There’s no reason why pump maintenance should be too complicated for clients’ own teams to undertake, says David Brown, managing director of Borger UK
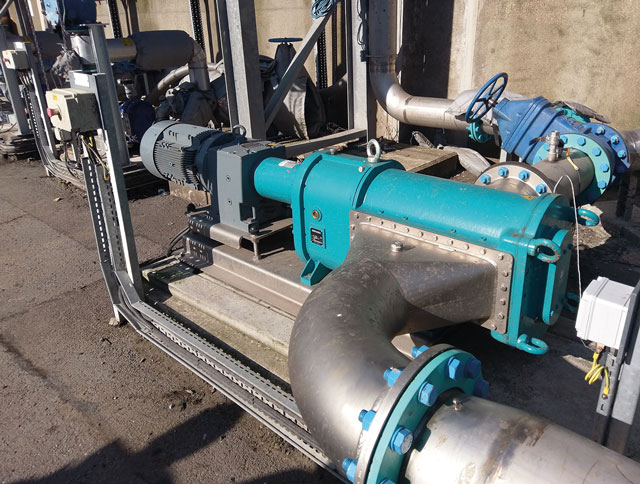
Remember those days when you could look under the bonnet of a car, and – with a bit of knowledge – solve a problem? Now, everything in the engine compartment is all very sophisticated – with no end of parts partnered with high-tech components – so that you can’t work on it yourself.
In industry, with the rise of automation, fewer employees are needed, and improved connectivity has enabled more employees to work remotely. Site staff and maintenance personnel increasingly work, and attend breakdowns and other incidents, alone, often at remote locations. The COVID-19 outbreak has only made these challenges more apparent.
So I think pumps should be like cars used to be – that you need some skills for servicing, but that there shouldn’t be unnecessary obstacles.
The business model of service contracts is a wise one. For the manufacturer they bring in regular steady income. So you’d be forgiven for thinking that our company, Borger, is missing a trick. Borger has and wants service contracts, but working closely with our partners and our customers, we welcome the fact that many of our clients carry out their own maintenance.
Borger pumps recently replaced some units for an important application at a treatment works where the correct mixing of waste sludge pays significant dividends with biogas yields. A big selling point was that the new pumps were “maintenance in place”, requiring no special tools. Before, even though the maintenance team at the plant were extremely capable, when work was required the pump manufacturer had to visit the site with its own specialist jig. Frustrated, the water company asked if it could buy a jig, but was told that it wasn’t available.
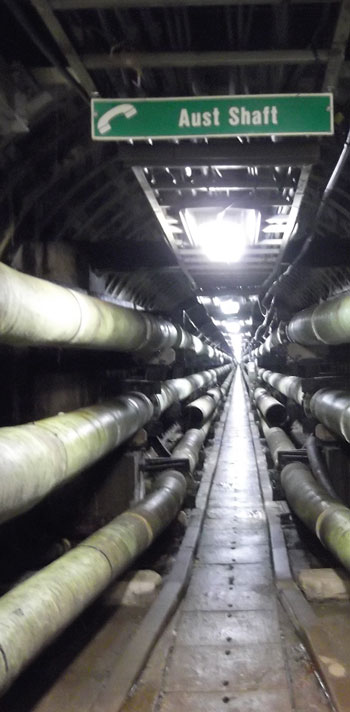
This is a common example of simple, preventive maintenance being made unnecessarily complicated – which also means that it is time-consuming, not good for the process, and invariably expensive.
When Borger receives enquiries asking what special commissioning tools are required for our pumps, the reply is “none”. Since 1975, the company philosophy on making pumps has been quite simple: problem-free continuous operation because working hours are precious; downtime is bad time.
In a tunnel 70m below the Severn Bridge, a crucial pumping operation protects National Grid power lines supplying local housing and industry from inundation, removing a million litres of water from underground springs daily.
Servicing used to be a major event, requiring a minimum of three personnel to go down into the tunnel to carry out an inspection that could take at least two and half hours. To bring one of the pumps out for repair or maintenance required winches, in an extremely time-consuming health and safety event lasting up to two and half days.
There was the cost of bringing in two fitters and jacking up the screw pump in order to cut the main rotor in half. Though systems are firmly in place to prevent homes and industry from any power outages, the knock-on effect from a total pump failure would cost around £1m to £1.25m per day.
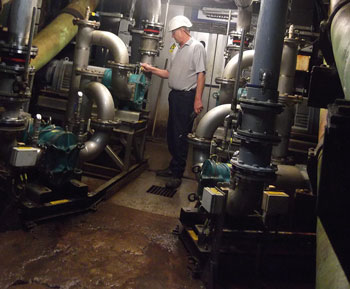
Now the two old units have been replaced by four Borger pumps, and inspection time is less than 45 minutes. For servicing, the maintenance team can take a small holdall of basic tools down in the lift to service the pumps in situ. The maintenance-in-place feature means that all four can be stripped down, oil changed, and rotors checked, in a day (or less), right back to the gearbox seals. The savings on labour are huge.
The business model for spare parts can also be extremely lucrative for manufacturers. But why pay so much, especially on top of all that downtime? Users are becoming increasingly unhappy with paying anything from £600 to £2,000 for a new pump seal. Some Borger seals cost less than £100 – and I hasten to add that’s not because they are “cheap”.
As it always does, technology keeps moving at a fast pace. Some of the innovations that come to industry are incredible – but, as we all know, things can also be very over-engineered. For numerous pump applications, there’s simply no need.
01902 798 977 | www.boerger.com | uk@boerger.com