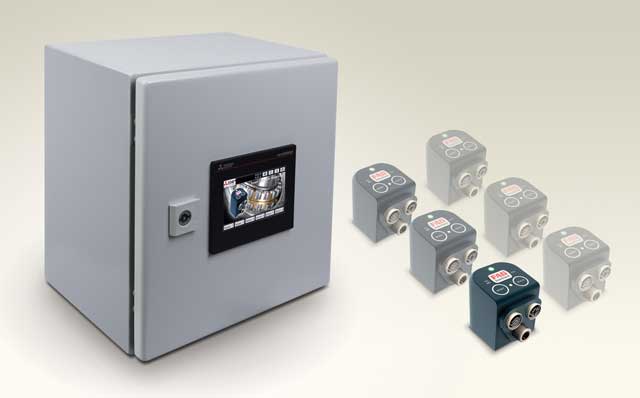
Predictive maintenance is helping food and beverage companies to reduce downtime and improve profitability, says Jeremy Shinton, solutions manager in the marketing and operations group of Mitsubishi Electric’s automation systems division.
With margins continually driven down by retailers, and an increasingly fickle public driving new product requirements, food and beverage businesses rely on efficient flexible operations for their profitability and competitive differentiation. Meeting the challenges of the food processing sector means increasing machine availability and reducing unscheduled downtime. That requires techniques that will help to manage maintenance and maximise reliable production.
Reactive maintenance – fixing problems after they have caused unscheduled downtime – is the worst possible approach. Preventive maintenance is an improvement, in that impending problems can be tackled during scheduled downtime. But all too often products are replaced on the basis of statistical lifecycle data. So you could be replacing components that might still have years of useful life left in them, while on the other hand unexpected failures could still catch you by surprise.
Predictive approach
Condition monitoring, in contrast, offers a predictive approach to plant maintenance based on a continual live status, optimising asset performance while keeping downtime to a minimum. Predictive maintenance is built on real-time monitoring of actual machine parameters to help eliminate downtime and is an important step in maximising productivity.
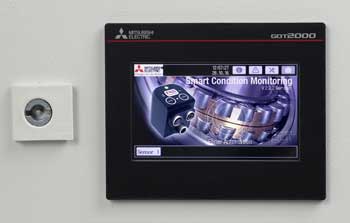
Condition monitoring technologies continue to evolve. An example is the Smart Condition Monitoring solution from Mitsubishi Electric, which combines FAG SmartCheck sensors from Schaeffler with Mitsubishi Electric control technologies. In addition to systems built around physical Mitsubishi Electric programmable logic controllers, uniquely an SCM solution can be embedded within a Mitsubishi Electric inverter drive, using the inbuilt PLC feature to provide dedicated local monitoring systems without the need for additional control hardware.
In its broadest implementation, the SCM solution provides an integrated approach to monitoring the health of individual assets and enables a holistic approach to be taken to monitoring the health of the whole plant. Individual sensors retain a traffic light system for local status indication at the machine. At the same time information from multiple sensors is transferred over Ethernet to the intelligent sensor control system for in-depth monitoring and more detailed analysis.
Linking the sensors to the control system enables the controller to analyse patterns of operation that are outside the norm, with a series of alarm conditions that can provide alerts when attention is needed. The SCM analysis provides detailed diagnostics, and provides maintenance staff with more precise error identification. It even provides recommendations on what remedial actions should be taken, via clear text messages.
For example, detecting an increase in vibration on a pump motor, the status indicator on the individual SmartCheck sensor would switch from green to amber, while the display would show a text message such as: “The measurement system has reported a pre-alarm for vibration. Possible fault sources for this anomaly can include: bearing damage, gearing damage or loose components. We recommend taking further diagnostic steps.”
This information can be networked to higher-level systems for trend analysis over all the assets around the plant.
Continuous monitoring
Once set up, the SCM provides continuous monitoring of each asset, with functions including bearing defect detection, imbalance detection, misalignment detection, lack of lubricant, temperature measurement, cavitation detection, phase failure recognition and resonance frequency detection. User interfaces can range from displays on the plant floor, to management PCs or mobile devices working over a secure network, providing convenience and efficiency for both operators and managers.
In a number of installations SCM technology is already reducing downtime and saving money. In one sugar processing application, for example, a one-hour stoppage represented a cost of €60,000 (£53,000), so plant managers were keen to gain greater insight into key assets. Four gearboxes were fitted with SmartCheck sensors and integrated into an SCM system, with data displayed locally as well as being made available at enterprise level via an Ethernet network, enabling preventive maintenance to be performed and eliminating costly unscheduled downtime.
The solution is a practical example of how a smart factory should work, with predictive maintenance information being made readily available either locally, or being pushed into the enterprise level for analysis in the total productive maintenance system. The result is the elimination of unplanned downtime, along with increased asset availability.