A collaborative R&D process lay behind the development of a new generation of burners with greater efficiency and reduced emissions, says Chris Horsley, Babcock Wanson UK process engineering director.
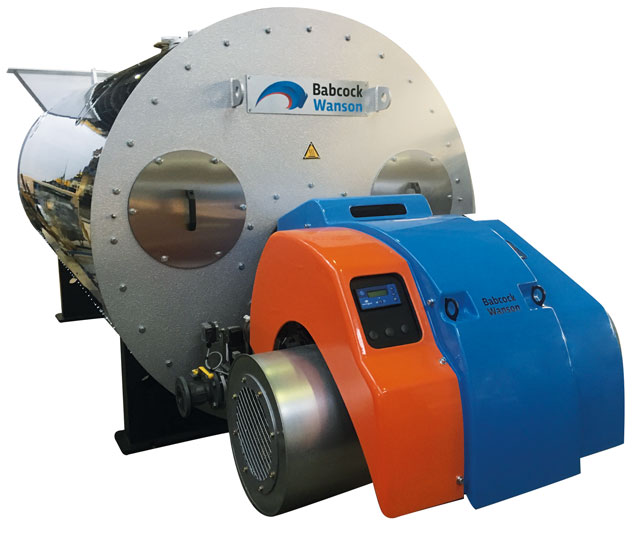
In all walks of life, doing things more efficiently and limiting the environmental impact of activities should be at the forefront. In manufacturing and process heating, great strides have been made. But there is always more to do.
Recently, Babcock Wanson led the DEMOXYA research project, in collaboration with the Poitiers-based Pprime Institute and Bertin Technologies, with the aim of reducing emissions and improving the energy efficiency of burners. It was awarded funding by ADEME, the French environment and energy management agency, as part of a call for projects in support of R&D programmes aimed at improving air quality.
The collaborative project had two objectives – the reduction of nitrogen oxide (NOx) emissions generated at combustion plants which consume fossil fuels, and the improvement of energy efficiency by virtue of an increase in the modulation rate of the burners.
A new generation of Babcock Wanson “Optimo” burners has resulted from the project. The first two burners available in the range are Optimo 1, for smaller output boilers with a capacity of 1 to 2 t/h, and Optimo 2, for medium size firetube steam boilers ranging from 2 to 4t/h output. The Optimo range is not only suitable for use on new steam boilers, but can also be retrofitted to existing boilers to meet tighter emission requirements.
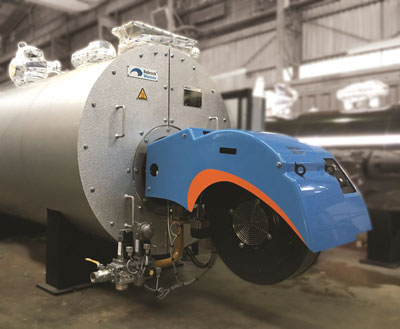
Designed with a high-performance combustion head, Optimo not only meets the requirements of the Medium Plant Combustion Directive, it can be configured to provide even lower emissions where regulations demand. Optimo 2 emission rates in standard form, for example, are less than 100mg/Nm³ NOx throughout the firing range when burning natural gas.
The Optimo has been designed for energy efficiency, achieved through precise control of low excess air levels throughout the turndown range, resulting in high combustion efficiency regardless of the process load. In addition the burner performs with a very high turndown ratio, enabling it to adjust its output to meet the needs of the process. This avoids the costly energy losses incurred by continual stop/start cycles, and further adding to operational efficiency.
Electricity consumption has been reduced through the introduction of interchangeable combustion air fans. This allows the Optimo burners to be perfectly matched to the boiler requirement and allows greater burner turndown, with reduced electricity consumption when operating at lower power levels. The wide fan range means noise is reduced when using lower fan powers. With a new burner casing design, additional sound insulation can be supplied where required.
The new casing has all the electronics of the combustion equipment integrated directly into it, facilitating its interface with a customer’s plant. This, combined with a new burner management system, make it easy to install and to handle, set up and use in daily operation.
The aim of the project was to improve energy and environmental performance. At the same time, it allowed Babcock Wanson to undertake a complete overhaul of its burner manufacturing process, with the aim of bringing to market burners with the latest technologies at the best possible price.
www.babcock-wanson.com | info@babcock-wanson.co.uk | 020 8953 7111