Schaeffler’s new condition monitoring solution, OPTIME, offers a unique set of benefits over alternative CM systems. In the simplest terms you can Plug > Play > Predict .
What does this mean? The installation is straightforward and does not require any specialist expertise and the machine diagnostics are displayed instantly, showing the maintenance engineers where they are required.
Automated data analysis at an expert level, very low installation outlay and rapid initial operation allows the implementation of CM for large numbers of machines, whose condition could not be monitored cost-effectively until now.
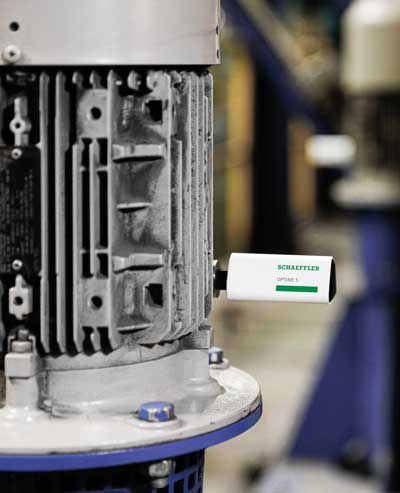
This means machine operators, process plants and entire manufacturing sites can benefit from the use of OPTIME, as well as professional condition monitoring service providers and power transmission specialists who wish to expand their portfolio through additional CM solutions.
OPTIME is an easily scalable system that consists of a mesh network of wireless, battery-powered vibration sensors, a gateway with SIM card, data analysis in the cloud, and an app for mobile and desktop devices to visualise the condition of all assets. A key benefit of OPTIME is that maintenance managers can install the system themselves and monitor their machines at expert level without assistance.
The data captured by the sensors is analysed using specially developed algorithms that draw on Schaeffler’s technical expertise, its extensive library of physical models developed and refi ned over many decades, and the company’s vast experience in the condition monitoring of rolling bearings.
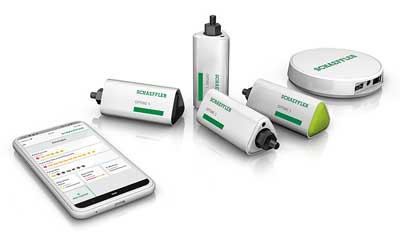
OPTIME provides several weeks’ early warning of rolling bearing damage to machine components such as motors, fans and pumps and also provides early warning of imbalances, misalignments, cavitation in pumps, gearbox damage and lubrication issues. The app presents trends in graph form and visualises the severity of incidents using traffic light colours and alarm states. Maintenance teams receive specific recommendations on the remedial steps required, so they can easily plan their maintenance work, manpower needs and spare parts procurement.
Minimum outlay, maximum benefit
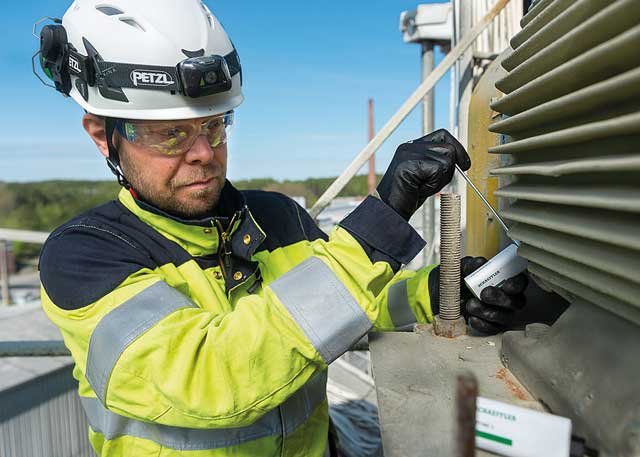
install the OPTIME solution.
OPTIME can be installed and initial operation carried out without any prior CM expertise, and several hundred measurement points can easily be set up in a single day. The vibration sensors are screwed directly on to the asset or by using a mounting plate secured using adhesive, and are activated by the accompanying app, which connects to them via near-field communication.
All installed sensors communicate autonomously with each other and the gateway, thereby forming a dedicated mesh network. The sensors transmit machine KPI data as well as raw vibration and temperature data via the gateway to the Schaeffler IoT Hub. The hub analyses the data, and the results are displayed in the app, which supports a wide range of end devices commonly used by maintenance teams and plant operators. Alternatively, results can be made available for integration into the customer’s own IT environment via a REST API.
Significant cost savings
One of the first customers to use the Schaeffler OPTIME solution is Finnish cement company Finnsementti, which produces cement, lime and other raw materials at its Parainen and Lappeenranta plants.
The company‘s primary concern is plant downtime. Around 90 machine failures occur on average each year, the majority of which are caused by auxiliary units. In such cases, production is suspended completely for one to two hours. The most critical units are motors, gearboxes, pumps and fans. Finnsementti were also looking for a solution that would provide greater security for personnel. As auxiliary units are generally difficult to access, accidents are inevitable.
Finnsementti had not previously installed condition monitoring for the purpose of monitoring auxiliary units, as this was too expensive and, for the most part, did not work wirelessly. OPTIME allows Finnsementti to monitor practically every rotating machine at the plant on an automated, permanent basis.
The installation work, which involved fitting around 150 sensors to motors, fans, pumps and gearboxes, as well as mounting the gateway, was completed in just a few hours. The mobile app allowed hundreds of machines to be monitored directly.
Tony Virtanen, a maintenance engineer at Finnsementti
comments: “With OPTIME, our maintenance staff have the
transparency over the condition of most of our machines without
the need to watch them closely all the time.”