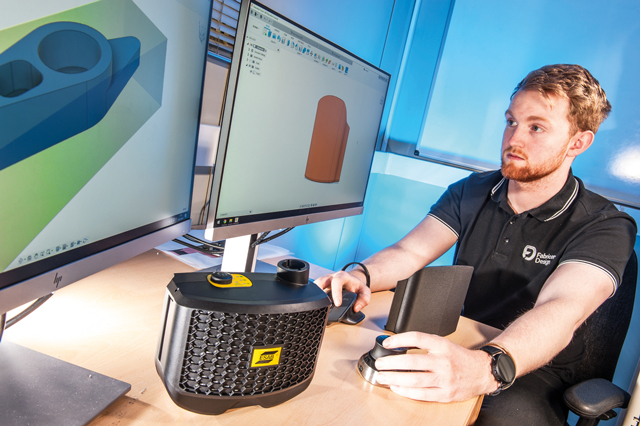
Small and medium manufacturers are rapidly embracing technology and digital tools to recover and grow after a tumultuous year, but the appetite for adoption is highlighting a digital skills gap. Innovative partnerships between industry and academia are needed to develop fast track solutions, says Made Smarter’s specialist organisational and workforce development adviser Ruth Hailwood.
Since its launch two years ago, the Made Smarter North West Adoption programme has engaged with 1,165 small and medium manufacturers to tackle the barriers to industrial digitalisation and show them how digital tools and technologies can make a real difference to their businesses.
Half those committed to investing in new technology have put data and systems integration at the heart of their productivity and growth plans. This has included working with legacy data and connecting up disparate data sources so all the data is visible and usable. This then enables other technologies to be used. For some this has meant the industrial internet of things, installing sensors on equipment, and building further data collection to capture vital information from the shop floor, while others have invested in full factory integration.
Though these projects have solved business challenges, driven growth, and whetted the appetite for further technology adoption, what has also become clear is that SME manufacturers need key skills in data management, integration and visualisation to be able to make effective use of what their data is telling them.
To help businesses fulfil their skills needs, Made Smarter is mapping the skills required to introduce new technologies and finding innovative ways to help bridge those skills gaps.
Our digital technology internship programme has so far connected 46 university students and graduates with SME manufacturers to work on live digital transformation projects. Businesses benefit from the fresh insight of a digital “native” to help them adopt technological tools, while interns benefit from paid work experience, valuable hands-on practical work experience, and a taste of a potential career path. A number have even secured permanent jobs.
The internships have also enabled manufacturers to test the business case for recruiting for data and software roles or identify how to upskill their current workforce.
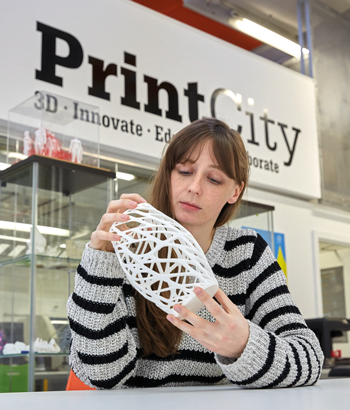
The Made Smarter Review, the independent review of industrial digitalisation in 2017, identified skills shortages as a major barrier to technology adoption. It found that businesses are being hindered by a fragmented skills system and a lack of systematic engagement between education and industry. One of its key recommendations was for relevant and easily digestible training.
The difficulty is that the skills and training landscape is mixed. There are some very basic digital skills offerings, and at the other extreme training that is very technical and specialised.
That is why we worked with Manchester Metropolitan University’s PrintCity, and Fabricon Design, a business using both traditional and advanced manufacturing methods, to jointly create an innovative, high impact programme for additive manufacturing.
The 12-day programme, funded by the Fast Track Digital Workforce Fund, uses flexible, modular training designed to fit around work schedules. It has enabled participating businesses to upskill members of their workforce, giving them the grounding to be able to implement a new technology straight away or to make the most of the technology if they have already invested. The aim is to accelerate productivity improvements in existing operations and potentially develop new products and new markets. The programme has proved industry and academia can collaborate successfully to pioneer fast track solutions to plug skills gaps.
The hope now is that this model can be applied to other skills needs such as data skills for manufacturing and to other technology areas such as IIoT, robotics and automation, AI, and simulation, giving SME owners an understanding of how these technologies can be used as tools to take their business forward, removing the fear of the unknown and equipping manufacturers with the new digital skills that they will need in the future.
That is what Made Smarter is about: demystifying the technology and removing that fear factor.