old stuff.
Even if sharp tools are used, EE is not able to properly formulate the problems ME faces and to supply the required inputs. No one is more qualified to generate cash flow projections that the maintenance engineer. Acquiring skills in forecasting methods and accounting is recommended, nothing so difficult as to deter engineers from doing the job. My favourite example is cost. ME cost is traditionally gauged by how much it spends, which is just a fraction of the whole cost ‘iceberg’. There are many other costs, including hidden ones such as loss of business reputation due to the delivery of poor quality goods, the final outcome of faulty maintenance activities. It seems that current cost models ignore the costs of not doing maintenance work. A rigorous cost model is still lacking.
Discount rates come next. The use of ‘hurdle rates’ to appraise capital expenditure projects with no justification of its value is common and undesirable practice in many engineering applications. Even textbook authors in Corporate Finance and EE fail in this respect. Is that a surprise? Not so much. To adjust a discount rate to the project level of risk is no easy task. But there are means to do it, starting from the basic financial theory of asset pricing under conditions of risk. The corporate-wide cost of capital may be a good guess to begin with, because ME spending is much related to preserving the current business capacity.
ENGINEERING ECONOMICS NEEDS MAINTENANCE ENGINEERING
EE needs more engineering. Gradually, EE was pushed out of the more technical university departments, being restricted to industrial (or production) engineering departments. These may provide a better environment for engineering economists, but this certainly limits the scope and reach of their work. Take a look at the bestsellers’ textbooks: there is ever less engineering content in them – I do not want to disrespect anyone’s intellectual output, but this a sad truth. If you are sceptical, search inside any EE textbook for engineering subjects like innovation, maintenance and retrofit. You will find nothing.
From my thirty six years of experience teaching to undergraduate and graduate students of engineering at Universidade Federal do Rio de Janeiro (UFRJ) I learned that is easier to teach economics to them rather than to teach technology to students of economics or business administration. My students – they alone deserve credit for this – never offered any major resistance to becoming knowledgeable in economics. Although it was not my intention, some of them became very good economists. To my greatest satisfaction, most of them became better engineers. Where I did find some opposition was among the academic staff. To many of them, economics is not a necessary intellectual competence of the engineer. In Brazil, to the best of my knowledge, engineers tend to reach high management positions and, also, frquently become very successful entrepreneurs. At the start of their professional careers they look for opportunities, such as the MBA programmes, to strengthen their intellectual capital – a clear recognition of the missing ingredients in their undergraduate preparation.
What can ME supply that EE needs? A great deal, but I will draw attention to only two aspects.
1. First and foremost, ME is indispensable for shedding light on the matter of production capacity. Once a production plant is started up, ME enters the game to preserve its capacity. How do ME activities relate to capacity levels? I assume that maintenance engineers can answer this question in their own language. What we (engineering economists) need is to get this answer in a language that we understand. We, on both sides, must therefore strive to understand each other. The financial health of private and public organisations alike will greatly benefit from this. And, of course, we will be doing a much better job.
2. ME is a service that can be supplied in many ways. Different strategies and technologies offer a host of investment (and current spending) alternatives, with varying implications for the availability of production capacity. We must explore this territory together.
THE CAM-I CAPACITY MODEL
CAM-I is the acronym for Consortium of Advanced Manufacturing International, a not-for-profit private organisation making valuable contributions to industrial management. It has developed a capacity analysis tool, a semaphoric model that divides one facility’s capacity into three major categories: green (productive capacity, used to produce goods and to improve processes), yellow (unused capacity) and red (non productive capacity, busy with sterile activities such as waiting, reprocessing and maintenance, among others). Thus, to CAM-I maintenance is not a value adding activity. However, the same capacity model takes a 24/7 (24 hours a day, 7 days a week) schedule as a world standard. How does this capacity availability arise? What makes it possible? Maintenance, I suppose.
Is the 24/7 regime possible? What is the best ME can do to deliver maximum productive time to a particular facility? Thus, what would be, in the world as it is, the net available productive time, given the best ME solution? I would love to see these questions answered.
ENGINEERING ASSET MANAGEMENT
Economists have developed some interesting approaches to the analysis of business firms. Let me introduce two:
1. The resource view of the firm
This sees the firm as a pool of productive resources – labour, equipment, materials and so on. Resource based concepts oppose the long established view of firms as pools of products, a view which gives more importance to marketing that to technology and operations, let alone maintenance engineering. In the eighties this also represented a different stance vis à vis the Japanese lead in many manufacturing fields.
2. The process view of the firm
This approach puts a coordinate set of process and activities between resources (basic inputs) and cost objects (final outputs). Its heyday occurred in the nineties with the emergence of the radical proposals of re-engineering and activity-based costing – sometimes wrapped together under the name of activity based management.
If I had to choose, I would pick the process view of the firm. Why? Because it adds processes to resources, it asks us to look at how resources are used by the firm. Resources flow to, or are consumed by. cost objects through processes. Not every cost object is also a revenue object: some are (for instance, saleable goods), some not (such as support of community activities).
However, accountancy influence upon activity-based costing has resulted in replacing costs of resources for resources themselves. People often speak of depreciation instead of fixed assets, salaries but not labour etc. I strongly argue in favour of starting from physical resources, to only later translate their use in terms of money spent. This leaves me very comfortable with Engineering Asset Management, as regards physical assets. Not every resource is taken into account, but a very respectful share of them is.
What is good news here? Firstly, physical assets mean high cost, low decision-reversibility and technology choice. After you have decided to buy a particular equipment, a lot of money must have been spent, you will have to keep the item for many years and the choice of technology will spread its effects over other resources – labour, especially. I could have added that buying a new machine is a manly source of pleasure. EAM comes to rescue all involved in these decisions and consequences from a lack of a sound framework to analyse every business case.
Secondly, EAM invites EE to assist in every step conducive to more effective management of resources. If this invitation is not yet loud and clear, let us make it so. Economic sense has to be made of any decision that costs money, in both private and public organisations. Take the case of public infrastructure. Official reports abound giving us notice that infrastructure swallows huge budgets just to get maintenance and yet displaying a very unsatisfactory state.
Thirdly, EAM is a multi-disciplinary field, where different eyes (and minds behind them) look at the same problem: how to do the best we can with our physical assets. It is to be hoped that EAM will, in the near future, become an interdisciplinary field, where eyes will see others and minds will strive to think together. Engineers are problem solvers by nature. As problems arise and get ever more difficult to tackle, engineers must improve their preparedness. Before managing physical assets, they are challenged to manage intellectual assets. The time is now.
About the author
Dr. José Côrtes (B.Phil.,Oxford 1970; D.Sc., Production Engineering, Universidade Federal do Rio de Janeiro 1998) retired from the Universidade Federal in 2010 and is presently working as a private researcher, writer and consultant.