Variable speed drives rarely trip because they are faulty. It is more often because they have just protected the motor or the application. ABB Motion’s Andy Preston gives an insight into the functions that can save your process from downtime.
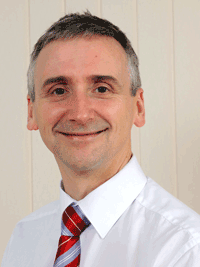
Whether a motor vehicle or an electric motor, keeping any engineered product at the peak of its performance requires a well-planned maintenance schedule. And variable speed drives (VSD) – used for regulating the speed and torque of motor-driven applications – are no exception. However, VSDs themselves rarely fail. Often, when a drive trips or flashes a warning message, it is not the VSD that is failing, but usually a signal that an error has been detected in the motor or the load.
In fact, a VSD acts like an early warning system that helps protect a plant with an array of built in diagnostic routines, protection functions and assistants.
Take a typical food production facility, where blockages are a common occurrence. Most motor-driven machinery will repeatedly attempt to drive through the obstruction, causing a spike in current. In a direct-on-line system the increased current can seriously damage the motor or other equipment. In a VSD-controlled system, the drive, detecting the spike, will trip out, cutting power to the motor and preventing expensive damage from occurring.
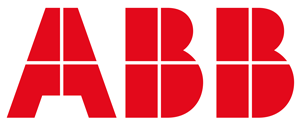
Today’s VSDs boast an extensive array of advanced features for analysing and resolving issues before they can become major incidents. Accurate and reliable diagnostic information is obtained through warning, limit and fault words. Dataloggers store critical values before and during an event, such as a fault. Real-time clocks allow the end user to see the exact times of events, enabling patterns – and therefore likely causes – to be identified. Additionally, built-in supervision and adaptive programming features and messages can be employed to monitor and pre-warn about many specific plant conditions, making the drive an integral part of the protection system surrounding an application.
This information can be easily accessed – and interrogated – using the latest generation of highly intuitive VSD keypads. Information is flashed up to users by way of simple icons, hint tips and help screens. Problems are communicated in plain English, rather than complex codes, cutting response time.
Similarly, fault names and descriptions can be customised, and service contact details added/displayed on the keypad screen. Fault help screens show users where to look if there is a problem. Trip histories allow users to spot patterns, with the trips and warnings time-stamped so that the frequency of a problem can be easily tracked. Preventive maintenance can then be arranged before a catastrophic failure. Time-stamping of faults makes tracing easier. The ability to log faults from a “system time” (not just the keypad) allow problems across an entire process line to be compared, synchronised and diagnosed.