Gas turbines are efficient and flexible sources of power that drive generators in power stations and industrial settings. Their reliability can be assured by an effective maintenance programme, says Campbell Archibald, sales director of Sulzer brand Alba Power.
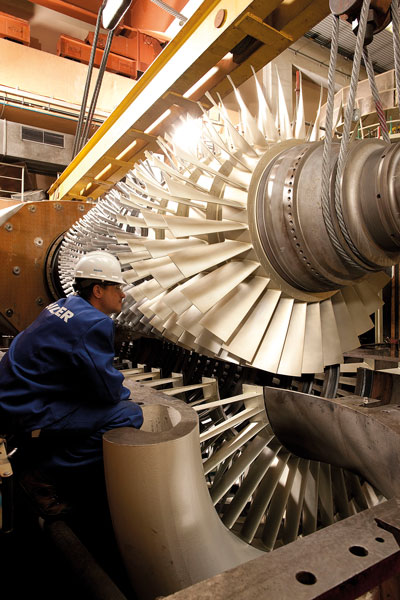
overhaul projects are completed on time
The popularity of gas turbines around the world as a source of mechanical power emphasises the efficiency and reliability that can be achieved. The range of designs, from aero-derivatives to large-scale power generation units, means that a wide range of applications can be accommodated. Their flexibility allows for frequent start/stop operations, but this makes planned inspection and maintenance all the more important.
Higher operating temperatures and mechanical stresses are creating the need for the use of advanced technology in components and refurbishment processes. In general, repair activities consist of the stripping and reapplication of coatings, rebuilding of the geometry of parts such as combustion liners, transition pieces and flow sleeves using advanced welding techniques, and rejuvenation of the material condition through heat treatment. Advanced refurbishment procedures include changes in materials, coatings, or design, which aim to improve performance and lengthen the periods between scheduled maintenance activities.
Assessing serviceability
The basic operating principles of a gas turbine are relatively simple, but the components involved must handle high temperatures and must work within very fine tolerances. Highly specialised parts and manufacturing processes are used to create the components and they need to be properly maintained to provide continued efficiency and reliability.
Regular data collection from sensors throughout the installation provides information on vibration, temperatures, pressures and turbine output. This is collated and assessed to find any anomalies, as part of a serviceability report which identifies any issues that need to be prioritised and addressed.
Condition-based monitoring and recommended maintenance intervals are usually dictated by the original equipment manufacturer. However, these may not suit all applications, especially gas turbines used for peak lopping or as back-up units; these can benefit from remote monitoring and bespoke maintenance packages that take their circumstances into account.
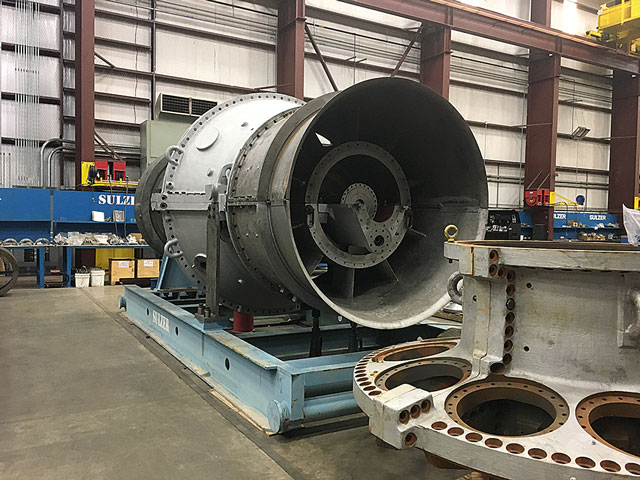
and well-equipped service centres
This approach is complemented by upgrading the sensor package to use items such as sonic microphones in the hot gas path to indicate problems with the combustion process. A tailored package offers the best availability by allowing maintenance and repairs to be completed during scheduled shutdown periods. These also provide the opportunity to install upgrades and improvements.
Thermal inspections
At the heart of the gas turbine, hot gas path components require regular inspections, since close examination of the individual turbine blades can reveal overheating. Obvious defects can be identified by a service engineer using a borescope, but occasionally a more detailed inspection may be required that demands more sophisticated tools.
In electrical equipment and bearings, the use of passive thermographic equipment can identify heat build-up from the thermal radiation being given off by the component under examination. In contrast, active, lock-in thermography uses ultrasonic excitation to introduce energy into an object such as a turbine blade, and measures its response. If the normally homogeneous material is damaged, some of the wave energy is absorbed and heat is generated, which can be detected by the thermal imaging camera.
Applied to gas turbine components, where effective cooling is essential for extended service life, this technology can show at a glance whether cooling holes are blocked or open. As part of an inspection or a repair, the cooling channels in blades and vanes should be checked.
Latest repair technologies
Modern third generation gas turbines use sophisticated designs and advanced components that require new inspection procedures, welding techniques, coating materials and tooling to restore components in the hot gas path to a safe and serviceable condition.
The use of higher turbine inlet temperatures of over 1,300 °C to achieve increased power output has led to the use of single-crystal (SX) materials in turbine blades. Unless the facility being used to maintain the turbine has the capability to repair these blades, they need to be replaced at every major overhaul, after 24,000 operating hours. Sulzer has developed advanced repair techniques that enable SX blades to be refurbished to an as-new condition, offering a substantial saving in maintenance costs.
As a specialist in the maintenance and repair of gas turbine machinery, Sulzer has extensive in-house expertise and manufacturing capabilities. By working with experienced design engineers and field service staff, gas turbine operators can benefit from independent maintenance support delivered within exacting timeframes.