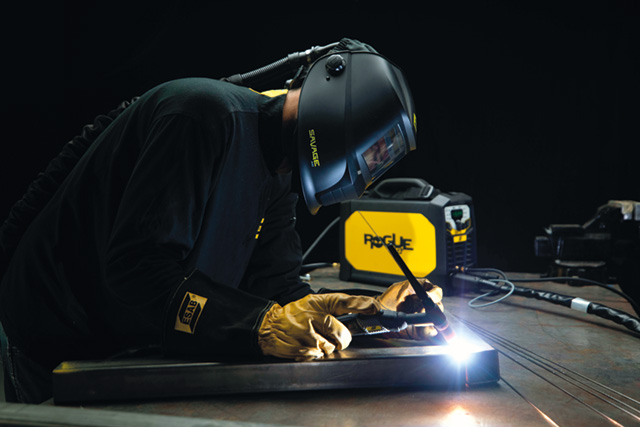
ESAB Product Application Manager Simon Marks gives advice for selecting equipment for welding and cutting for users who may not be familiar with the latest technology.
When it comes welding and cutting equipment for maintenance and light fabrication, choosing the right tools helps those with average skill produce higher quality results and enables the best workers to maximise productivity.
Inverter-based Welders
Each welding process has its strengths and weaknesses (Fig. 1). In the past, facilities often made do with an MMA welder in the maintenance shop and MIG welders for fabrication. The units could weigh 50 kg or more, had limited adjustability and limited location flexibility.
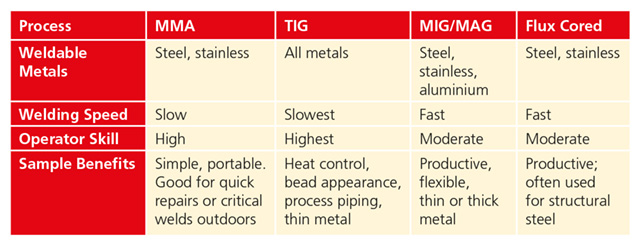
Inverter-based welding power sources offer a host of benefits depending on the application. The “inverter” part of the name refers to how the unit converts primary power to welding power using ultrafast power switching devices and microprocessor controls. Today’s inverter technology is extremely reliable and offers many advantages:
• Lightweight portability so the operator can move the welder to the work site. For example, an inverter with outputs for MMA and TIG can weigh10 kg or less. A professional-grade unit, such as the ESAB Rogue ET 200iP PRO, offers advanced arc control functions to improve MMA performance, pulsed TIG to control heat input and a high-frequency TIG arc start, which is required by many codes for welding process pipe.
• Input power flexibility. Some inverters can use 230V input for welding thicker metals and, with the addition of an adapter plug, connect to a standard wall outlet for location flexibility. A small multiprocess inverter with dual-voltage capabilities weighs less than 20 kg and can weld metal up to 9.5 mm thick. Higher-end units provide outputs for MMA, MIG, flux cored, DC TIG (for ferrous metals) and, in the case of the ESAB Rebel EMP 205ic AC/ DC, an AC output for TIG aluminium.
• Superior arc characteristics. With microprocessor controls, inverters can sense changing arc conditions and adjust the welding output in milliseconds, improving welding results.
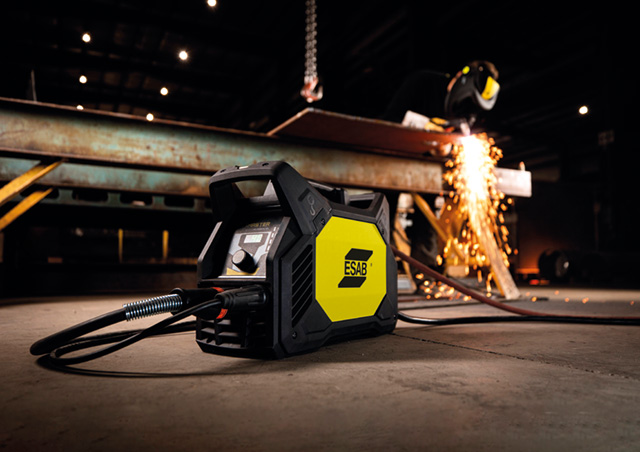
The new generation of inverters enables users to complete jobs faster and with higher quality. As an example, a function called Smart MIG simplifies set up and monitors the operator’s technique and continuously adapts to provide a stable arc to reduce spatter and improve control. Smart MIG makes it easy to switch between jobs, helps train new operators and can improve consistency between welding stations.
Plasma Cutting
Plasma cutting takes ordinary shop air and turns it into a superheated jet of plasma gas that slices through any metal like a hot knife through butter. For work on thinner materials (up to 6mm), a machine with an output of 35 amps is suitable. If you plan to cut metal up to 12mm, look for a machine in the 40- or 45-amp category. For metal up to 20mm, a machine with an output of 60 amps or more is a better choice.
Note that plasma cutters have “cut,” “sever” and “pierce” ratings. The edge quality on the cut rating will be of good quality. The sever rating will be for thicker material, but the cut surface will be rougher. If you want to start a cut in the middle of the plate instead of the edge, be sure to check the machine’s pierce rating.
Inverter-based plasma cutters pack a lot of cutting power into a lightweight package (10 to 15 kg). Operators can easily carry to the job site, get more work done with faster cutting speeds, make precise cuts on thin to thick material and trace templates for cutting shapes. Lastly, the newest generation of plasma cutters simplifies set-up and operation with features such as LCD screens and automatic gas pressure adjustment, a boon for occasional users.
www.esab.co.uk | cheron.robinson@esab.co.uk |
t: +44 (0) 1992 70244