Acoustic emission testing can improve the operability of lifting equipment and identify minor damage or defects at an early stage. Dr Alessandro Demma, director of Omnia Integrity, explains.
Lifting equipment is widely used in many industrial sectors to move both heavy goods and people. These lifting systems range from relatively small bucket trucks to very large cranes.
The safe operation of lifting equipment is regulated in most countries. For example, in the UK the HSE issued in 1998 a regulation for lifting equipment (LOLER) requiring a thorough examination and inspection at 6 to 12 month intervals, depending on the case.
In the meantime, new technologies and approaches based on acoustic emission have been developed and applied to improve both safety and operability of lifting equipment.
Acoustic emission makes it possible to “listen” for minor damage or defects in the structure. By mechanically loading the structure, the material undergoes changes, for example as a result of formation or enlargement of a small crack. This results in a small local displacement, which generates a stress wave that can travel far from the source of the crack. The wave can be detected by a sensor which works in a similar way to a microphone, so that the sound can be analysed. Acoustic emission is therefore one of the few NDT approaches that enables a large structure to be inspected with only a few sensors.
Acoustic emission for inspection of bucket trucks
Bucket trucks are in many cases made of both steel (for the lower lifting arm) and fibreglass (for the top). Fibreglass is used for electrical isolation.
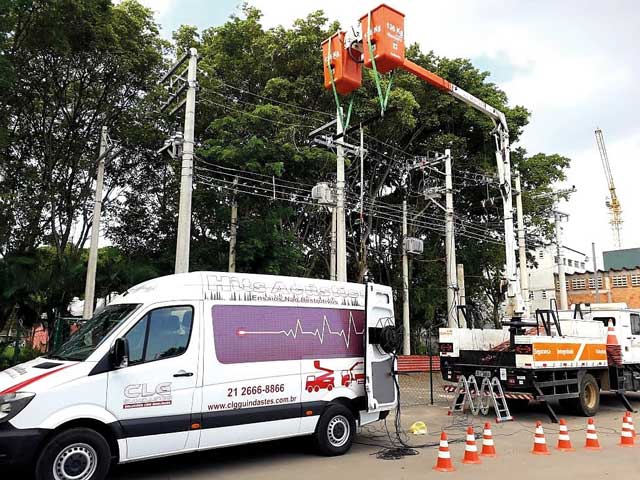
The inspection of fibreglass is not very common and standard non-destructive testing methods cannot be easily applied. Acoustic emission (AE) can be used on both steel and fibreglass, and with 12 sensors it is possible to inspect the entire structure.
New standards have been developed in the US (ASTM F914) and Brazil (ABNT 16593) recently, and in Brazil it is now mandatory (regulation NR12) to inspect bucket trucks using AE.
The testing procedure uses a load cell to stimulate the structure, and acoustic emission sensors are used to listen for potential damage.
Acoustic emission for inspection and monitoring of cranes
Cranes are large structures used in many industries. A catastrophic crane failure may cause harm to people and to other structures and it certainly causes downtime and consequential loss of business. A crane failure in an offshore platform may require temporarily stopping operations, as it is vital to have such a structure functioning on board.
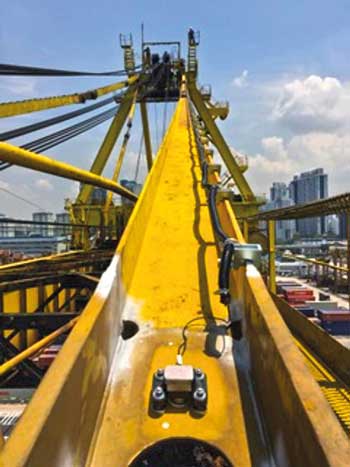
On offshore cranes it is common to carry out, additional to NDT inspection, regular loading tests, typically going to up to 125% of the crane’s rated load. Loading tests are recommended either by the manufacturer of the crane or the crane operator. However, there have been many examples of crane failures during load tests.
There is inherently an element of risk to the structure associated with load tests, and when they are carried out it is recommended that the test is monitored using AE. AE monitoring provides an early warning of structural damage and provides a tool to stop the test before failure. The AE device locates the area of concern with enough precision to follow up with further NDT techniques to size the damage and repair the area affected.
More recently acoustic emission specialist Vallen Systeme’s AE system has been used to monitor cranes continuously. This approach enables the risk of downtime to be eliminated entirely.
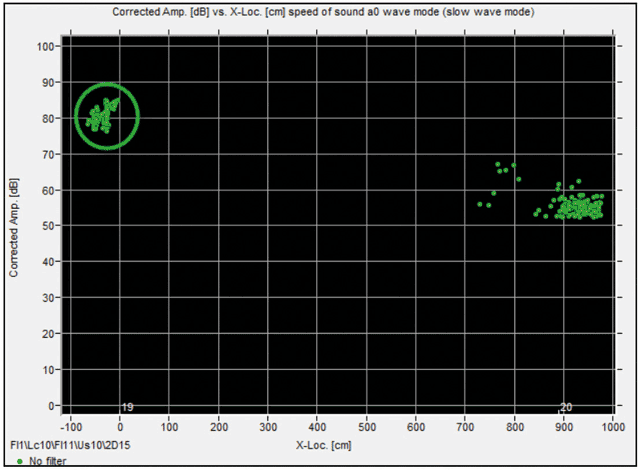
The graph above shows at the top left a cluster of acoustic events at about 80 decibels. This was due to a crack identified on a crane while it was being monitored. An alarm was sent to the crane operator. The area of the crack was identified and repaired before any irreparable damage was caused to the structure.
An ISO standard was specifically developed and published in 2018 for the inspection of cranes using AE (ISO 19385) and this can be used as a reference for implementation of an AE crane inspection programme.
Operability optimisation
Acoustic emission inspection or monitoring of lifting equipment improves safety while reducing downtime and potential consequential loss. Some countries have already adopted acoustic emission as the standard way to inspect lifting equipment and more are likely to adopt this method in the future.
Further information:
alessandro.demma@omniaintegrity.co.uk
www.omniaintegrity.co.uk | +44 7555731242