ABSTRACT
In addition to the well-known application, in various industries, of power consumption monitoring for the detection of faults associated with electric drives, experimental observations have indicated that it is also possible to detect and classify rotor-related faults by examining the energy patterns, under different operating conditions, of the studied rotating machine
INTRODUCTION
Rotating machines have proven to be vital elements of most industrial processes. In some instances they inevitably fail at certain stages of their operational cycles due to the extreme and constantly changing conditions under which they function. A typical rotating machine principally consists of the rotor, support structure, bearings and the source of rotational motion, usually an electric motor. In most industries the detection and diagnosis of common rotor-related faults (such as mis-alignment, unbalance, rubbing, looseness, cracking, etc.) have been dominated by well-established condition monitoring (CM) techniques, especially vibration analysis – although fault detection in rotating machines via the monitoring of power consumption is quite popular, particularly due to the enactment, in various countries, of strict industrial regulations that promote reduced carbon emissions and energy utilization efficiency. While it is impossible to ignore the fact that popular CM techniques such as vibration, temperature and lube/wear debris analyses have immensely contributed towards ensuring the availability of rotating machines, their applicability to some emerging and critical industrial rotating machines could still be limited. In the case of wind turbines (WTs), for example, this could be due to [1] –
- Lack of matured field experience with CM,
- Lack of an existing universal CM approach that satisfies the need of all WT types
- The fact that the development of an entirely novel and robust CM technique for WTs would usually entail the detailed analysis of the design parameters and ‘real-life’ operational performance, which often involves a complex and rigorous collaboration between designers and operators.
On the other hand, detailed exploration of the possibilities for developing power analysis for such crucial machines has suggested that there might be several advantages, including [1];
- The sensors needed for power monitoring are cheaper than those required for vibration and lube/wear debris analysis.
- Current signals used for controlling industrial rotating machines such as WTs, and power signals from the generator terminal voltage are already available.
- Power monitoring offers detectability of both electrical as well as mechanical faults since both affect power output.
Research studies of the relationship between power characteristics of industrial rotating machines and their states of health have gained popularity among the condition monitoring community. For instance, Pillutla et al [2] and Wamkeue et al [3] showed the link between rotating machine health parameters and stator currents by respectively applying neural network and least square methods, studies which have since led to the emergence of alternative means of fault diagnosis. A similar experimental study conducted by Cardoso [4] indicated that a rotating machine can be classified as healthy or faulty on the basis of the pattern of the calculated stator current Park’s vector. In this work it was reported that the circular locus patterns displayed by healthy machines, on the one hand, and faulty machines, on the other, were significantly different, especially when the fault considered related to inter-turn stator windings, voltage imbalance and single phasing in three-phase induction motors [5]. Other studies have included studying surge comparisons for detecting motor insulation defects, air-gap harmonic analysis for detecting stator winding defects, rotor bar faults, dynamic eccentricity and motor bearing faults [6-10].
Based on the literature currently available, the application of measurement of power consumption and energy characteristics of rotating machines as a CM technique has been significantly skewed towards the detection of faults associated with the electric drive component of the rotating machine system. It is a well-known fact that the reliability of electrical machines, such as induction motors, as well as of their associated components (e.g. rotor, stator, windings, insulators, bearings, etc.) is very crucial to most plant operations. However, since other machine faults, especially rotor-related faults (e.g. misalignment, shaft rub, shaft crack, looseness, etc.) also contribute immensely to reduction in plant reliability, efficiency, uptime and safety, it would be very useful to experimentally observe how common rotor-related faults impact on the power consumption of typical industrial rotating machines.
EXPERIMENTS
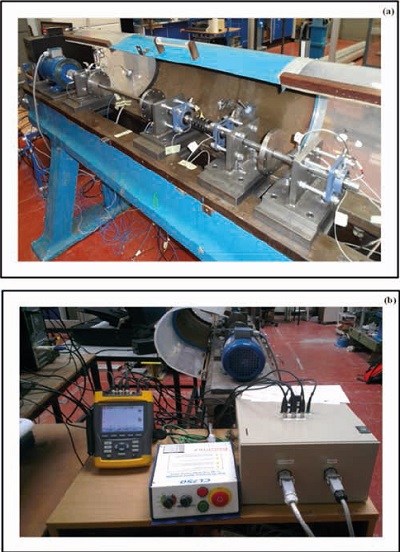
The power consumed by a laboratory based experimental rig designed and constructed at the University of Manchester Dynamics Laboratory was examined under different machine conditions (i.e. unbalance, shaft misalignment, bearing pedestal looseness and shaft rub) at 2400 rev/min machine speed.
The studied experimental rig consisted of a variable speed 0.75 kW induction motor flexibly coupled to a 1.5 m long shaft. Three similarly dimensioned balanced discs were respectively mounted along the length of the shaft, the entire assembly being supported by four flanged-mounted anti-friction ball bearings, as shown in Figure 1(a). On this rig, the four distinct rotating machine conditions investigated were
(a) 0.0004 m magnitude shaft misalignment initiated at Bearing 1 pedestal;
(b) unbalance;
(c) bearing pedestal looseness;
(d) the creation of shaft rub action near Bearing 2 by using a 0.021 m diameter brass sleeve.
The power consumed by the experimental rig under the different experimentally simulated machine conditions for several data sets was then measured using the energy meter shown in Figure 1(b).
OBSERVATIONS
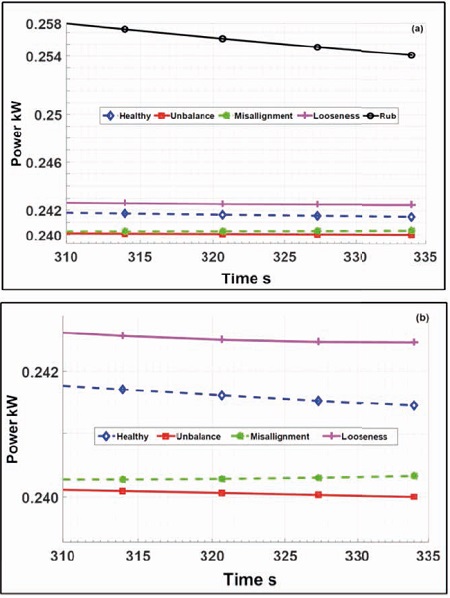
The aim of the study was to investigate the extent to which measurement of power consumption could be used to distinguish various types of rotor-related faults. Figure 2 (a) shows a plot of observed Power (kW) against Time (s) for all five experimentally simulated conditions (i.e. relatively healthy, unbalance, shaft misalignment, bearing looseness and shaft rub). A measurement duration of 0-332 seconds was used for each machine condition during the experiments. However, only 310-335 seconds of the measured data segment is displayed in Figure 2 due to the high power consumption associated with electric drives during start-up, which may not necessarily be an indication of the presence of a fault.
Figure 2 (a) shows that the shaft rub condition exhibited a distinctly high power magnitude due to its known characteristic chaotic nature while the other four experimentally simulated machine conditions had far lower magnitudes. Figure 2 (b) is a ‘zoomed’ view of Figure 2 (a), i.e. with the power axis expanded and the shaft rub condition deliberately excluded so as to clearly show the difference in power consumption of the other four machine conditions. It should also be noted that the reason for the higher amplitude of the relatively healthy condition (compared with that of some of the faulty conditions, such as shaft misalignment and unbalance) is due to the fact that the relatively healthy condition observed during these experiments is also associated with some amount of misalignment and unbalance. Also, the experimental rig had to be stripped and re-assembled prior to the simulation of individual conditions, which could have significantly skewed the machine away from healthy and towards faulty condition. However, despite these limitations of the experimental simulations, the power consumption measurements indicate that the different rotor-related machine conditions considered exhibited different energy levels, showing the possibility of using such measurement as a simplified condition monitoring technique for diagnosing rotor-related machine conditions. In addition to the non-intrusive and non-destructive nature of this approach, the cost of its implementation is also minimal since the acquisition of power data for most electric drives is an integral part of most industrial operations.
ACKNOWLEDGEMENT
The presented work is an extract from a Reliability Engineering and Asset Management (REAM) MSc dissertation from the University of Manchester.
REFERENCES
[1] Yang W, Tavner P J, Crabtree C J, Wilkinson M, Cost-effective condition monitoring for wind turbines. IEEE Transactions on Industrial Electronics, 2010; 57(1):263-271.
[2] Pillutla S, Keyhani A, Kamwa I, Neural network observers for on-line tracking of synchronous generator parameters. IEEE Transactions on Energy Conversion, 1999; 14(1):23-30.
[3] Wamkeue R, Kamwa I, Dai-Do X, Keyhani A, Iteratively re-weighted least squares for maximum likelihood identification of synchronous machine parameters from on-line tests. IEEE Transactions on Energy Conversion, 1999; 14(2):159-166.
[4] Cardoso A J M, Cruz S M A, Fonseca D S B, Inter-turn stator winding fault diagnosis in three-phase induction motors by Park’s vector approach, IEEE Transactions on Energy Conversion, 1999, 14(3):595-598.
[5] Nejjari A, Benbouzid M, Ei H, Monitoring and diagnosis of induction motors electrical faults using a current Park’s vector pattern learning approach. IEEE Transactions on Industrial Electronics, 2000; 36(3):730-735.
[6] Kliman G B, Stein J,. Methods of motor current signature analysis, Electrical Machines and Power Systems, 1992; 20(5): 463-474.
[7] Schoen R R, Habetler T G, A new method of current-based condition monitoring in induction machines operating under arbitrary load conditions. Electric Machines and Power Systems, 1997; 25(2): 141-152.
[8] Riley C M, Lin B K, Habetler T G, Kilman G B, Stator current harmonics and their causal vibrations: a preliminary investigation of sensorless vibration monitoring applications. IEEE Transactions on Industry Applications, 1999; 35(1): 94-99.
[9] Riley C M, Lin B K, Habetler T G, Schoen R R, A method for sensor-less on-line vibration monitoring of induction machines, IEEE Transactions on Industry Applications,1998; 34(6): 1240-1245.
[10] Watson F J, Dorrell G D, The use of finite element methods of improve techniques for the early detection of faults in three-phase induction motors, IEEE Transactions on Energy Conversion, 1999; 14(3): 655-660.
Authors’ contact addresses
simon.boniz@gmail.com
akilu.kaltungo@manchester.ac.uk
jyoti.sinha@manchester.ac.uk