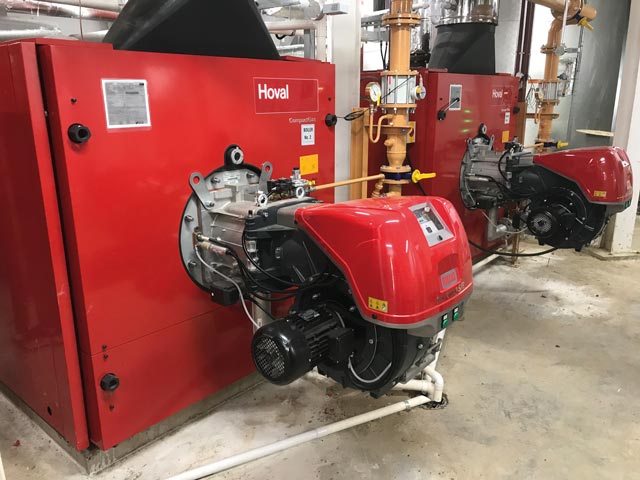
With growing demand to reduce NOx emissions from combustion equipment it’s important for businesses to be aware of the options available. Paul Sharp of Riello discusses two NOx-reducing technologies in industrial and commercial applications
Emissions of nitrogen oxides (NOx) from combustion equipment are becoming an increasingly important consideration from both an environmental and regulatory point of view. In higher capacity applications such as process and manufacturing plants, there are two burner technologies to be aware of – flue gas recirculation (FGR) and premix. Each of these is highly effective in reducing NOx emissions and the choice of technology will be determined by the particular requirements of the project.
NOx formation
To put this into context, it’s worth briefly summarising how combustion results in NOx emissions. During combustion the main components of any fuel – carbon and hydrogen – react with oxygen in the combustion air to form carbon dioxide (CO2) and water (H2O). Other emissions of concern are carbon monoxide (CO) and unburnt hydrocarbons (CxHy), oxides of nitrogen (NOx), oxides of sulphur (SOx).
The NOx emissions are a result of nitrogen in the air combining with oxygen during the combustion process. There are three classes of NOx: fuel NOx, prompt NOx and thermal NOx.
Fuel NOx is related to the nitrogen content of the fuel, which is higher in heavy oils and coal. Prompt NOx is formed in the very early stages of combustion when highly charged unstable oxygen molecules interact with the nitrogen in the combustion air. Thermal NOx results when airborne nitrogen reacts with oxygen, a process that is accelerated at higher temperatures.
Both prompt and thermal NOx emissions are reduced if the flame temperature is reduced.
Two technologies
The main differences between traditional pressure jet burners and premix burners relate to the ways in which the air and gas is mixed and in the technology of the combustion head. In traditional pressure jet burners, the gas and the combustion air are mixed at the point of ignition on the end of the combustion head in the space available in the combustion chamber (resulting in a diffusive flame). This is the most familiar arrangement.
In premix burners the air-fuel mixture is created upstream of the combustion head, which comprises a metallic cylinder that has multiple gas ports on its surface and is covered with a woven wire gauze (known as a “sock”). The air-fuel mixture flows inside the combustion head, through precision-located ports and the sock to the external side of the combustion head, where ignition occurs through spark generation to an electrode and the flame is established.
Flue gas recirculation (FGR)
The use of flue gas recirculation with pressure jet burners is a popular option for reducing NOx emissions. The technology has been available for some years, but uptake in the UK has been slow because of the need for additional controls. As NOx regulations become tighter the use of the FGR becomes more attractive and financially viable.
As noted earlier, NOx formation is exacerbated by high flame temperatures, and the principle of FGR is to reduce peak flame temperature by piping the relatively cool and inert flue gases back into the burner air supply system. The carbon dioxide in the flue gases also helps to inhibit combustion, thereby reducing peak flame temperature even further.
FGR burners need to be used in conjunction with electronic cam control of the combustion air/fuel ratio via separate servomotors, and a further servomotor to control the flow of the recirculated flue gas. The use of FGR with electronic cam control helps to significantly improve energy efficiency as well as reducing NOx emissions.
Riello can supply FGR burners with outputs from 500kW to 32MW, to provide ultra-low NOx emissions, less than 40mg/kWh. This is less than half the threshold required by BS EN 676, Forced draught burners for gaseous fuels, for gas-fired burners to be classified as “low NOx”.
Premix burners
The method of operation of premix burners, as described above, means that the flame develops only on the external surface of the combustion head, with combustion taking place very close to the metallic fibre of the blast tube. The result is extremely compact flame geometry, so that its effective length is practically the same as the combustion head itself. The flame diameter is directly related to the burner firing rate and is more compact than a diffusive flame.
The geometry of the gas ports is designed specifically so that, throughout the modulation range, the speed of the air/ gas mixture is sufficient to avoid burn-back. Premix technology also offers a much lower risk of flame impingement, due to the reduced likelihood of contact of the flame with the combustion chamber walls.
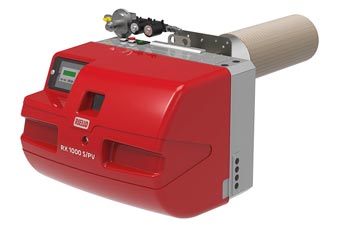
Additionally, the high combustion intensity developed on the premix burner head means that a greater heat output is achieved over a much smaller combustion head dimension compared with other burner technologies. In certain applications this enables the combustion chamber dimensions to be greatly reduced, resulting in lower manufacturing costs.
A key factor is the design of the combustion head, which can vary. The combination of premixing the gas/air mixture, the even distribution of gas over the surface of the burner and more precise heat control serve to reduce combustion temperature and, therefore, thermal NOx.
Riello’s design uses a seamless knitted wire for the sock that allows its application around the support without any welded seams. Thus critical situations to components caused by thermal stress are eliminated. Moreover, this technology allows for an even distribution of the heat along the length of the combustion head, also providing precision of heat control.
Riello can supply premix packaged burners in outputs from 5kW to 3MW, which have been seen to regularly reduce NOx emissions to as low as 30mg/kWh, and have even gone down to 20mg/kWh in some independently witnessed site tests.
Summary
Optimum burner selection is determined by a wide range of considerations and the choice of FGR or premix will depend on factors such as the design and capacity of the boiler. The important thing is to be aware of the options and engage with appropriate experts to ensure the best solution.
www.rielloburners.co.uk | info.riellouk@carrier.com
Tel 01480 432144 | Fax 01480 432192