ABSTRACT
It is often observed an emergency unplanned plant shutdown due to failure of a machine may not only cause production loss but may also affect plant safety. A case study shows that simple on-line vibration measurement can predict the presence of a fault at early stage so that maintenance activity can be planned before failure.
INTRODUCTION
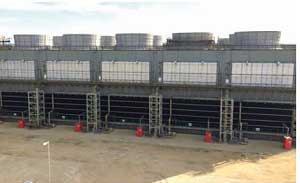
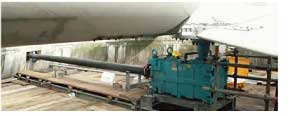

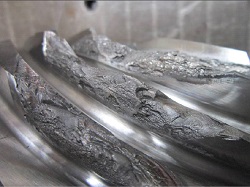
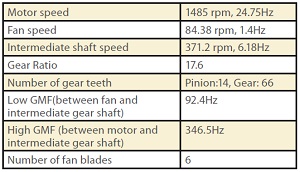
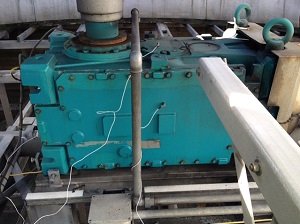
A Combined Cycle Gas Turbine (CCGT) power plant had three water-cooling towers, each of which (see Figure 1) had ten fans (five per row) for the forced cooling of the condenser water. A typical fan-gearbox unit, with schematic diagram, is shown in Figure 2; the gearbox shaft is connected to the motor.
There was no online system for monitoring the health of each fan-gearbox-motor (FGM) unit during plant operation. However, it has been observed that a few fans stopping working simultaneously had often been the cause of an unplanned plant shutdown. Physical inspection after such failure always confirmed that it had been due to damage to the intermediate shaft bevel gear teeth. A typical damaged gear box is shown in Figure 3.
VIBRATION MEASUREMENT AND ANALYSIS
The running speeds of the gearbox, fan and motor and their related frequencies together with the gear mesh frequencies (GMFs) are listed in Table 1. Vibration measurements were carried out on the gear box of an FGM unit during its normal operation. The mounting locations of the accelerometers are shown in Figure 4 and the measured acceleration spectrum in Figure 5.
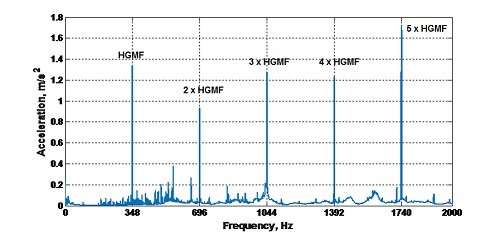
The spectrum shows the presence of the high gear mesh frequency (HGMF) at around 348Hz, and its higher harmonics, which indicates wear in the teeth related to the motor and intermediate shaft’s gear mesh. However, a closer look around the high GMF at 348Hz (see Figure 6) shows the presence of side bands of the cluster of frequency peaks at equal intervals of 6.2Hz. These side bands indicate the presence or initiation of faults in both the motor and intermediate shaft’s gear teeth. This is because the intermediate shaft speed is 317.2 rpm (6.18Hz) and the motor speed is 1485 rpm (24.75Hz = 4 × 6.18Hz). Note that the increase in the amplitude of side band frequency peaks with machine operating time generally indicates the fault propagation with time.
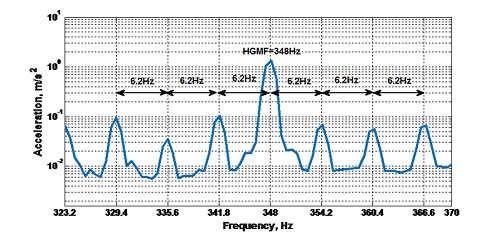
CONCLUDING REMARKS
This case study confirms that a simple on-line vibration measurement and spectrum analysis, at the gear box only, can provide knowledge of the health of both the gear box and the fan that can be used to forestall unplanned shutdown of the unit and hence production loss. It is important to note that such measurements and analysis may not involve high skill and instrumentation cost.
ACKNOWLEDGEMENT
The authors wish to acknowledge the support of Innovate KTP Project no 9227 (TSB Project No. 508926).
ABOUT THE AUTHORS
Erfan Asnaashari is Research Associate, School of MACE, The University of Manchester, currently based in EDF’s West Burton Power Station, Retford and working on wind turbines.
Keri Elbhbah is Knowledge Transfer Partnership (KTP) Associate, School of MACE, The University of Manchester, also currently based in EDF’s West Burton Power Station, Retford and working on the vibration-based monitoring of the condition of steam turbine blades.
Wolfgang Hahn is Head of Engineering, Coal, Gas and Renewables, EDF Energy UK and is visiting academic at The University of Manchester. He has extensive experience, over more than 25 years, in reliability, maintenance and design improvement in the manufacturing and power industries.
Jyoti K. Sinha is Director, Reliability Engineering and Asset Management programme and Head, Dynamics Laboratory, School of MACE, The University of Manchester. Has recently authored the book Vibration Analysis, Instruments and Signal Processing (CRC Press, 2014).