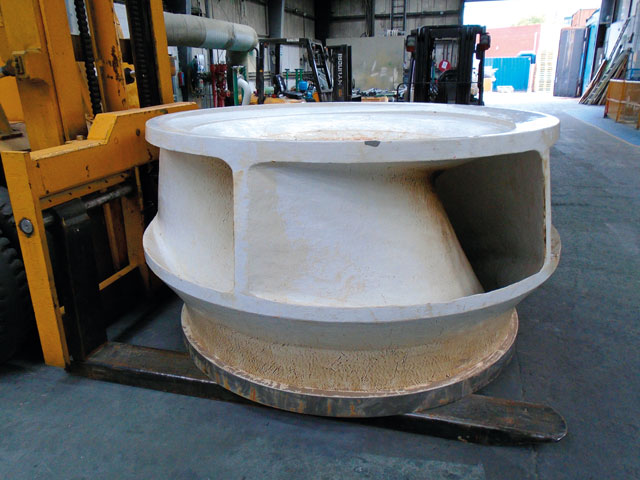
It is estimated that corrosion and wear costs the UK approximately £80 billion per annum.* But, what is even more alarming is that a considerable amount of these costs are completely avoidable, says Douglas Lynch, Corrocoat Technical Services.
Astronomical cost and time implications can arise due to numerous factors when corrosion occurs in industries of manufacture, engineering, oil, chemical plants and any other metal using industries. Consider for example, the situation of a power station that is cooled by two very large seawater circulation pumps (1.5 MW). There is a catastrophic failure of one pump due to corrosion and this causes a shutdown of half the power station. The major costs involved include production loss, statutory fines, maintenance costs, operation costs, transport costs, parts, mechanical refurbishment and coating refurbishment.
In most cases, the electrochemical corrosion process can be prevented, or at least the rate at which it occurs can be substantially reduced, by the elimination or the isolation of one or more of the primary components of a corrosion cell:
1. Anode
2. Cathode
3. Electrical Path
4. Ionic Path
Corrocoat coating systems stop and /or effectively slow down corrosion by isolating the metal substrate from the ionic path and on occasion, by eliminating the electrical path in equipment where dissimilar metals are coupled.
Whilst the permeability of organic binders on their own is fairly high, the barrier properties of organic coatings are achieved by the addition of fillers. The conventional method to protect against corrosion is to use a primer with inhibitive pigments overcoated with an adequate topcoat. The primer in this system typically protects the surface by either sacrificial means or passivation.
These types of systems can never be permanent because the inhibiting pigments are used up in preventing corrosion and the break down must occur eventually. This will occur quicker if the top coat is damaged and the primer is exposed to the environment.
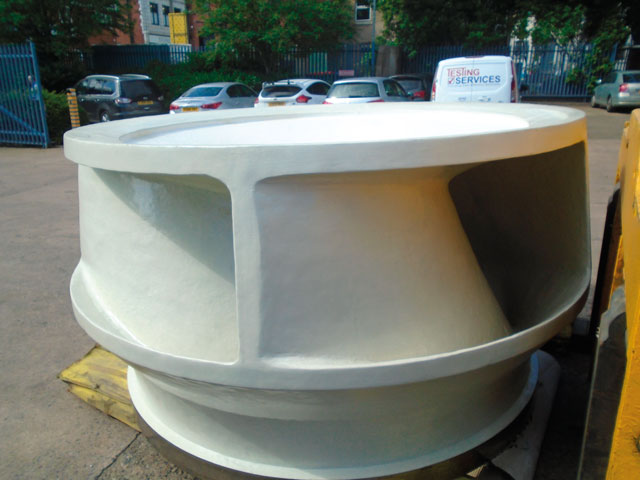
The addition of impermeable barrier fillers is effective as a tortuous path is created where the any moisture vapour entering the coating has to negotiate around the fillers to reach the substrate.
At Corrocoat, we use high quality impermeable ECR glassflake within our coatings. The high aspect of the glassflake i.e. the diameter being much greater than the thickness as well as the symmetry of the flakes, create a tortuous path from the coating surface to the substrate approximately 11 times higher than with ceramic filled systems. This reduces the Moisture Vapour Transmission to almost zero, leading to extremely long service lives. As you have now removed the ionic path, a component of the corrosion cell, corrosion cannot occur.
We recently worked on a project to repair and coat a main cooling water pump impeller, which we had previously coated 15 years ago; when the impeller was brand new and first put in to service.
The pump was returned for maintenance and repair, and despite 15 year of service operating in water with high sand content, the damage to the impeller was impressively minimal, with just a few areas of mechanical damage, and slight water damage and discolouration along the vein tips and edges.
There is no doubt, without the original coating system, that the pump would have been in such a good condition despite its operation in its aggressive service environment for over a decade, and repair costs would have undoubtedly exceeded the maintenance costs.
As previously highlighted in this article, for companies who must react further down the line when corrosion actually occurs and equipment begins to fail, there can be catastrophic time and cost implications.
Some clients deem their equipment unrepairable and often purchase replacements, instead of considering corrosion protection as a viable and cost effective solution. At Corrocoat, we are extremely confident in stating that even the most severely damaged piece of capital equipment can be refurbished by us, at a fraction of the cost of replacement.
*According to a study carried out at The University of Edinburgh.
www.corrocoat.com | info@corrocoat.com | t: 0113 2760 760