Prescriptive analytics powered by peak impact detection simplify equipment diagnosis and bring it to the control room says Gary Ingram of Emerson Automation Solutions.
Analysing vibration data from rotating equipment makes possible the early detection of problems such as misalignment, gearbox meshing issues, insufficient lubrication, pump cavitation and rolling element bearing defects. This helps to prevent unexpected failures that can cause safety incidents and production loss.
Traditionally, though, vibration data is usually never routed to a plant’s control room. It requires specialised training and tools to extract useful information, and it does not offer information that operators can use to improve plant operation. Correctly interpreting vibration data is a specialist skill, and companies may not even have maintenance engineers with the necessary experience.
However, by using peak value detection, a non-specialist control room operator can identify when a machine is developing a problem, and even gain insight into the severity of the problem.
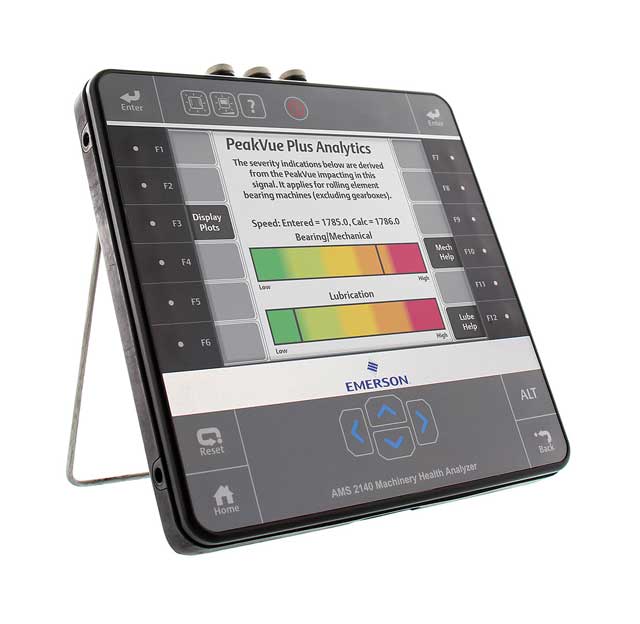
Peak value detection
Traditional vibration analysis relies heavily on a signal processing technique called the Fast Fourier transform, which converts the signal into a vibration spectrum. This can provide an analyst with information to help determine the source and cause of any problem. But this process requires specialised skills, and it also loses critical information about the amplitude of the original signal.
In contrast, peak impact detection effectively filters vibration signals from the shaft rotation to focus on “impacting”, where metal parts come into contact with each other. This is a key indicator of the four most common issues leading to equipment failure: rolling element bearing defects, under-lubrication, gear defects and pump cavitation.
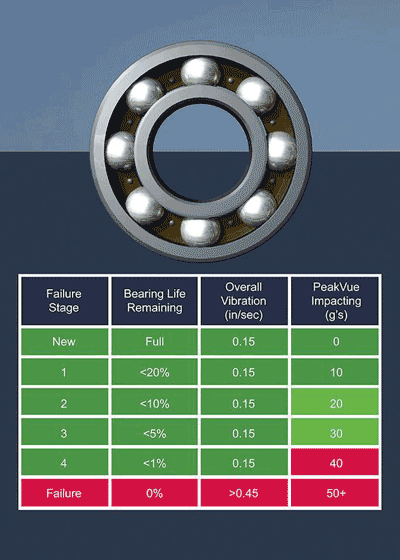
Peak impact, used by Emerson’s PeakVue technology, is in fact a measure of “stress wave” activity in a metallic component. Such stress waves are associated with impact, friction, fatigue cracking, and so on. For example, when a rolling element impacts a defect on a bearing raceway, it will generate a series of stress waves that propagate away from the location of the defect. This will create a response in a motion sensor such as an accelerometer or a strain gauge. Common defects which generate stress waves are pitting in anti-friction bearing races, fatigue cracking in bearing raceways or gear teeth (generally at the root), scuffing or scoring on gear teeth, cracked or broken gear teeth and others.
Peak impact detection technology provides a simple, reliable indication of equipment health. It generates a single value, which can be plotted over time against pre-determined alert limits to provide a simple interpretation of machine health to non-specialists.
Identify faults
Peak values are observed over discrete time intervals and then analysed. They are much easier to interpret. A healthy machine that is correctly installed and well lubricated shouldn’t be experiencing any impacting and the peak value measurement should be at, or close to, zero. As a fault such as a rolling element bearing defect begins to develop, the peak value reading will increase in proportion to the severity of the problem.
For a typical process pump, when the value reaches 10, there is a problem with the machine. At 20 there is a serious problem, and when it reaches 40 the problem is critical.
This simple rule makes it easy to identify when the machine is experiencing a problem and how serious the issue is.
Once an abnormal situation has been identified, detailed diagnostic information can be extracted from the peak impact waveform or spectrum to verify the nature of the defect.
Prescriptive analytics
In a recent advance, peak impact detection has been combined with prescriptive analytics to help further automate the analysis process. By embedding expertise into the peak impact detection algorithms, it is possible not only to see when a fault is developing, but also to obtain an indication of whether it is caused by under-lubrication or a mechanical problem, such as a bearing defect. This quickly identifies the root cause of the issue, shortening the path between problem detection and resolution to avoid unplanned downtime.
Stress wave analysis is a powerful complementary tool that can detect a range of faults and problem conditions that techniques such as vibration analysis alone might miss under certain conditions.
With the help of prescriptive analytics, field technicians and control room operators alike can make timely, corrective decisions that lead to increased equipment reliability and an overall improvement in plant efficiency.