Sensor to cloud integration – a direct connection from the production line to IT systems on the operational level – has become a key objective of many businesses as they expand their digitisation strategy. The Perinet system is designed to make this simpler, explains Björn Engelbert, who leads the company’s strategic business development.
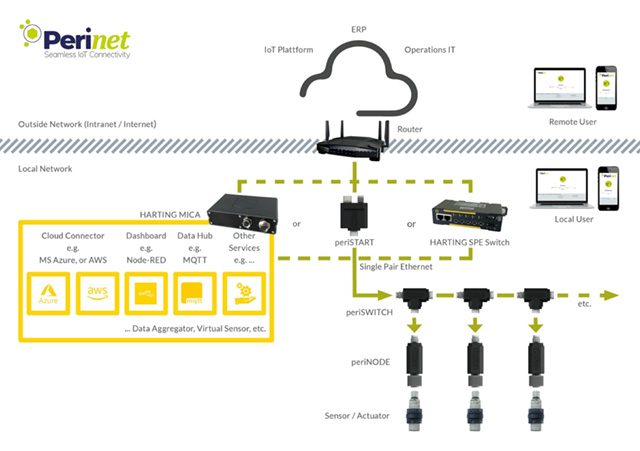
The aim of achieving sensor to cloud connectivity is rooted in the aim of process optimisation. It makes real-time data on the performance of equipment on the production line readily visible to anyone, from the shop floor to the purchasing department and throughout the whole organisation.
Perinet, based in Berlin, was founded by former Harting Technology Group chief executive Dietmar Harting and is led by the former head of development of the award-winning MICA Edge Computer, Dr. Karsten Walther. It is focused on the seamless connectivity of sensors and actuators with any given IoT data hub, with the aim of facilitating easy and economical implementation at the operational level, condition monitoring and predictive maintenance being the most prominent use cases.
Since October 2018, the company has worked on the development of a core module and a series of hardware components and embedded software that extend the internet of things by transforming passive sensors and actuators into smart, native network participants.
In other words, it allows those devices to be connected to the network as easily as a PC, and directly addressed without the necessity of additional protocol conversion.
There are two key components in Perinet’s Seamless IoT Connectivity system. A smart adapter, periNODE, can be retrofitted to existing analogue sensors and actuators. As well as providing an Ethernet interface, it adds intelligence to the sensor, so that it can perform pre-calculations and send information rather than raw data. The sensor can be communicated with via the internet using any device with a browser. A core module, periCORE, has the same functionality and is targeted at manufacturers of sensors and actuators to be designed into their products.
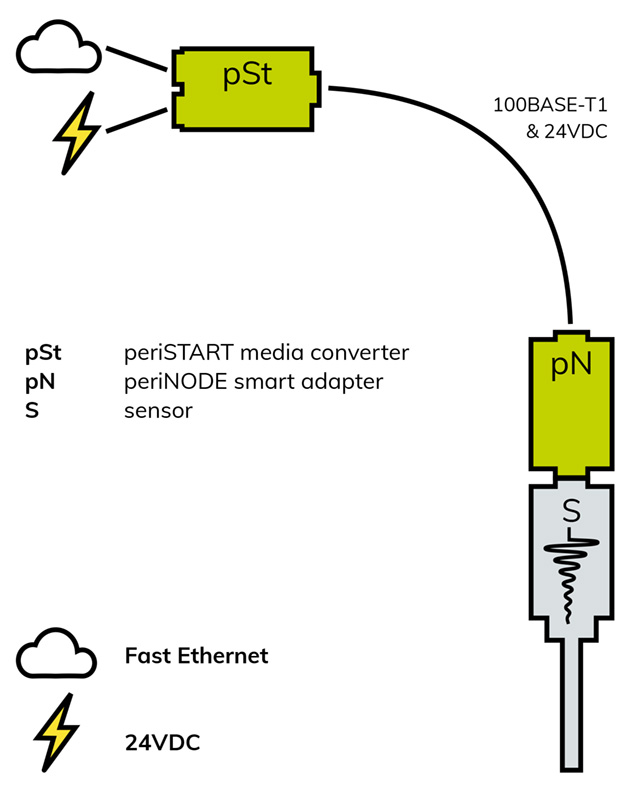
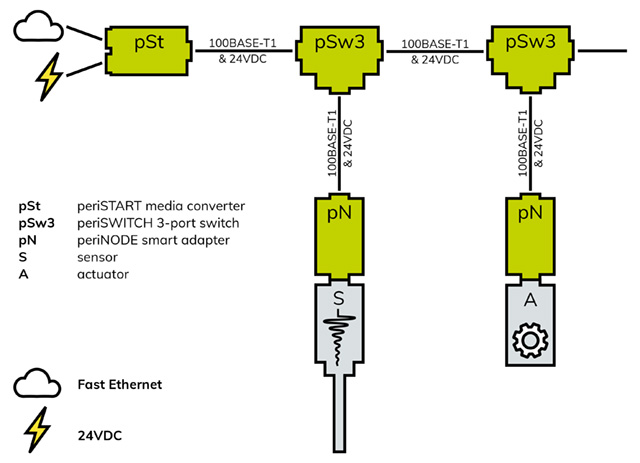
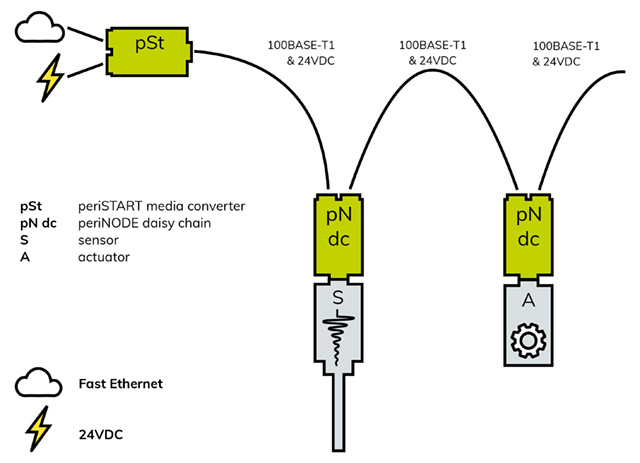
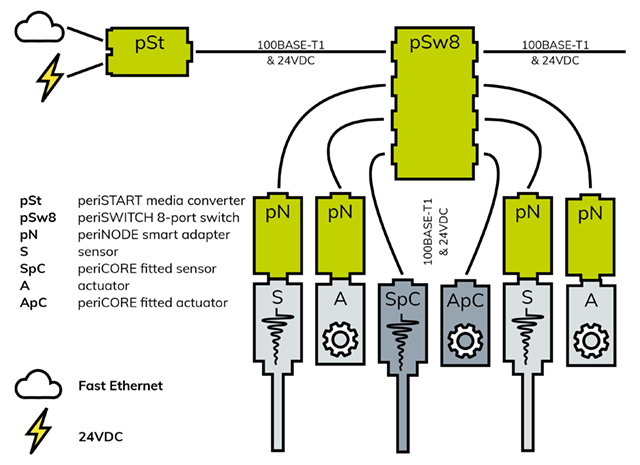
Classic IIoT uses such as condition monitoring and predictive maintenance are often a first step companies take when approaching their digitisation strategy. Though sensors to provide data on current status are already a staple in automation, these are usually connected to a PLC, to provide feedback used to control the machinery.
Perinet, by contrast, bypasses the PLC altogether and provides field-level data directly to operational IT systems. The data can then be used directly to trigger appropriate action (such as generating an automatic alert if a given threshold value is reached). The periNODE smart adapter converts sensor signals directly into a specific value including the physical unit (such as °C) and allows the data to be viewed directly via a browser-based dashboard.
The proprietary set of components is designed to easily connect field-level devices directly to the existing infrastructure, that is an Ethernet network port and a standard power outlet. Only two components – the smart adapter and a media converter called periSTART – and a cable are needed to connect a sensor or actuator on the shop floor to the cloud. For point-to-multi-point setups, a 3-port switch as well as an 8-port switch facilitate various network configurations (line, star, daisy chain) to adapt to any particular setting or environment.
Once deployed, the Perinet system transmits data to any given IT system or data hub, both at the plant or in the cloud, that may be used for further processing and analysis.
Perinet components allow for the integration of different sensors and actuators, independent of signal type or manufacturer. This ensures system compatibility, as only minor adjustments to the hardware and software are necessary to expand the portfolio.
The system is designed to be employed in both greenfield and brownfield environments, in the latter allowing for the integration of older, analogue machinery in digitisation strategies and prolonging their lifespan.
Other key features of the Seamless IoT Connectivity system are automatic device identification in the network, a browser-based interface that works both as a dashboard to immediately view sensor data as well as for advanced configuration setting, and end-to-end signal encryption for full data security.
Planning, deployment and operation are significantly simplified, and the time and effort required for installation and setup is greatly reduced when compared with sensor systems addressed via a PLC, resulting in a lower cost of ownership.
Operational IIoT use cases
For communication with a plant-based or cloud-based data hub, Perinet enables the user to configure whether data is to be communicated continuously, at defined intervals or as a result of events, such as the passing of a threshold. This allows data rates to be controlled as required, rather than creating a redundant and costly data lake.
Condition monitoring uses in Industry 4.0, for example on the current status of an industrial connector, or automatic identification during the tooling process for example in injection moulding, can be covered by use of Perinet’s core module.
Hybrid Single Pair Ethernet
Connection by Hybrid Single Pair Ethernet allows additional configurations to be achieved, such as daisy chaining (see box). Smaller components available for the hybrid variant allow for further reduction in size.
Currently, SPE following the IEC 63171-6 standard defines 100 Mbit/s transmission for cable length of up to 15m. Perinet is currently working on a solution to significantly expand the cable lengths supported in the SPE standard in order to enable the digitalisation of the process industry with the Seamless IoT Connectivity System.
e: welcome@perinet.io | www.perinet.io
t: +49 30 86 32 06 700
Single Pair Ethernet
Single Pair Ethernet (SPE), originating from the automotive industry, is now available for the industrial field level. It describes a technology that combines both data communication and power supply over one pair of copper wires, which significantly simplifies the cabling effort during installation.
When connected via SPE, devices at the field level, such as sensors or actuators, receive their power feed via power over data line (PoDL) while communicating via BASE-T1 Ethernet at various transmission speeds.
Perinet uses hybrid Single Pair Ethernet (SPE) for data transmission, where instead of power over dataline two additional wires supply attached devices with 24V DC. This makes possible configurations that are not possible with “classic” SPE, such as daisy chaining.
Previously, Fast Ethernet (100Mb/s) alone required two pairs of wires, Gigabit Ethernet four pairs. The reduction in cabling made possible by SPE facilitates easy and economical deployment of field-level devices by means of a slim and lightweight yet powerful infrastructure for seamless sensor to cloud integration.
Hence Single Pair Ethernet forms the basis for straightforward digitisation and sought-after IoT uses, such as condition monitoring and predictive maintenance.
For further information on Single Pair Ethernet and the IEC 63171-6 standard, see www.single-pair-ethernet.com