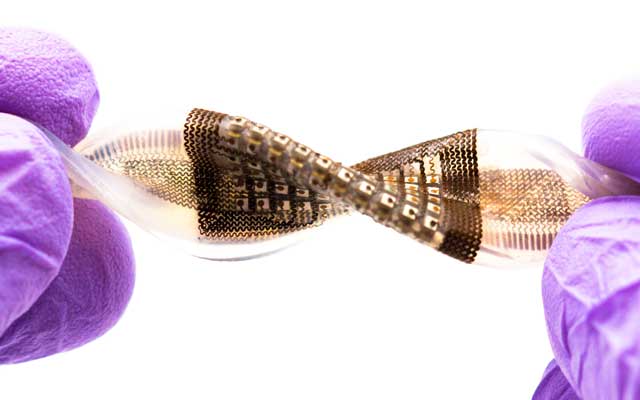
Researchers have developed a stretchable, flexible patch that could make it easier to perform ultrasound imaging on irregularly-shaped structures, such as turbines, engine parts, and reactor pipe elbows, which are difficult to examine using conventional ultrasound equipment.
The ultrasound patch promises to be a versatile and more convenient tool to inspect parts for defects and damage below the surface.
A team of researchers led by engineers at the University of California San Diego published the study in Science Advances.
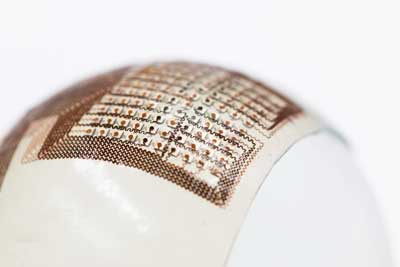
Conventional ultrasound devices are difficult to use on objects that don’t have perfectly flat surfaces. Their probes have flat and rigid bases, which can’t maintain good contact with curved, angled and other irregular surfaces.
Gel, oil or water is typically used to create better contact between the probe and the surface of the object, but too much can filter out some of the signals. Conventional ultrasound probes are also bulky, making them impractical for inspecting hard-to-access parts.
Sheng Xu, a professor of nanoengineering at the UC San Diego Jacobs School of Engineering, said: “If a car engine has a crack in a hard-to-reach location, an inspector will need to take apart the entire engine and immerse the parts in water to get a full 3D image.”
The flexible probe is a thin patch of silicone elastomer patterned with an “island-bridge” structure. This is an array of small electronic parts (islands) that are each connected by spring-like structures (bridges). The islands contain electrodes and piezoelectric transducers, which produce ultrasound waves. The bridges are spring-shaped copper wires that can stretch and bend, allowing the patch to conform to non-planar surfaces.
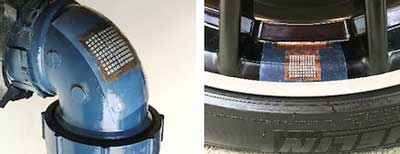
The device was tested on an aluminum block with an irregular surface. The block contained defects 2-6cm beneath the surface. Researchers placed the probe at various points on the surface, collected data and then reconstructed the images using a data processing algorithm. The probe was able to create images of the 2mm wide holes and cracks inside the block.
The team envisages the probe being attached to an aircraft wing or other structure and used to continuously monitor it for cracks.
The device is still at the proof of concept stage. It does not yet provide real-time imaging. It needs to be connected to a power source and a computer to process data. “In the future, we hope to integrate both power and a data processing function into the probe to allow wireless, real-time imaging and videoing,” Xu said.