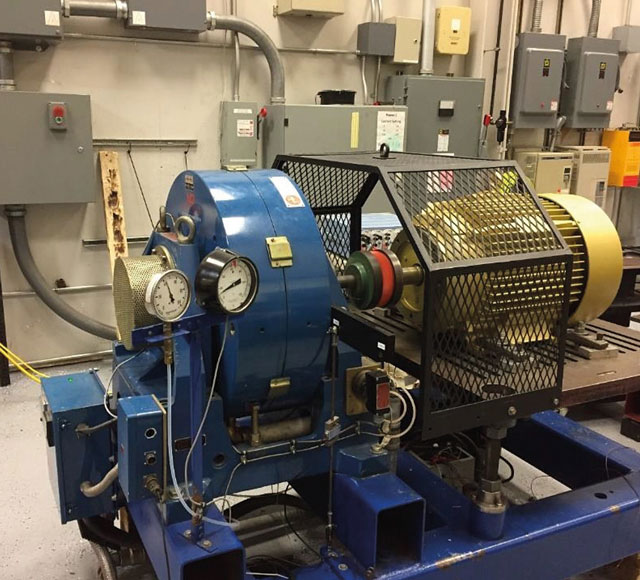
Tighter energy efficiency regulations have led to a significant increase in the use of premium efficiency (IE3) motors, and as a result the question of maintaining efficiency after a rewind has reappeared. A new study finds rewinds completed using good practice retain the original efficiency rating, says AEMT secretary Thomas Marks.
It is well established that electric motors account for 65% of the energy used in industrial applications. Slightly less well known is the fact that approximately 96% of the lifetime costs of an electric motor are associated with energy consumption. With this in mind, it is important that any repairs to premium efficiency motors retain their original specifications.
To establish the effect of rewinding a motor on its efficiency rating, a comprehensive study was carried out in 2003 by the Association of Electrical and Mechanical Trades (AEMT) and EASA in the US. It involved 23 larger IE2 motors, which would be considered most likely to be rewound, compared with smaller models that would be more economic to replace. The study spent considerable time establishing the procedures for the repairs and the facilities that would be used to test the motors.
In 2019, they study group was reconvened to answer the same question, but this time in relation to premium efficiency IE3 motors. In this case, ten new IE3 motors with power ratings ranging from 30 kW to 75 kW, half being IEC and half NEMA designs, were evaluated. These had similar characteristics to the motors used in the 2003 tests, to enable meaningful comparisons to be made:
• Totally enclosed fan-cooled IP54 enclosures
• 50 Hz and 60 Hz designs
• 2-pole and 4-pole motors
The first step was to establish a benchmark efficiency figure for each motor, rather than taking the data provided by the various manufacturers. All the testing was performed at North Carolina Advanced Energy Corporation (Advanced Energy) located in Raleigh, North Carolina, using an eddy current dynamometer test stand. Currently, Advanced Energy is the only independent motor lab in North America to hold the National Voluntary Laboratory Accreditation Program (NVLAP) accreditation for motor efficiency testing.
Harmonised standards
The procedures for removing and replacing the stator windings had been established for the 2003 study. These repair procedures were published in the Good Practice Guide to Maintain Motor Efficiency, which has been incorporated into the latest international repair standard IEC 60034:23:2019, and the latest American Ansi/EASA standard AR100. As with the previous study, the IEEE 112B test standard was used – this also complies with the harmonised international test standard IEC 60034-2-1.
The results from the ten motors showed that there was no significant change in the efficiency of the motors following a rewind using good practice repair procedures. This mirrors the results from 2003. The average change in efficiency over the entire group of motors was a decrease of just 0.1%, which is within the tolerance that would be expected in this study.
The near-identical results between the 2003 and 2019 studies is attributed to the method of removal of the original windings and the process of replacing them with new parts. The stator loss was maintained by copy rewinding. In some cases, the wire volume was increased because all the new coils were inserted by hand, whereas the original windings were machine wound.
The 2019 study has reaffirmed the findings from 2003 and endorsed the findings that rewinding IE3 motors using methods outlined in IEC 60034-23 and the Good Practice Guide will retain the original motor efficiency.
+44 (0) 1904 674895
admin@aemt.co.uk
www.theaemt.com