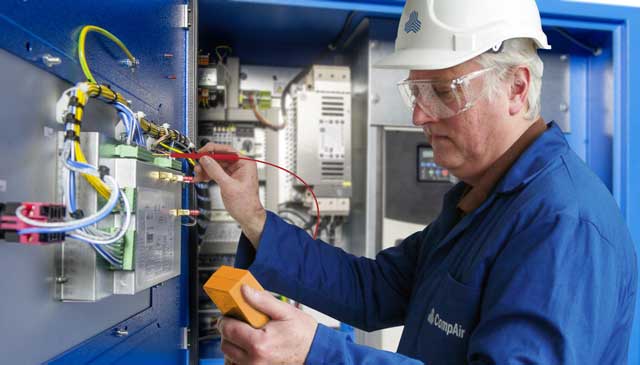
Annually, UK industry uses over 20TWh of electricity to compress air, equivalent to the output of four power stations and over 8.1 million tonnes of CO2 emissions. As a result, high-quality energy performance at a cost-effective price continues to be a key consideration for businesses. Keith Findlay, compressed air audit manager at Gardner Denver, outlines the benefits of energy audits, and the improved efficiencies they can help realise.
Total cost of ownership
A key driver for innovation and technological advancement is total cost of ownership. Businesses of all sizes have become increasingly wary of buying a compressed air system for a low upfront cost, only for issues to arise later that mean any savings originally realised are lost in service and maintenance costs.
Organisations are moving away from considering the initial purchase price for a piece of equipment alone, and starting to focus on the whole-life costs. Servicing and maintenance costs are no longer seen as separate entities, but as parts of a whole.
The British Compressed Air Society recently introduced BS ISO 11011, which has now been adopted as IS ISO 11011, on assessing the energy efficiency of a compressed air system. Regardless of the size or scale of operations in question, businesses could potentially save a significant sum of money on their bottom line.
As a result, compressed air systems are being more closely scrutinised than ever before. Undertaking a thorough and detailed energy audit can reduce total cost of ownership at the same time as improving efficiency.
Air demands
Generating compressed air accounts for 10% of total energy costs in industry, so keeping waste to an absolute minimum should be a key concern for all operators. With energy accounting on average for more than 80% of the total cost of ownership of a compressor, datalogging equipment is increasingly being used, helping companies identify inefficiencies and assisting with performance optimisation, leak reduction and practical air management processes.
The consequences of not dealing with these issues can be problematic, both with regard to equipment performance and the financial implications.
Leaking profit
There are many reasons for leaks in a compressed air system. Regular culprits include manual condensate drain valves being left open, shut-off valves being left open, and leaking hoses, couplings, pipes, flanges and pipe joints.
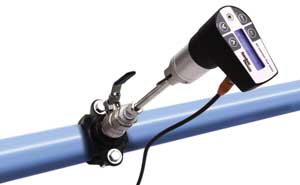
Leaks in pipework can account for up to 35% of total air consumption, and the Carbon Trust reports that a leak as small as 3mm could cost more than £700 annually in wasted energy. The latest flow meters offer a reliable means of evaluating compressed air generation and the associated costs from any downstream inefficiency. Finding and repairing one 3mm leak could save enough money to cover the cost of the meter.
Minimising system leakage is not a one-off activity, because leaks will recur in different locations. Energy audits can help identify leaks and make sure they are managed effectively.
Energy recovery
Recovering heat generated by a compressor is gaining popularity, and is a good example of how an energy audit can illustrate how a business might improve operational efficiency.
Evidence shows that 94% of the heat generated by a compressor can be recovered. This can be achieved through a number of processes, such as recirculating warm air from the compressor to a local area as space heating, or by installing an energy recovery unit.
Energy recovery units transfer heat from the compressor oil circulation system to an incoming water supply, which can be used for hot water washing, central heating, steam systems and in other manufacturing processes where heated water is required.
An energy audit can help determine the heat recovery potential from a compressed air system.
Next steps
Before undertaking an energy audit with a business, a reputable supplier should first carry out a pre-assessment survey, looking at a range of variables that will have an affect on compressed air use. These include: compressor kW ratings; the flow, dew point, pressure and temperature required; the time required to perform a leak survey; shift patterns; cost of electricity on site; and any obvious signs of leaks.
From here, the company will be able to advise whether the business will benefit from an energy audit. A typical audit report from Gardner Denver, for example, will then include the following: an overview of the compressed air system, a power and flow report, temperature data, an air leakage survey, a report on any pipework issues, potential energy-saving opportunities and then a proposal of how to implement these suggestions.
Eminent mathematical physicist and engineer Lord Kelvin once said: “To measure is to know. If you cannot measure it, you cannot improve it.” This demonstrates exactly why an energy audit can be highly valuable, helping to make vital cost savings and improve operational efficiency.