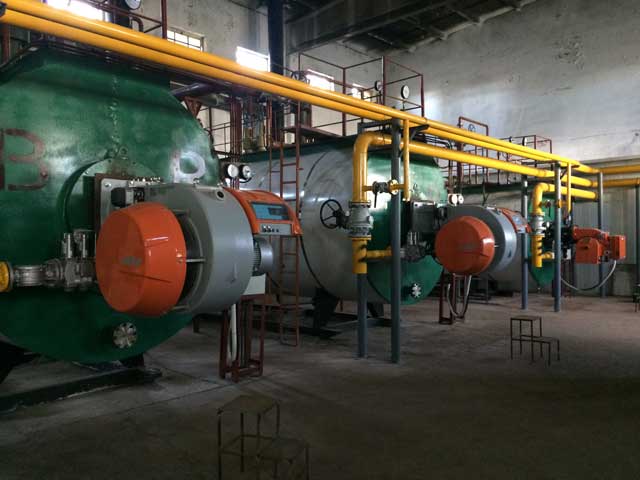
Of the two main types of boiler for industrial applications, the fire-tube type is more common in the UK. Phil Pett, commercial sales manager at burner manufacturer and distributor EOGB Energy Products, explains why water tube boilers should not be overlooked.
In the UK there are two primary types of boiler which are used for steam generation in industrial installations – water tube and fire tube.
It is difficult to argue that one of these types is superior to the other: both have distinct advantages and disadvantages. However, the fire tube boiler (also known as a shell boiler) is much more commonly used in the UK: this is thought to be for historic reasons (the design of the fire tube boiler dates to the eighteenth century, when it was used for steam locomotives).
Fire tube boilers
In a fire tube or shell boiler, the hot combustion gases produced by the burner are passed through small tubes arranged in a pressurised cylindrical drum and surrounded by water. Heat energy is transferred to the water which is heated up until it becomes steam.
Fire tube boilers are a lower cost alternative to water tube boilers and are often used for smaller industrial facilities with lower operating pressures. The main advantages of a fire tube boiler are its simple construction, compact size and the ability to easily meet rapid fluctuations in steam demand.
Disadvantages are the excessive time it takes to raise steam pressure because of the relatively large volume of water, the lower efficiency of heat transfer (because the heat exchanger uses less thermal radiation) and the inability to respond quickly to sustained large load changes (which is also a result of the large volume of water).
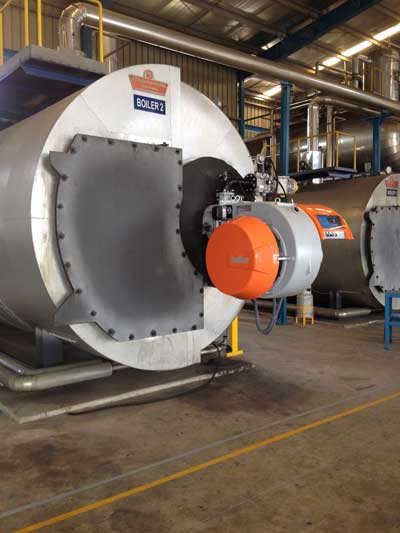
Water tube boilers
Industrial water-tube boilers work in the opposite way: water is circulated inside the boiler tubes and the tubes are surrounded by hot gases. This type is relatively rare in the UK, but much more common in other parts of the world.
Due to the small tube diameter, a water tube boiler can operate at much higher pressures than a fire tube boiler, so they are often used in power station applications that require a high steam output, high pressure steam or superheated steam.
Advantages
Such boilers are often powered by more than one burner, and these can be used individually or in parallel on a single furnace, which provides the opportunity for individual controlled shutdowns for maintenance without having to turn the boiler off entirely. The burners can operate at different loads over the furnace to take into account fluctuations in demand, resulting in reduced emissions.
Water tube boilers are supplied with a custom programmable logic controller (PLC) for boiler management and modulation of the burner (or burners), which can control the superheater, level control and feedwater systems.
As there is a smaller volume of water in the tubes in a water tube boiler than a fire tube type, they produce steam much faster and are exceptionally responsive. They are also extremely efficient, operating at higher pressure, and can produce saturated or superheated steam depending on the design and application they are required for.
The water tube boiler can be designed to work with high-ash fuels in conjunction with soot blowers and the appropriate ash handing and flue gas clean-up equipment to meet environmental regulations. This means the design lends itself to biomass applications and waste-to-energy plants.
Disadvantages
The disadvantage of a water tube boiler is that the capital cost is normally higher than the equivalent fire tube boiler and, depending on the size, it often has to be constructed on site, which can add to the costs and timescale. Special designs can take into account site space limitations but this can also add to the project budget.
The complexity of the control systems can be overcome through bespoke training and appropriate levels of automation, but there is additional cost associated with this.
However, automation can improve reliability and offer solutions for remote monitoring and troubleshooting that can mitigate the capital investment, offering operational savings and improvements in predictive maintenance.
Summary
Both fire tube and water tube boilers have advantages and disadvantages in different industrial applications. The reason that water tube boilers are very rarely used in the UK is unclear, but can be attributed to historical reasons and the fact that the fire tube method is seen as the “traditional” technique to produce steam.
In the light of new efficiency regulations such as the European Energy-related Products directive, many companies are choosing to replace traditional boilers. Choosing the right boiler for an industrial application is not an easy task and it is important to make a decision based on a number of factors such as steam production needs, reliability, efficiency, operating costs and ease of maintenance.