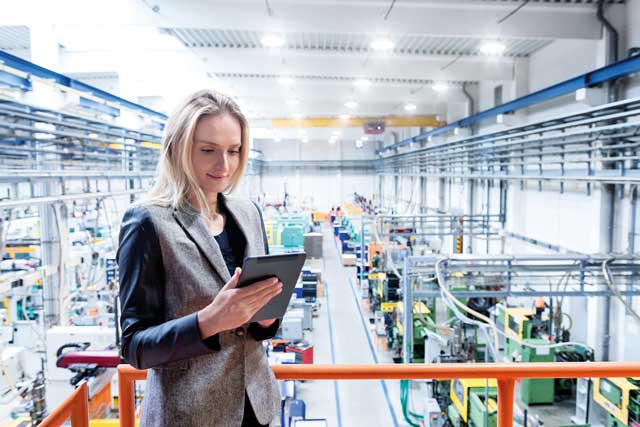
Dave Sutton, automation, HMI and connectivity manager at Schneider Electric, explains how the industrial internet of things is allowing companies to take the first steps towards digitalisation with the minimum of disruption
Over recent decades traditional automation control systems have increasingly provided smarter manufacturing methods, improving industrial process efficiency and productivity, while reducing downtime. Reactive maintenance has been replaced in the main by active maintenance, driving down the time and money spent diagnosing, fixing and testing.
As the whole production process becomes more efficient, businesses are wondering where the next wave of improved productivity will come from. Most are banking on data analytics and the industrial internet of things as the next big breakthrough. But the introduction of the technology brings significant considerations, such as how to collect and interpret the data in a secure way.
Existing installed automation control systems are not necessarily equipped, or flexible enough, to take up this challenge. New generation IIoT Node-RED based technology is helping to bridge the gap with low-risk solutions that provide a direct connection between manufacturing data and the cloud, without the need to modify existing automation control systems. This makes it easier for businesses to introduce IIoT technology and see its benefits, in a cybersecure environment.
The evolutionary journey to IIoT
The IIoT is a natural evolution of control systems
The size, capabilities, and complexity of control systems have increased rapidly in recent decades. The increasing volume of process and machine data in industrial settings is astronomical. By 2020, there will be an estimated 50 billion “things” connected to the internet, and an increasing share of these devices will be industrial assets.
IIoT connectivity provides a common platform to develop new digital services, improving the efficiency and reliability of all sorts of machines and industrial processes, and connecting plant, field and cloud applications. It will be essential to exploit the power of big data and translate it into business value.
The IIoT consolidates data analytics from a range of assets in different locations. It aggregates the data and seamlessly provides analytics at the cloud level, building digitalised smart factories and improving responsiveness.
Traditional systems – barriers to IIoT?
Existing control systems may not be flexible enough to adapt to changing business conditions. Traditional control systems operate with a limited scope of data. Data collected and used from existing control systems is only a small fraction of field data. Data is sometimes difficult to extract, integrate, and comprehend. It’s even harder to drive dynamic, actionable intelligence back into operations to improve productivity.
This is where IIoT comes in – but making changes to introduce IIoT connectivity at both the device or operational technology level and cloud or information technology level can present obstacles. Control system applications and programming languages may be challenging. Making changes requires skilled personnel, and may require authorisation, re-testing and re-validation. It can require assets to go out of service while updates are made.
In recent years automation devices have increasingly been connected to web servers, allowing access from browsers. IT software technologies that manage open communication from the plant level, such as OPC, .net and SQL, have become common. This was the foundation of IIoT.
New IIoT technology builds on IT/OT convergence, which involves high levels of cooperation between IT and operational technology groups in charge of monitoring physical devices such as valves and pumps. Open source Node-RED software can simply wire the “things” from the field to the cloud applications without the need to modify existing automation control systems.
Extensive node libraries are openly available from the rapidly growing Node-RED community. This represents a quick, low-risk path to the IIoT.
Node-RED
Node-RED is a tool for integration between automation and IT functions that have traditionally been fragmented by different programming languages and systems. It provides a web-based integrated environment to build and deploy operations.
Originally developed by IBM in 2013, Node-RED has evolved into a simple, open source graphical programming tool for designing the communication data flow from OT to IT.
Thousands of nodes are available ready to use, to get data from connected products, manage communication, and connect to IT systems.
IIoT Edge Box
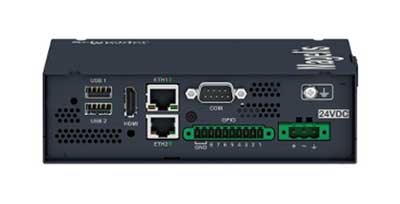
Schneider Electric’s Magelis IIoT Edge Box, with Node-RED pre-installed, is a robust industrial edge device, requiring no maintenance, and designed to run in harsh environments. It stands alongside (in parallel to) the existing automation control system, minimising plant disruption.
It connects to and collects data from field devices, and provides a wide array of connectivity options, hard-wired I/O, and remote access via Wi-Fi or 4G, plus options including blind box or local operator screen, expansion accessories and operating system options for Windows 10 and Linux. It is natively cybersecure. Node-RED can be configured for one-way communications only, so device data is accessible in read-only mode. IIoT Edge Box also incorporates cybersecurity features such as end-to-end data encryption.
Conclusion
Businesses are demanding integration of IIoT with the entire value chain on factory floors. The Magelis IIoT Edge Box provides a first step towards IIoT and IT/OT integration without the need to change or stop the existing control system. With smarter data, operational efficiency can be improved globally.