ABB’s Andy Pearson explains how a holistic approach to maintaining drives reduces the risk of sudden failures and provides a way of managing replacements and upgrades.
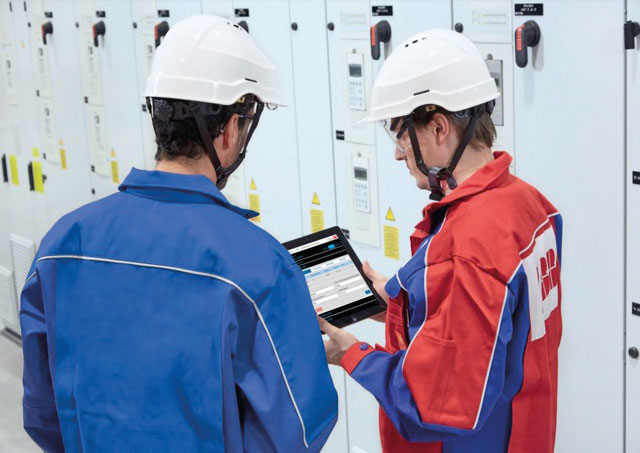
Variable speed drives (VSDs) are extremely reliable and can provide many years of incident-free operation, and a lifespan of several decades. However, their high reliability can sometimes create a false sense of security. If a VSD is operating in good conditions – away from dusty environments, extreme temperatures and hazardous areas – then it can have a mean time between failure of over half a million hours or the equivalent to 62 years.
However, VSDs are not indestructible, and every unit, if left without maintenance, will eventually fail. If the VSD or its components are obsolete it may be very difficult to repair quickly, potentially leading to costly downtime. Having to replace an obsolete drive at short notice is also a headache that operators can do without, particularly if production backlogs are mounting up.
Although VSDs may not be the most expensive items of capital equipment in a plant, they have a high in-service value, and the cost of a failure in lost production can be great. Even so, it is estimated that up to 80% of VSDs in the UK are operated without any kind of systematic maintenance programme in place. This makes it more likely that, if failures occur, they will occur unexpectedly.
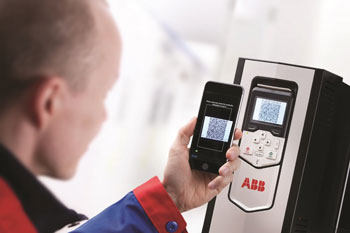
Whole life approach
If a failed VSD cannot be repaired economically then it may be time to replace it. However, this is not a decision that should be taken lightly, and certainly not one to rush. Choosing the right replacement VSD under pressure, amid mounting production backlogs, can result in fl awed decision-making or incorrect installation. It is far better to have a plan in place beforehand that can be activated so that downtime can be kept to a minimum, and the right VSD selected for the right application.
This is best achieved by taking a whole-life approach to the management of both maintenance and upgrades for all VSDs in operation, as well as spares. It considers continuing maintenance requirements as well as obsolescence, replacements and upgrades in the future. This can help to take the element of surprise out of having to replace a drive, and allow potential failures to be anticipated.
Overall total cost of ownership can be reduced by taking a strategic approach to replacement and upgrades, ensuring that VSDs approaching the end of their operational life are appropriately replaced before they risk failure, while embracing new drive technologies and functions as they emerge.
Approaching maintenance strategically
Implementing a comprehensive and continuing review of the status of all VSDs at a given time can be difficult and time-consuming, but services like ABB’s Life Cycle Assessment (LCA) are available to make it easier. VSDs are registered using information collected from the customer’s own management system in an online tool. Alternatively, this can be done through a site visit from an ABB engineer or one of its Value Provider partners, who can make the assessment for you. Once the VSDs are registered, the tool provides a comprehensive overview of the life-cycle state and operating conditions of each drive for better decision-making and maintenance scheduling.
The LCA tool logs age, location, criticality, operating environment, service history and part replacement history. This allows maintenance to be tailored to the needs of each drive, while flagging any drives or components that need particular attention. Critical drives and at-risk assets are identified, providing a comprehensive overview of the entire infrastructure.
The tool also highlights, in a report, those assets which need servicing or are candidates for replacement or upgrade. This helps avoid unplanned downtime and can be used to project maintenance budgets and manage costs. It can also help companies to modernise their operations by providing a schedule for replacing and upgrading equipment that might be approaching obsolescence.
www.abb.co.uk/energy | e: energy@gb.abb.com t: 01925 741300