As with any asset, robots will run at peak efficiency when operators have access to predictive maintenance tools. Barry Weller, product manager at Mitsubishi Electric, looks at how AI-based predictive analytics can support predictive maintenance of robots and how this can benefit users.
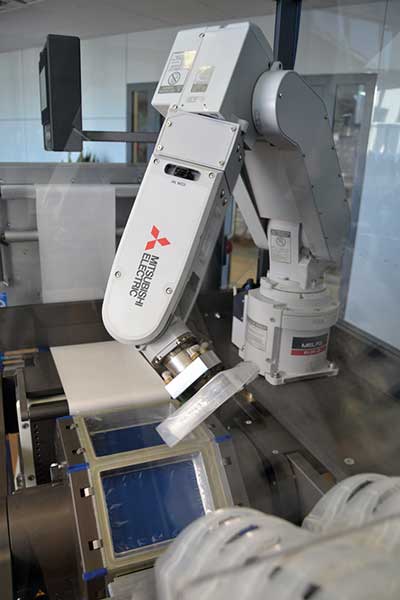
Both standard industrial robots and collaborative robots can create new opportunities for streamlining production and assembly operations. But like any other machine, robots require maintenance to optimise their performance.
To forecast when a piece of equipment is likely to fail, predictive maintenance algorithms process and analyse data collected from different sources to build a model that can provide useful insights on the status of a robot.
Artificial intelligence systems are the most useful tools to recognise patterns, make predictions and give practical advice on actions to take. By using a range of technologies, AI shows an unmatched ability to process large volumes of data to identify patterns in it and generate predictive models.
These can help to accurately calculate wear and consumption for different robot components, or identify trends suggesting a component is about to fail. Examples of relevant information that AI-based predictive maintenance can use include machine operating conditions, components’ average service lives, frequency of specific robot motion patterns or real-time data from the drives.
The raw data results obtained may be clear to the AI system, with its ability to crunch the numbers. However, they may not be straightforward for humans to interpret. As a result, visualisation is a key aspect of AI-based predictive maintenance, because it presents the information generated by the model in an accessible and immediate way to plant and maintenance operators.
This leads to knowledge that informs meaningful decisions and quick action, without the need for specialised skills or training in data mining. A direct result is efficient maintenance schedules that maximise equipment use or intervene before breakdowns occur.
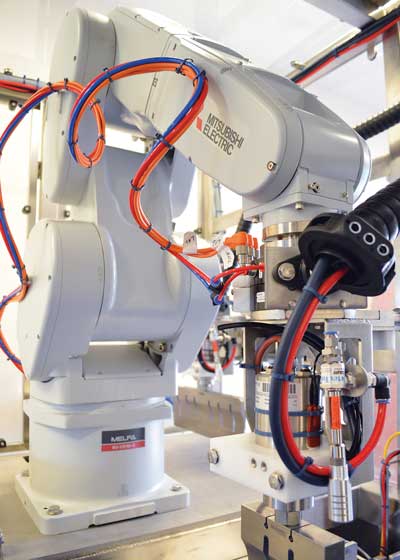
Making the step towards maintenance 4.0
Users of Mitsubishi Electric industrial robots now have direct access to this type of solution, because artificial intelligence is embedded in the company’s latest MELFA SmartPlus software for its FR-series intelligent robots. The system is built into the robot controller and offers three main functions.
Consumption degree calculation determines when parts such as ball screws and ball splines, gears, bearings and belts are likely to need replacement. Whenever maintenance is required, the system can send clear notifications.
The second function offers maintenance simulations. By aggregating the data used by the consumption degree model, the AI system can estimate the robot’s service life. It can offer a maintenance schedule that optimises maintenance costs and takes into account the operating conditions and activities performed by the robot. Thanks to this function, users can understand, schedule and optimise robot maintenance even before installing the machine on the factory floor. This helps to provide them with the confidence that their robot investment will be worthwhile.
Finally, the AI system offers a centralised robot management platform. The data from SmartPlus can be loaded to multiple cloud-based analytics solutions and will interact with upper-level enterprise systems to combine their data with maintenance data from the robot controller. In this way, the solution can provide highly reliable predictive models.
Sometimes it is easy to forget that Industry 4.0 and Big Data mean not only intensifying processes, but also supporting maintenance activities. By applying AI-based predictive maintenance to their robots, industries can maximise the efficiency and productivity of their automated systems.