
Well-designed machine guarding can improve rather than hinder efficiency, argues Steve Allen, national sales manager at Procter Machine Safety
Machine guarding has a significant impact on the efficiency of both the production process and maintenance. Poorly designed guards hinder access and increase cycle times, as well as impeding maintenance. Furthermore, awkward guards are more likely to encourage unsafe practices such as defeating interlocks or not replacing fixed guards after their removal for maintenance. Should an accident occur, the injuries sustained and the costs – both direct and indirect – will prove the foolhardiness of penny-pinching on machine guarding.
Guards are key to the interaction between operatives and the machine: depending on the process, guards might be opened once per machine cycle, periodically for cleaning or clearing blockages, or for maintenance. Simple features such as well positioned vision panels can reduce the number of times guards are opened, or in some circumstances light guards or pressure-sensitive mats can replace physical guards and cut cycle times. When large areas need to be accessed, heavy guards can be improved by the use of counterbalances, springs or powered actuators.
Hinges and linear guides on movable guards must be sufficiently robust for the application because premature wear can make the guards difficult to operate. The same wear can also cause interlock switches and their actuators to become misaligned, leading to safety circuits not being completed when guards are closed or false signals being generated due to vibration. Glazing in vision panels must be resistant to scratching, or replaced when it becomes obscured, otherwise there may be a temptation to open the guard for process viewing, which may lead to a longer cycle time or a loss of quality.
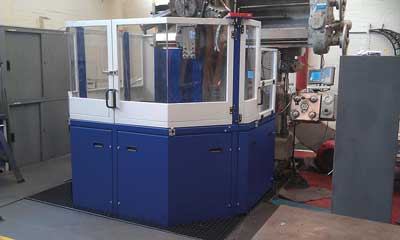
Close-fitting guards are often installed on hazardous machines, but larger processes may be better protected by perimeter guarding. In this case, the height of the guarding and the distance from the hazard must be appropriate (this is covered by BS EN ISO 13857). If the guarding is located further from the hazard than is necessary, valuable floor space is lost.
When maintenance is required, whether planned or unplanned, guards must be removed quickly and easily to gain access. Correctly designed guards will be held in place by the minimum number of fasteners possible, and the relevant standard (BS EN ISO 14120) requires the use of retained fastenings for fixed guards. Many different styles of retained fastenings (captive screws) are available, but it is important to use robust fasteners because some types are inherently difficult to replace if damaged. Fixed guards should also be designed so their replacement is unambiguous, as incorrect fitting could leave hazards exposed.
Two of the main guarding standards have already been mentioned, but there are numerous others with which machine guards must comply, and even more standards are applicable when guard switches and interlocks have to be incorporated within a machine’s safety-related control system. However, though compliance with standards is a black and white issue, it takes experience and expertise to know what an HSE inspector will expect to see when assessing whether risks have been reduced to a level that is as low as reasonably practicable (ALARP).
Procter Machine Safety has a team of qualified and highly experienced specialists who can conduct surveys to check machine guarding compliance with standards, and it can also undertake machinery inspections under the Provision and Use of Work Equipment Regulations (PUWER). The full service offering extends to on-site machine surveys and risk assessments, plus design, manufacture and installation of bespoke machine guards, complete with electrical aspects such as connecting interlocks to a safety-related control system. In addition to close-fitting guards, the company offers standard modular or bespoke perimeter guarding in steel or aluminium, acoustic enclosures and access platforms.