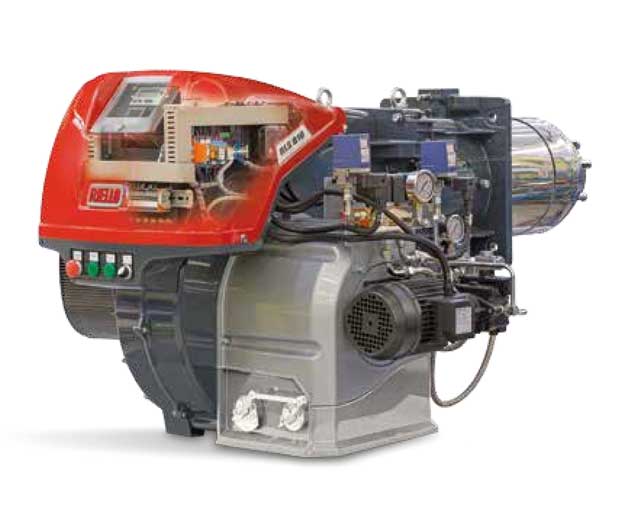
Emissions of nitrogen oxides from combustion equipment are becoming an increasingly important consideration from both an environmental and regulatory point of view. Riello technical director Bernard Dawson explains how NOx levels from burners can be reduced.
As regulations governing emissions of nitrogen oxides continue to be tightened it becomes increasingly important for engineers and building operators to make use of the latest burner technologies to reduce emissions. To achieve low NOx levels, there are two key technologies to understand – flue gas recirculation and premix.
Flue gas recirculation
Flue gas recirculation (FGR) is a proven method for reducing NOx levels in pressure jet burners, but historically has not been widely used in the UK because it requires additional controls. However, as NOx regulations tighten, it is a very effective way to meet these stricter requirements.
Air contains around 79% nitrogen, so a considerable amount of nitrogen is introduced into the combustion chamber of boilers and other combustion equipment, potentially leading to formation of NOx. NOx formation is exacerbated by high flame temperatures.
The principle of FGR is that a percentage of flue gases – which are relatively cool and inert – are piped back into the burner air supply system to reduce the flame temperature. Further cooling is achieved by the inhibiting presence of carbon dioxide in the flue gas.
FGR burners are available with outputs from 500kW to 32MW, to provide NOx emissions of 40mg/kWh or below. To put this figure into context, EN 676, the standard for automatic forced draught burners for gaseous fuels, classifies burners achieving 80mg/kWh or less as “low NOx”.
Premix
There are occasions where premix burner technology is an appropriate alternative to FGR. The main differences between traditional pressure jet burners and premix burners are in the way in which the air and gas is mixed and in the technology of the combustion head.
In traditional pressure jet burners, the gas and the combustion air are mixed at the point of ignition, at the end of the combustion head. In premix burners the air-fuel mixture is created upstream of the combustion head – which comprises a metallic cylinder that has multiple gas ports on its surface and is covered with a woven wire gauze (known as a “sock”). The air-fuel mixture flows inside the combustion head, through the precision-located ports and the sock to the external side of the combustion head, where ignition occurs.
This means that the flame develops only on the external surface of the combustion head, with combustion taking place very close to the metallic fibre of the blast tube. This results in an extremely compact flame, with lower peak temperatures, reducing the potential for NOx formation.
Even on large burners up to 3MW, we have seen NOx emissions of lower than 30mg/kWh and, on some independently witnessed site tests, even down to less than 20mg/kWh.
Selection
Selecting the most appropriate technology to achieve low NOx will depend on the particular requirements of each project. The important thing is to be aware of the options available and make a selection in the light of specific project criteria.