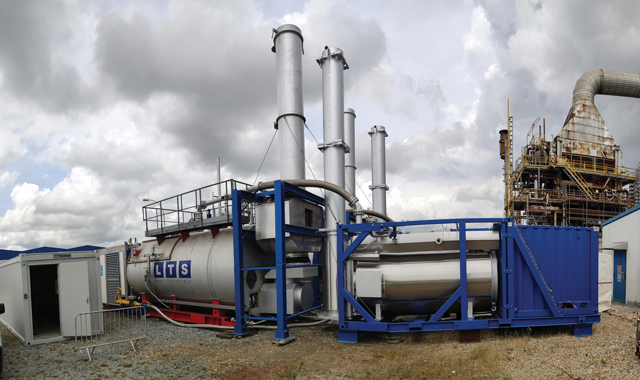
Taking a long-term view of boiler efficiency is an effective way of reducing whole-life costs of steam generation, says Matthew Schofield, UK steam business development manager at Atlas Copco Rental UK.
Often when businesses are considering a new steam installation the emphasis in decision-making is placed on the capital investment. However, this does not take into consideration the longer-term cost implications or overall efficiency of the asset. It is valuable to consider the cost of usership, and not just ownership.
Usership takes into consideration the initial and continuing costs of the equipment, as well as utilisation – this can provide a much more accurate picture of the most cost-effective solution. This is particularly important because typically the expense of fuel over the life of a boiler can be the costliest element.
Whether considering capital investment or a rental solution, making sure you have the most efficient boiler is key to the cost per kg of steam.
Improving boiler efficiency
Typically, industrial steam boilers off er an average efficiency of 85%, so 15% of the energy supplied is lost in radiation, burner purges and exhaust gases via the chimney. By recovering or reducing these losses efficiency can be increased.
Well-established methods to improve boiler efficiency are often overlooked. These principally minimise the cooling losses of the system and recover heat energy. Most commonly used are techniques such as recovering waste heat via an economiser and improving the turndown ratio of the burner – the latter can also be combined with flue gas recirculation.
The role of an economiser
An economiser is a heat exchanger which transfers heat energy from the flue into the boiler feedwater, thereby recovering energy that would normally be lost and putting it back into the system. The energy input to the burner is reduced by approximately 5-6%. Care should be taken not to reduce the flue gas temperature below the dewpoint of water vapour in the fl ue, because the condensed vapour may dissolve acidic gases, increasing the likelihood of corrosion.
The benefits of using an economiser include:
• Saved fuel = fi nancial savings
• Improved effi ciency = less input for the same output
• Reduced environmental impact = less carbon dioxide, nitrogen oxides (NOx) and other products of combustion.
The table below demonstrates typical savings based on Atlas Copco’s largest rental boilers (12,000 & 16,000 kg/hr steam output) coupled with an economiser.
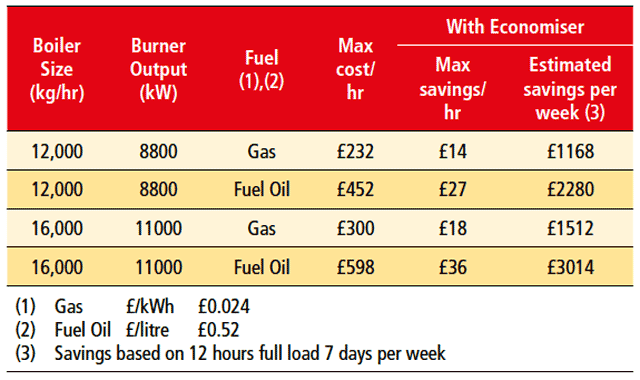
Burner turndown
Turndown is the term used to refer to how much the burner can be regulated before being forced into an off state. Every time the burner starts or stops, air purges entrain cooler air into the system and purge residual fuel, with a negative effect on efficiency.
A modulating burner with a high degree of turndown can reduce the need for stops and starts by regulating output to suit steam demand. This proves extremely useful for production sites with a variable load. It also keeps the burner firing at optimum efficiency to maintain the steam output of the process, adjusting up and down accordingly. Couple this solution with flue gas recirculation and not only do you reduce fuel consumption, but you can also dramatically reduce gaseous emissions.
Atlas Copco Rental UK’s fl eet consists of highly efficient assets to provide the optimum rental solution. Its boilers are capable of 10:1 turn down (plus FGR) and can achieve an efficiency of 90%+ from an agile modular solution.
Further information: 0800 169 6611
www.atlascopcorental.co.uk | rentaluk@atlascopco.com