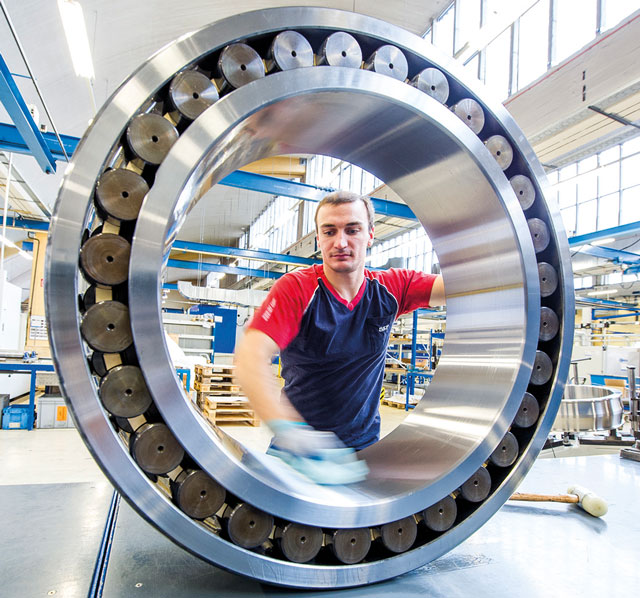
To generate measurable value and improve the performance of rotating equipment using Industry 4.0 technologies, the approach must be tailored to the specific needs of the customer, says SKF.
Advances in technologies for connecting machinery to the internet, for controlling that machinery remotely and for gathering data from it have unlocked the potential for significant improvement in the cost-efficiency, quality and productivity of industrial operations. For rotating equipment, such technologies could be used to maximise the reliability and output of machinery – and the production processes in which it is used – while driving down the total cost of the ownership of the equipment over its life.
Potential
Many companies and their suppliers, however, are struggling to exploit this potential to its fullest. This is because they tend to focus on the theory surrounding Industry 4.0 and the technologies necessary for its widespread introduction, when they should be focusing on the benefits of the approach and the practical challenges associated with its adoption.
To fully harness the benefits of Industry 4.0, the toolbox of technologies involved – such as internet of things enabled devices, big data analysis and machine learning – needs to be used in such a way as to generate real and measurable value. Many suppliers of these technologies choose to focus on the development of an Industry 4.0-based ecosystem, without considering the specific needs of their customers. It is vital that the circumstances of the customer are understood fully, and the practical and specific benefits of adopting Industry 4.0 technologies are explained to them.
Key performance indicators
The first step should be to establish the value that digital technologies can generate for the customer, and this is achieved through the use of key performance indicators (KPIs). Many companies, for example, are looking to increase their output. By using the Industry 4.0 toolbox to gather process data remotely, and to gain a thorough understanding of the customer’s operations and requirements, a programme of predictive maintenance could be drawn up that minimises unplanned downtime, potentially saving the customer significant amounts of money in lost production.
The importance of data
Condition monitoring systems can also be used to collect data on the noise, temperatures and vibrations generated by a piece of machinery. The data can be used to identify, and thereby solve, current problems, and machine learning algorithms could be exploited to predict the emergence of future issues.
Handling such data correctly represents a significant challenge in itself. SKF has collected data from many millions of bearings, but this has to be prepared so that it can be analysed accurately and reproducibily for a wide variety of applications, using machine learning algorithms.
The quality of the data being gathered is a key factor in the success of machine learning technologies. Although only a small proportion of the data collected will be required for the process to be effective, it can be difficult to identify the right information for a given application. Further, data is often held in separate “silos”, and sometimes in different formats, making it difficult to investigate holistically.
High-level analysis
The data gathered through condition monitoring programmes must be analysed properly. Though this can be done on site, it is often more effective to send the information to remote monitoring centres, where it can be examined more or less as it is being collected, meaning any potential inefficiencies in the operation of a piece of machinery can be identified more quickly. Further, it is easier for this data to be made available to other teams – application specialists or lubrication engineers, for instance – allowing a process to be analysed in much greater depth.
Performance-based contracts
Taking a traditional approach, all this might be achieved through the introduction of maintenance contacts and consultancy agreements, but such traditional transactional models are increasingly being replaced by performance-based contracts, such as SKF’s Rotating Equipment Performance (REP) programme. These use a base monthly fee, with a bonus payment added at longer intervals if the customer’s performance indicators are achieved. Through such contracts, any risks are shared, but so are the rewards.
The companies that will benefit most from Industry 4.0 technologies in the coming years will be those that are prepared to enter long-term relationships with their suppliers and customers, and keep their minds open to new ways of working with one another.