KSB valve sales manager Marc Walker provides a potted guide to the most important types
Since way back in history, there has been a need to control the flow of water to cultivate crops for farming. It is believed the flow of water would originally be regulated using a combination of branches, tree trunks and stones.
However, around the 5th century BC, the Romans were credited with inventing the first valves while they were creating a formal system of canals.
According to the Oxford Dictionary the term valve comes from the Latin word valva meaning “leaf of a folding door”.
Once the industrial revolution began the valve played a crucial part, and it still does today. Valves are used in almost any application influencing the flow of a medium. From home heating systems to the offshore oil and gas industry, from treatment and storage of water to liquefied natural gas transportation, from ships to breweries, from mining to nuclear, from pharmaceutical to cosmetic production, valves play a part in every process.
To cover such a large and varied spectrum of applications valves have evolved and diversified since Roman times. Although there are many variations available today, six core types are widely used: butterfly, globe, gate, ball, check and diaphragm, each with their own advantages and disadvantages.
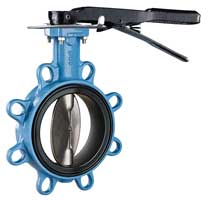
Butterfly Valves
Butterfly valves use a disc that rotates to open or close the valve. The disc is positioned in the centre of the pipe with a stem that passes through the disc. Even in the open position the disc is always present within the flow, so it induces a pressure drop.
In operation, butterfly valves are fully opened or closed by a quarter-turn of the handle or actuator. When the valve is closed, the disc is turned so that it completely blocks off the flow. When the valve is fully open, the disc is rotated a quarter-turn so that it allows almost unrestricted passage of the fluid. The valve may also be opened incrementally to control the flow of the medium.
There are different kinds of butterfly valves, each adapted for different pressures and uses.
Zero Offset or Centred Disc
In a concentric valve (zero offset), the disc rotates around the centre axis allowing for 360° rotation. Sealing is achieved by the disc deforming the soft seat seal. A low cost, easy to actuate valve with a bubble tight seal, it is generally used for low pressure systems.
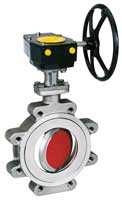
Double and triple offset
High-performance double and triple offset butterfly valves have been developed for higher-pressure systems. With either a soft PTFE or metal seat, these valves can be used for high temperature or cryogenic applications. The triple offset butterfly valve is the valve best suited for high-pressure systems.
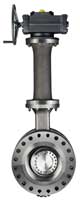
In the triple offset, the shaft is offset from the centre line of the disc seat and body seal (offset 1 in the diagram below), and the centre line of the bore (offset 2). This creates a cam action during operation to lift the seat out of the seal and decreases wear. The disc seat contact axis is also offset (3). This ensures friction-free stroking throughout its operating cycle. Contact is only made at the final point of closure.
The third offset solution has been engineered to eliminate deformation and friction, making its advantages clear for high pressure systems.
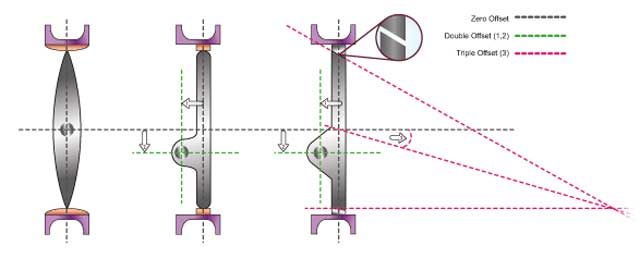
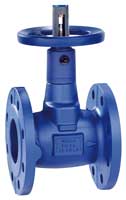
Globe valves
Globe valves are multi-turn valves with a linear motion, and are designed to stop, start and regulate flow. They derive their name from their spherical body shape. Globe valves have two chambers. The fluid flows into the bottom chamber, then into the one above. The disc of a globe valve blocks the flow from one chamber to the other; when in the fully open position it is totally removed from the flow path.
Globe valves may be used for isolation and throttling services. Although these valves have higher pressure drops than straight-through valves such as gate, butterfly and ball types, they may be used where the pressure drop through the valve is not a controlling factor. Globe valves with bellows-sealed sealing arrangements are often used for low-pressure steam applications.
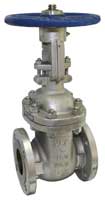
Gate valves
Gate valves, sometimes called sluice valves, are primarily designed to start or stop flow when a straight-line flow of fluid and minimum flow restriction are needed. In service, these valves generally are either fully open or fully closed.
When the valve is in the open position there is uninterrupted flow through the valve because the disc or wedge is completely removed from the flow path.
A gate valve can be used for a wide range of liquids and provides a tight seal when closed. Using a gate valve to regulate flow is not recommended as this will increase the wear and tear and will lead to leaks.
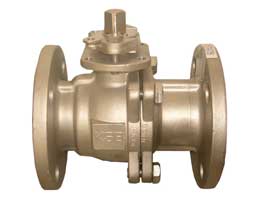
Ball valves
A ball valve is a quarter-turn rotational motion valve that uses a ball-shaped disc with a central hole to stop or start flow. The ball valve is an on-off valve and is opened when the ball rotates to a point where the hole through the ball is in line with the valve body inlet and outlet. When the valve is closed, the ball is rotated so that the hole is at 90° to the flow.
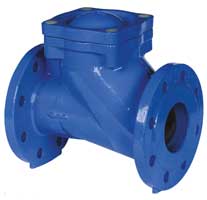
Check valves
A check valve, sometimes known as non-return valve, is a valve that allows fluid to flow one way only. The check valve is a common type and versions of it can be found in many household items.
There are various types of check valve: swing type valves, twin plate, piston, and ball type valves. All work in much the same way. The plate, diaphragm or disc acts a stopper, resting in the seat, until the fluid builds up enough pressure to move the stopper and allow the fluid through. This pressure is known as the “cracking pressure”, and must be calculated beforehand to ensure you have the correct check valve.
The check valve works completely automatically. There are other benefits of using a check valve. Making sure that there is no reversal of flow or flow-back protects pumps and system equipment. Check valves help to maintain low pressure, which helps with energy savings. They also help to prevent water hammer.
An arrow stamped on the body of the valve indicates the direction of flow.
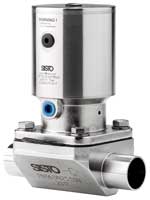
Diaphagm valves
The diaphragm valve was originally developed in the goldmines of South Africa.
They are excellent for controlling the flow of fluids containing suspended solids. Diaphragm valves are available in two basic forms: weir type and straight-through types. The weir type has a weir formed in the body. As the diaphragm is screwed down to close the valve, the diaphragm is pressed against the weir stopping the flow, which creates a pressure drop allowing the valve to be used for regulating services.
In the straight-through type the body bore is circular. The straight body offers minimum resistance to flow in the open position and therefore is well suited to slurries.
The diaphragm valve works well with corrosive and abrasive fluids.
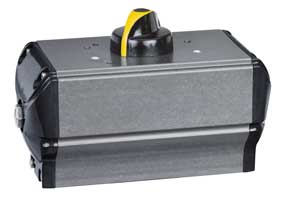
Actuators
A valve actuator is the mechanism for opening and closing it. Manually-operated valves require someone to physically open or close the valve, using a direct lever (for quarter turn valve types such as butterfly and ball), or hand wheel (for multi-turn valve types such as globe and gate).
Powered actuators using hydraulic or air pressure or electricity allow a valve to be operated and adjusted remotely. Valves with actuators may be the final elements of an automatic control loop which automatically regulates and controls a flow process.
The valve has come a long way since Roman times to become the sometimes overlooked part in the process – but the humble valve plays a key role. As a result there is now a valve for every process – it’s just a matter of selecting the right one.
www.ksb.com
products.ksb.com/global/
ValveSalesUK@ksb.com
Telephone: 00 (44) 1509 231872