Instantaneous hot water systems are common in the process industries. Spirax Sarco business development manager Angelo Giambrone explains how to maximise their effectiveness.
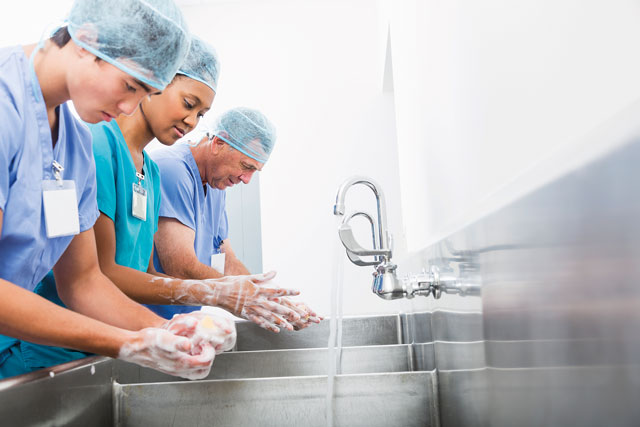
How can hot water be generated on demand, without the need to store it? Over the last 20 years or so, there has been a shift in the way hot water for both process use and hand washing is produced. Traditionally, storage calorifiers were used, consisting of a large tank capable of generating heat within a mass of water, using a heat transfer coil heated by steam. The problem with this method is that the stored water radiates heat, which limits efficiency levels, as well as potentially creating a point of risk for legionella.
A modern solution is plate heat exchange technology. Plates can provide high levels of heat transfer in a very compact housing, generally around a third of the size of an equivalent calorifier. The rapid heat transfer makes it possible to produce hot water instantaneously, eliminating the need for large hot water storage tanks, removing the inherent standing losses and reducing the legionella risk.
Steam is the ideal medium to distribute large quantities of thermal energy around site to heat water at a rate to suit the demand. Steam contains large amounts of energy, typically 23 times as much per kilogram as a water system. The result is smaller and lighter pipes, and less space needed in the plant rooms and ducts – a compact, pump-free way of distributing large amounts of energy around the site.
The importance of supplying dry steam must be considered when designing a new installation or managing an existing system. Distributing the steam at high pressure keeps pipe sizes small.
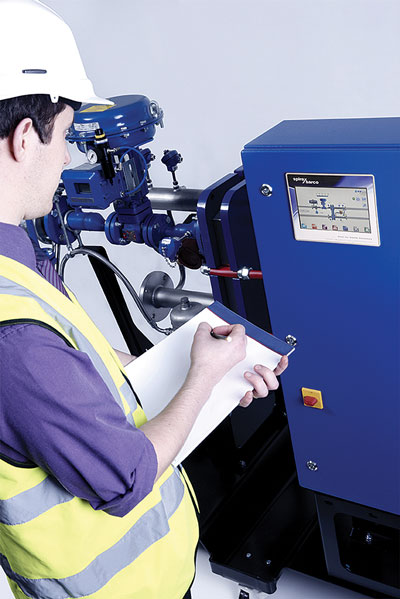
Good quality, dry steam is needed at the heat exchanger to maximise efficiency and minimise steam consumption. Wet steam contains a proportion of water, and hence effective steam trapping of the mains is important in achieving good quality steam.
Non-condensable gases should be removed from the distribution system, as they create a barrier to heat transfer. This is achieved by the use of air vents fitted at strategic points in the pipe system.
Gases can also be minimised through good practice in the boilerhouse. This means using the correct water treatment, and by keeping the boiler feedwater temperature high to allow dissolved oxygen to be driven out of solution before it reaches the boiler – typically at least 85°C in an atmospheric hotwell. Pressurised de-aeration is the best way to deoxygenate the feedwater, as it allows the water to reach temperatures above 100°C, driving non-condensable gases out of solution.
This is why the bigger picture is important. Taking action in the boilerhouse and in the distribution system directly influences the quality of the steam and hence the effectiveness of the heat exchangers in the plant rooms which are being used to generate hot water.
By avoiding reliance on storing hot water and by employing good practice across the site, users in manufacturing plants and the healthcare industry can improve energy efficiency, reduce the risk of legionella and provide reliable, consistent hot water to processes and people alike.
Further information: sxscom.uk/HeatExchangers