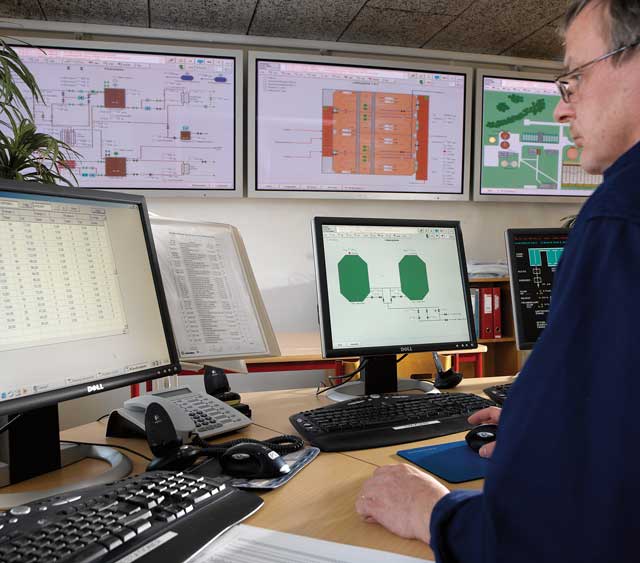
Energy is the biggest component of the cost of a pump over its lifetime. But that means there are big potential energy savings, says Andy Shearer, Grundfos Pumps director of sales for industry
Wherever you are, you won’t be far from a series of pumps that are performing a multitude of tasks. Pumps play a key role in every industrial process and application.
Despite the crucial role that pumps undertake, in process applications, heating, cooling, boiler feed, maintaining water pressure, distributing clean drinking water, removing wastewater, and supplying fire suppression systems, they tend to be largely forgotten about until there is a problem.
But pumps can also be serious energy wasters, leaving behind a significant carbon footprint. Conversely, this means that pumps stand out as offering potentially one of the biggest opportunities for savings in your business.
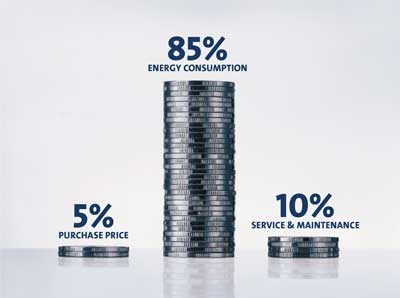
in the life of a pump
Pumps account for 10% of the world’s electrical consumption. It is estimated that two-thirds of currently installed pumps use up to 60% too much energy. This may be because they were originally oversized; are fixed speed types, which means they cannot adapt to meet the actual system demands; and they do not benefit from technological advances in aspects such as motor efficiency. If every company switched to a high efficiency pump system there could be global savings of 4% of total electricity consumption – comparable with the residential electricity consumption of 1 billion people.
When to replace/upgrade
It is rare for anyone to consider replacing a pump for any other reason than that it has reached the end of its life. Yet there are many opportunities when to do so would allow process improvement through system integration, leading to improved energy efficiency and therefore reduced emissions. Giving consideration to replacing individual pumps or whole pumping systems before it becomes essential can have a short payback period.
Pumps that operate in an industrial environment may require replacement for many reasons. When this happens, it offers the opportunity to review the system and make sure it is providing the most efficient solution for that particular plant or process against its individual blueprint. Whatever the circumstances, it is worth reassessing the situation, since, depending on the application, there could be large financial savings to be made by changing to a more efficient option.
At Grundfos, experience tells us that, for the most part, pumps are directly replaced like-for-like, without any extra consideration being given to any changes in demand or use since the original pump selection. This means that the opportunity to optimise a replacement selection is lost.
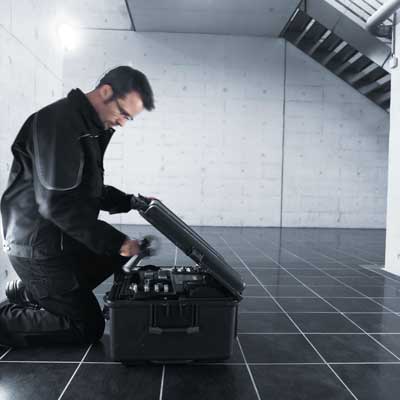
Check out your pump equipment
There is a better way. For example, if you want to quickly assess what savings could be realised in your current pump systems, contact a reputable pump company to undertake an energy check that will assess all the installed pump equipment and will look at the current and future demands of that system.
It will then produce a comprehensive report that will document any suggested changes and the potential savings that they offer, along with giving an overview of the return on investment, carbon dioxide saving and a complete lifecycle cost.
More sophisticated pump partners such as Grundfos Pumps can also provide multi-level energy optimisation assessments. These include
- a simple visual inspection of the pumps, installation and application
- monitoring real-time power consumption via wireless sensors linked to the cloud
- a pump audit in which flow, differential pressure and power are logged over 7-14 days
- thermodynamic testing, whereby differential temperature and power are measured to accurately calculate pump efficiency.
This data is then used to formulate reports that highlight potential savings and how improved control philosophy can bring about significant process improvements. This may include reduced water hammer and noise, leading to reduced maintenance costs and downtime; greater SCADA or BMS integration; system simplification by removing control valves; and improved risk management by removing obsolete pumps that can no longer be repaired or replaced.
Some real-life examples
To see the true value that such checks can actually deliver in real life, here are three examples of different types of companies which have all benefited from a pump assessment.
A well-known name in the UK brewery industry wanted to ascertain the efficiency of a particular area of their operation and approached Grundfos to assist them. An energy check was undertaken which showed a potential energy saving of 148,645kWh could be achieved by changing just two pumps. The payback period would be just six months.
The replacement Grundfos pumps have now been installed for some time and have achieved the promised energy efficiency, and also are proving to be very reliable. The pumps can be automatically slowed down at weekends when production is not as high, saving additional energy.
The facilities management company was so impressed with the results that they requested more energy checks be undertaken on other premises in their portfolio.
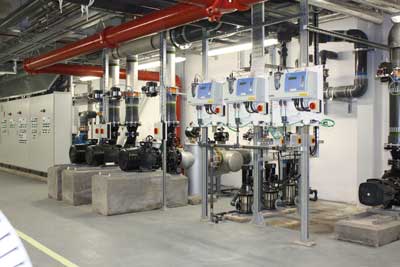
A pharmaceutical company in north-west England was using obsolete split-case pumps that were no longer capable of being maintained. An energy check was undertaken which showed that by replacing the pumps with new, properly sized, Grundfos split-case pumps a annual saving of 792,518kWh would be possible. In this instance the payback period was just 15 months.
In north-east England, a soft drinks manufacturer needed to review its provision for water-boosting because the existing system was not performing effectively. A new Grundfos MPCE variable speed booster set was indicated as being the solution, following an energy check. The booster set was duly replaced and the new set is saving 329,900kWh annually, which meant it paid for itself in 16 months.
Beyond the pump
These examples show the impressive return on investment that can be achieved, as well as the significant energy and carbon dioxide savings. But this is only the beginning of the story. Today pumps rarely operate in isolation, and therefore have the capability to feed into integrated and sophisticated systems covering a range of operational demands.
This means that even greater benefits are available through optimising the entire pump system using an intelligent control solution which adapts precisely to manage performance, energy efficiency, and reliability.
Digital future
The pump industry has been busy gearing up to play its role in the digital future. For example, cloud-based sensor systems allow you to monitor and control, react fast to alarms and optimise all the components in HVAC, boosting, and other systems. They offer easy-to-understand user interfaces, such as mobile apps. Built-in control algorithms make sure that your system is constantly operating with the greatest security, while using the minimum amount of energy.
This means that you can get instant access to information to monitor your systems and alarms, remotely access a range of information, optimise your overall system and gain the upper hand against downtime through predictive maintenance.
Summary
Pumps play a pivotal role in the industrial landscape. They could very easily be the source of impressive energy and carbon dioxide savings.