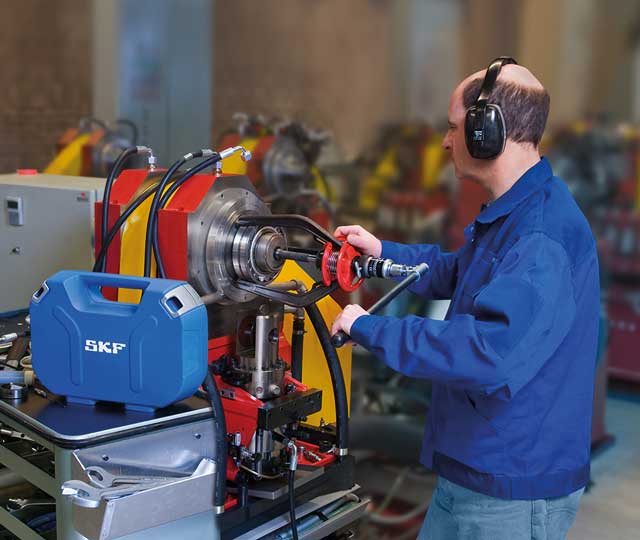
Every maintenance engineer knows that bearings need to be mounted correctly. But care is equally necessary when removing them, as Mark Townsend, SKF mechanical services and service engineering manager explains.
Bearings are precision components. Appropriate installation, alignment and adjustment are essential for efficient running and a full operating life. When a bearing has to be removed, however, it can be tempting to take shortcuts,
That’s a mistake. Hitting a bearing with a hammer risks damage to shafts, housings and other components, creating problems that could jeopardise the future reliability of a machine. Removal doesn’t always mean it’s the end of the life of the bearing itself. Though it is best to leave a healthy bearing in place, disassembly may be required to gain access to other components.
If the bearing involved is at an early stage in its life, remounting the same unit may be preferred to the installation of a new component. Or the organisation may want to return worn bearings to the supplier for remanufacturing, a strategy that has both cost and environmental benefits.
There are four recommended methods for dismounting bearings: manual removal with appropriate tools; hydraulically-assisted removal; oil injection; and the application of heat. The size of the bearing is the most important factor in deciding which method to use. Small bearings, with a bore diameter of 80mm or less, can usually be removed using mechanical tools. Larger bearings require greater force, often necessitating hydraulically-assisted or oil injection methods.
Manual removal
Small bearings can be removed from the shaft using a mechanical puller. The tool has claws that hook on to the bearing inner ring or an adjacent component. Force is then progressively applied using a screw mechanism. Where possible, the shaft should be supported in a bench vice to avoid damage during removal. If access to the inner ring is not possible, the bearing can be withdrawn via the outer ring, but re-using it is not recommended because the forces involved in removal might damage raceways or rolling elements.
Hydraulically-assisted removal
In the case of larger bearings, or those mounted with an interference fit, hydraulically-assisted removal tools are capable of generating the higher forces required. Some removal tools have screw or hydraulic options, allowing selection of the most appropriate approach for a given task. Pullers are available for bearings with outside diameters up to 500mm.
Oil injection
Some machine designs incorporate special features for easy bearing removal. If the shaft is equipped with a suitable duct and distribution groove, high pressure oil can be injected between the shaft seat and inner ring bore until an oil film completely separates the surfaces. The bearing can then be removed from the shaft with little force.
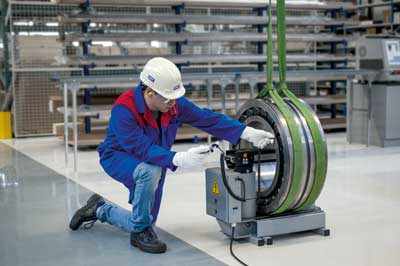
Heat
The controlled application of heat can be used to expand a bearing, creating clearance between the inner ring and shaft. Heating rings or special induction heaters can be used to apply heat with the necessary precision, but this is a specialised technique, typically only used as a last resort.
Safety and environmental considerations
A key factor in any bearing dismounting procedure is preparation. The area should be thoroughly cleaned and suitable equipment should be available to capture any lubricant released during bearing removal. If reinstatement of the bearing is expected, its relative position against the shaft or housing should be marked before removal. If an undamaged bearing is remounted, the non-rotating ring is usually turned by 120 to 180 degrees to ensure that a different part of the raceway is in the load zone.
Some bearing arrangements, such as those fitted to tapered shafts or with adapter sleeves, pose the risk of serious injury when dismounting. Appropriate steps must be taken to prevent this, for example by installing a locknut on the end of the shaft to limit the bearing travel when it comes loose.
Bearings are precision-engineered components that deserve to be treated with respect throughout their life. The way you remove one bearing can have a real impact on the performance of its replacement, and on the long-term health and reliability of your machinery
www.skf.com | +44 (0) 1582 490049