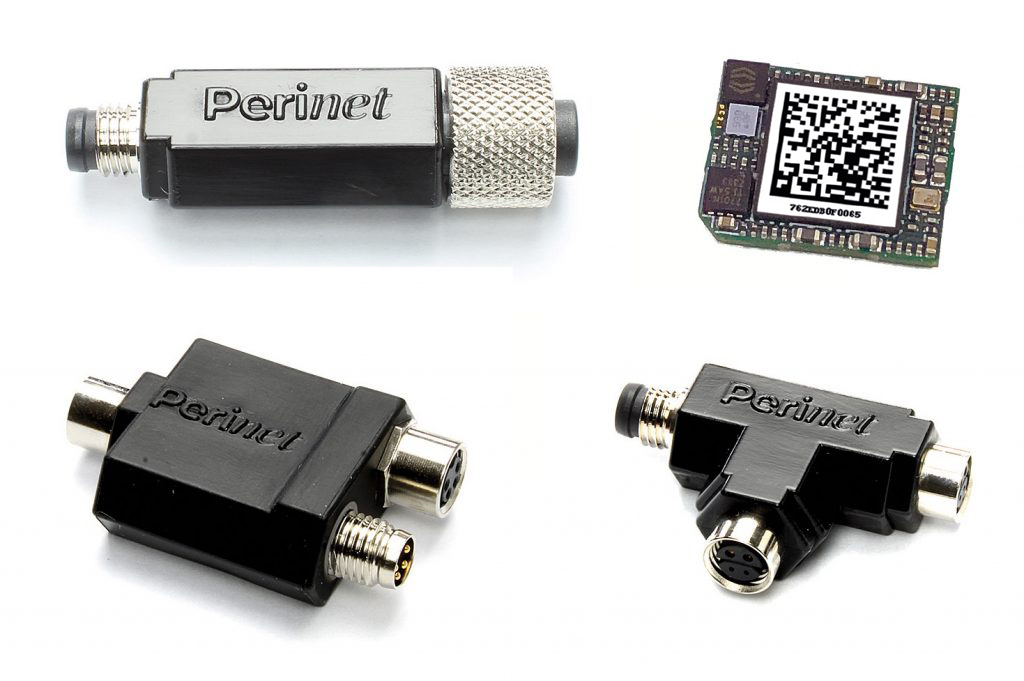
A seamless connection from equipment on the shop floor to the company’s IT system and all the way to the cloud is the ultimate ambition of many companies’ digitisation strategies.
The idea is that this can help to improve efficiency by making data collected from the production process, along with information gleaned from analysing it, readily accessible to anyone in the organisation.
So maintenance staff would be able to conduct predictive maintenance and anticipate when machines and components were nearing the end of their life. But equally, for example, purchasing staff would be able to look at the data to see how long equipment lasted and predict much more accurately when machines would need replacing. Data amassed in the cloud would be analysed to reveal longer term trends.
In this issue we feature an article about Perinet, a company set up by a former chief executive of connectivity specialist Harting Technology Group specifically to address this. It has developed a few simple but effective components to make setting up such connections much easier.
Key to this is a smart adapter, which can be retrofitted to existing sensors. It then allows direct connection of the sensor to an Ethernet network, allowing its status to be displayed on any device with a browser. At the same time it adds “intelligence” to the sensor. So instead of continuously transmitting, say, a temperature reading, the sensor can be programmed to do this only at fixed intervals, or when a predetermined limit or threshold is passed.
In this way the sensor starts to provide information rather than just data, and the accumulation of vast and expensive quantities of data, which may never be properly analysed, can be avoided.
You can start with just one sensor, and scale up as necessary.
It’s perhaps surprising that the company has chosen to go for a wired rather than wireless connection, but it argues that the use of compact Single-Pair Ethernet connectors allow connections to made easily even in confined spaces. A wired connector, which also supplies power, doesn’t need configuration as 5G or Wi-Fi would, and avoids the problem of interference with wireless data that can be encountered in a factory environment.
Elsewhere in this issue, SKF predicts that the day when machine learning algorithms will be routinely used to spot patterns in a vast array of interrelated data is not far away, and that this will allow, for example, much more accurate prediction of the remaining useful life of a machine or component. SKF is working both on the algorithms and also on what combinations of data will allow the algorithms to do their job most effectively.
Together these two developments provide yet more evidence of the powerful tools that are becoming available through digitisation and the internet of things, and which are transforming maintenance into much more of an exact science.
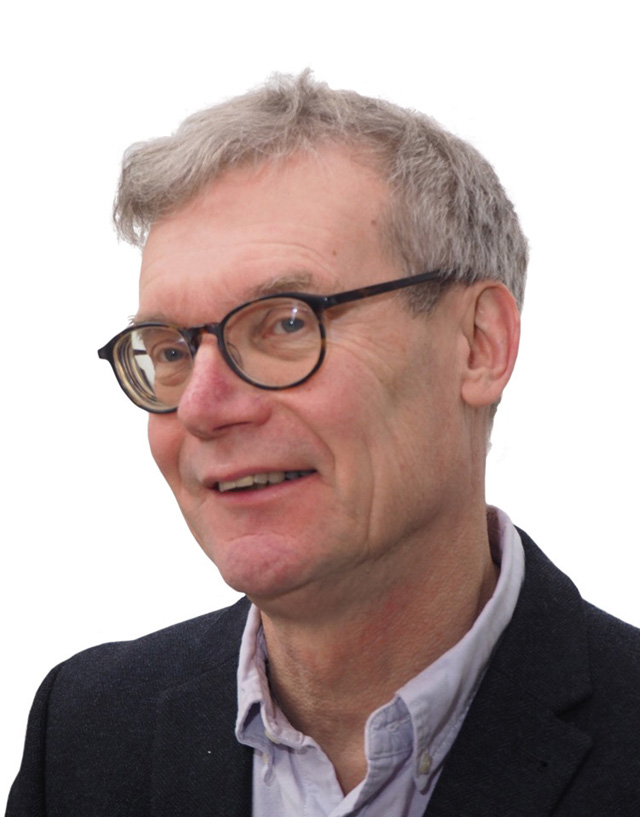
David Fowler MIStructE, Editor
david@maintenanceandengineering.com
@MaintOnLine