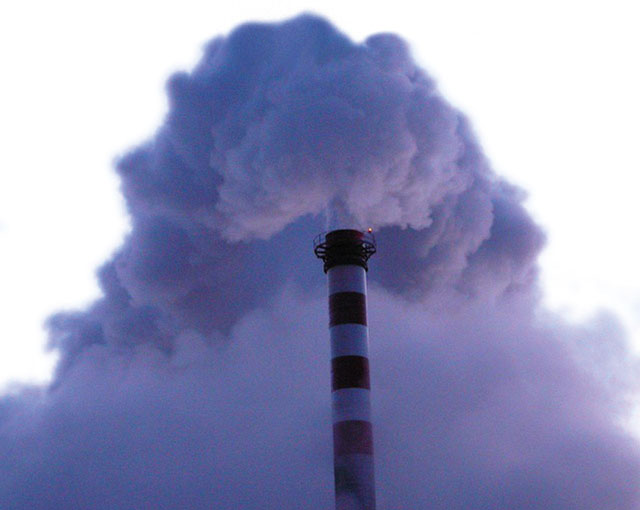
The Environment Agency published an updated version of the Operator Monitoring Assessment scheme in April. Below Andy Tiffen, project manager for air and emissions at SOCOTEC, summarises key updates relevant to an OMA audit.
What is an Operator Monitoring Assessment?
OMA audits are carried out by the EA on industrial installations regulated under the Environmental Permitting Regulations. They are carried out to assess the monitoring of emissions to air and discharges to controlled water (including public sewers and groundwater). The OMA scheme is used to:
- Assess the quality and reliability of operators’ self-monitoring, as required by their permit
- Identify monitoring shortfalls and potential areas for improvements
- Review the monitoring conditions in the permit.
The audit aims to make sure the operators’ self-monitoring techniques are suitable and provide accurate data. This in turn ascertains there is no environmental risk or damage caused via emissions and discharges.
After an audit, a report is produced and a copy provided to the operator. Any areas of concern are followed up by the EA, either individually or as a repeat targeted OMA. A full OMA should be carried out within one year from a permit being issued or a plant commencing operation. It should then be repeated every four years, with the frequency increased using a risk-based approach.
What is the purpose of the updated OMA guidance?
The aim of the update is to make sure that assessments of operators’ self-monitoring arrangements are made in an objective and consistent manner. Though predominantly for the use of the EA, it can also be made available to operators who wish to carry out internal audits on their behalf.
What are the key changes?
One of the key changes is the removal of “critical elements”. Critical elements used to receive specific focus from the EA, with low scores in these areas likely to result in corrective actions. The new scheme now includes a “scope” description in each section to define more clearly what it applies to. For example, calibration of equipment may apply to in-house equipment, external laboratories or the accredited stack emissions monitoring contractor.
In addition, there are a number of section-specific changes:
- 1A – Now requires a specific documented review of the Site Specific Protocol (SSP) before any stack emissions testing is carried out
- 1C – There should be documented reasons if scheduled monitoring is delayed
- 1D – The operator will receive a low score if monitoring results are only assessed against the Emissions Limit Value (ELV). Results should be used to assess trends or process conditions in addition to simply meeting the permitted ELV
- 1E – The site should have an understanding of how the process affects the environment and this should be supported by an H1 assessment. Additional points are available if an operator has a carbon neutral policy.
In the section 2 summary, the use of surrogate calibration methods has been removed.
- 2A – Evidence of an EN15259 assessment is required where such an assessment is applicable
- 2B – If non-certified equipment is used, this requires written approval from the EA
- 2C – A line has been removed from this section relating to the need to identify significant interference from other species or sensitivity to any process parameters. A requirement for the operator to assess Limits of Detection has been added
- 2D – In this section and many following, additional points are likely to be gained if calibrations are done to UKAS/MCERTS specifications. In addition, calibration concentrations should be relevant to the site ELV.
- 3B – A site procedure should exist to ensure new equipment is MCERTS certified
- 3C – Additional points are available for sites not falling under Waste Incineration (WI) or Large Combustion Plant (LCP) if they comply with the requirements of BS EN 14181
- 3F – For WI and LCP sites, if more than 10 days of monitoring data annually is invalid, this must have been reported to the EA along with a corrective action plan
- 3H – Specific guidance has been added on requirements for the traceability of test materials
- 4A – Any sub-contract monitoring organisation’s performance in Performance Testing schemes should be known
- 4B – Continuous Emissions Monitoring System reporting software must now meet MCERTS. In addition, the operator should be able to show how reported data is calculated from raw data and must have measures to cover data security and archiving.
The Environment Agency has internal guidance for inspectors on how to apply OMA, and although this guidance is not published, it can be requested from your local EA inspector.
SOCOTEC provides OMA audit assistance and offers a number of OMA-related training courses for operators, including OMA preparation courses, operator permit awareness, BS EN 14181 requirements and MCERTS revision.
For further information visit www.socotec.co.uk/services/energy-supply-generation-and-regulation/stack-emissions-monitoring-and-testing/ or contact the emissions team at www.socotec.co.uk/contact-us