It is more important than ever that industrial employers understand their legal responsibility to make sure their technicians are competent to carry out their tasks. John Saysell, director of training for MCP, outlines alternative approaches
The first stage in any exercise of this type is to define competence. In simple terms, it means that the task is done safely, to the right standard, within a reasonable length of time. Over the past 20 years competence has come to the forefront of MCP’s discussions with industry.
There are two main approaches to establishing training needs, namely the classic Training Needs Analysis (TNA) and a Competence Based approach.
The classic TNA is a much broader way of examining what maintenance technicians could get involved in. The competence-based approach is narrower, but an output from it is actual evidence of competence.
Among the gains from a training and development plan are opportunities to improve morale, motivation and job satisfaction; improve performance and customer service; and clearly define maintenance roles. It will help you to improve staff retention and comply with legislation, as well as providing accurate evidence of competence and embedding a transparent grading structure. It will allow you to align training with business needs and reduce reliance on contracted staff.
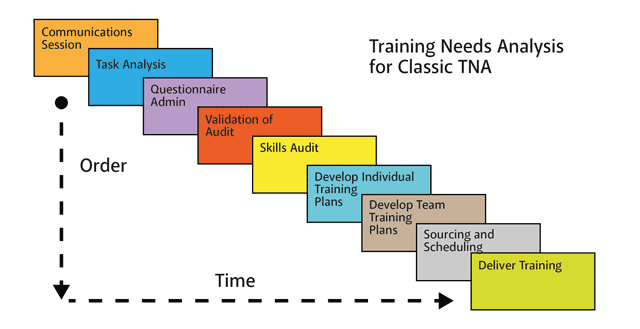
It is important to involve all stakeholders from the outset. In initial communication sessions, a brief presentation is made, outlining the process, and explaining how this method is objective, fair and recognised as best practice.
In task analysis, vocationally competent maintenance engineers walk the job with the technicians, listing each task undertaken. A questionnaire is then prepared.This is a typical technical experience questionnaire (top right). The numbers in red are the desired numbers of competent staff. The next column is the actual numbers of competent staff. The skills gap, or training need is the difference.
Technicians have their questionnaires administered in groups of five to ten. The questionnaires are then validated by the technicians’ first line manager.
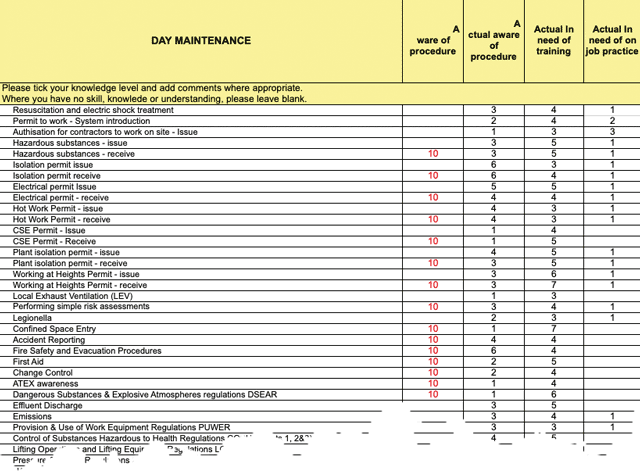
Skills audit: Depending on the job role and mix of tasks and skills, it will be possible to identify an ideal skill set for certain groups. Candidates can then be audited against this.
Individual training plans will be a product of the skills audit and are linked to the organisation’s business needs. If it is appropriate, it will also be possible to identify team training plans at this stage.
Training providers are then identified to deliver off-job and on-job training. Candidates will demonstrate competence and be signed off or, importantly, retrained.
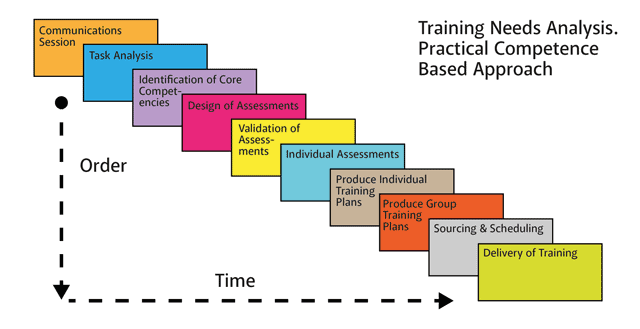
This approach is appropriate both for existing staff and new recruits. Assessments that mirror the maintenance tasks will need to be written. Typical assessments could include scenario or competence-based interviews and psychometric tests. Practical tests could include a PLC or electro-pneumatic fault finding rig test; belt/chain alignment; stripping and reassembly of a pump and so on.
As above, communication sessions are held in which a presentation is made to stakeholders. Vocationally competent maintenance engineers walk the job with the technicians to undertake task analysis, listing each task.
From the task list a number of core competences (say 20) will be reviewed. Some of the tasks will be appropriate for the higher level technicians and some for the lower level.
Assessments are developed working closely with the engineering team. They are validated and dry runs carried out.
Assessments are carried out and feedback is given on candidates’ performance. Prioritised individual and group training plans are provided.
Training providers are identified at this stage to deliver appropriate off-job and on-job training. Candidates will demonstrate competence and be signed off or retrained.
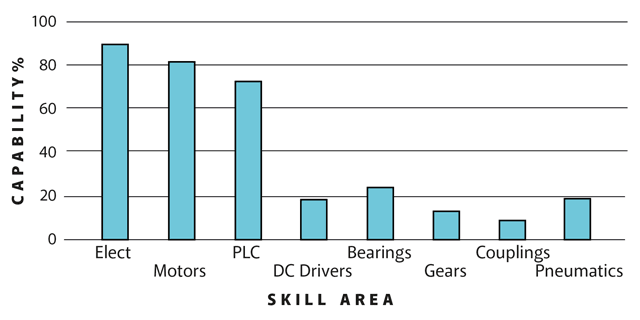
This profile graph shows an electrician working in a dual skill electrical/mechanical role. The chart shows good capability in core skills, including knowledge of programmable logic controllers. In this case the profile indicates potential development needs in mechanical skills and DC drives.