A proven solution for monitoring loads in platform mooring connectors will help developers in the emerging floating offshore windfarm sector to increase safety and optimise designs, says Strainstall renewables business development manager Michael Hook
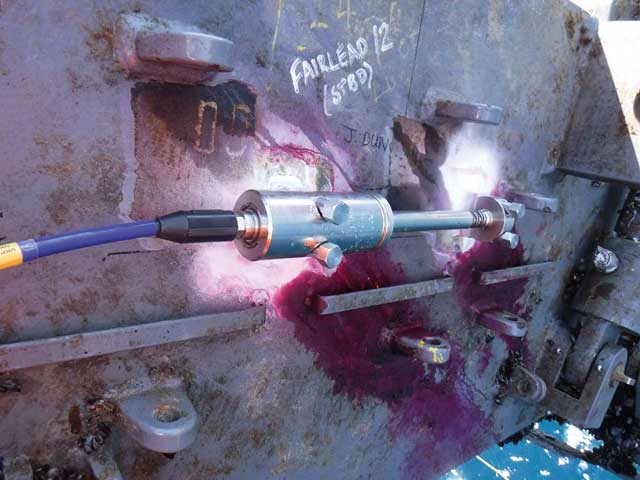
Located 15km off Aberdeen, the world’s largest floating offshore wind farm (FLOW) started generating renewable power in September 2018 with the installation of its first 2MW turbine. Costing an estimated £500m, the wind farm is set to generate enough power for 56,000 homes. As part of the project’s next developmental phase, platform mooring connectors (PMCs) installed by contractor First Subsea will be equipped with Strainstall’s Strain Ring load monitoring solution to provide highly accurate real-time data for one of the wind farm’s platforms.
Challenges for the sector
Though the FLOW industry still has some way to go to achieve parity with the levellised cost of energy (the average cost over the plant’s life per MWh of electricity generated) of its fixed counterpart, floating turbines promise to unlock areas for wind development in waters too deep for regular monopile or jacket foundations. This is against the backdrop of a global scale-up “Catch-22”, in which developers continue to argue the need for a larger “pipeline” of orders to reduce the technology’s costs, while governments call for proven cost declines before allocating funds.
In the UK market, this cycle is beginning to give way to a more streamlined path to commercialisation, as illustrated by the government proposal earlier this year that FLOW may be included as a distinct technology in the next Contracts for Difference round.
The UK has advantages both in its successful deployment history and native supply chain competence – which are widely recognised by the hydrocarbon sector. This framework provides floating wind developers with proven solutions that can overcome the challenges of commercialising in a viable and sustainable way.
Challenges for the project
When operating floating offshore wind turbines, it is essential to understand the stability and performance of the floating platform. The ability to obtain mooring loads and validate those against theoretical models provides a robust foundation for full-scale commercialisation, securing FLOW projects against threats such as mooring line failure.
First Subsea’s key challenge was to retrofit a monitoring solution that could provide the platform operator with accurate and reliable mooring load information without significantly changing the existing design of the PMCs. The company also preferred not to use direct load measurement devices in a subsea environment for the PMCs, favouring an indirect load measurement solution.
First Subsea chose the indirect load monitoring functionality of Strainstall’s Strain Rings as they capture strain information from the bodies of the PMCs, which can then be resolved to derive the mooring loads, without the strain rings themselves having to form part of the primary load path. Integrating simply into the design of the PMCs with only minimal modifications, the Strain Rings proved to be a cost-effective, turnkey solution.
Strain information is transmitted wirelessly from the Strain Rings. It can be monitored on any device, either using Strainstall’s own software to produce a bespoke data dashboard, or integrated into the customer’s existing monitoring set-up.
Strainstall’s Strain Rings were selected in the light of their successful implementation for major projects worldwide. Deployed in the exploration and production sector for nearly two decades, the technology has been installed on both new build and retrofit projects to obtain mooring load data for floating assets, including FPSOs and semi-submersible platforms. With an accuracy of 0.25% of full scale, the technology provides the quality of data necessary for FLOW project stakeholders to benefit from asset lifecycle forecasting, material reduction and value engineering operations, providing long-term improvements for platform safety and cost-efficiency.
To meet the project’s unique requirements, Strainstall also collaborated with First Subsea to design a custom-made dynamic cable that has the ability to accommodate various orientations during different operational conditions.
As a result of its long design life – which exceeds 20 years – the unit can remain in situ for the duration of a typical FLOW project – even in the most challenging offshore environments – meaning that the additional costs of replacement can be avoided.
The solution is suitable for installation in a range of structural applications, from FLOW platforms to wave energy converters.
www.strainstall.com/load-monitoring-products/load-cells/strain-rings/