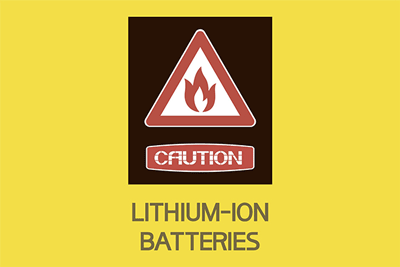
Explosion protection safety solutions provider Pyroban is warning that the use of lithium-ion batteries in fork lift trucks operating in potentially explosive atmospheres might not be safe.
The requirements to assure their safe use in such environments is not clear, says Pyroban, but some manufacturers have placed lithium-ion powered fork lifts into Ex applications, while others do not think the technology is ‘appropriate at this time’.
Using lithium-ion batteries has advantages in the right applications, says Pyroban, but managing director Steve Noakes, convenor of the EN1755 standards committee, says his company will not quote for the ATEX conversion of lithium-ion fork lift trucks.
“We receive a growing number of enquiries for Ex-certified lithium-ion battery options, and for good reason,” Mr Noakes said. “Lithium-ion batteries allow opportunity charging, require less maintenance, and offer longer operation between charges, so have proven to be popular in many industries.
“However, as it stands in June 2021, for the foreseeable future Pyroban declines to quote for the ATEX conversion of lithium-ion forklift trucks.”
Mr Noakes said it is not clear what the right level of safety is for this technology. “As the Ex standards do not appear to cover traction battery applications, one has to question therefore whether they are safe for use in hazardous areas,” he added.
“Pyroban remains active in its technical review of the ever-evolving lithium-ion technology, and in the Ex standardisation work we do to drive clarity in the standards to fork truck applications.
“Although Pyroban has pioneered many new technologies in the past, we do not feel confident to unilaterally decide what is safe for Ex lithium-ion traction batteries. Companies which are currently offering Ex lithium-ion batteries, in our view, do so without a clear foundation even if they have involved a third party, as the recent Safety Alert demonstrated.”
Ex standards for lithium-ion batteries currently applies mainly to small battery packs, not explicitly traction battery capacities. So there is no clear guidance on what battery conditions should be considered for Zone 2 and Zone 1 areas (normal operation, foreseeable faults) and what Ex protection concepts are appropriate.
Mr Noakes said some of the various types of lithium-ion batteries, which use varying chemical compositions, are more volatile than others and there is a balance between power density and inherent stability (safety).
A lithium-ion battery comprises far more components than a conventional traction battery, with individual cells connected to form modules, and each module is connected to form the overall battery package which is overseen by the Battery Management System (BMS). “How each element is designed, produced, and tested is key to achieving the right level of Ex safety,” said Mr Noakes.
He said as cells are produced in very high volumes by factories not always owned by the final battery OEM, a question posed by the EN1755 committee is how the production of this key component can be controlled and verified for Ex applications.
“Which Ex protection concept is appropriate is also a fundamental question which does not have a clear position at the moment as it depends on what conditions are included in the normal operation and foreseeable malfunction requirements.
“Even an Ex d flameproof enclosure may not be suitable for a lithium-ion battery despite its ruggedness.”