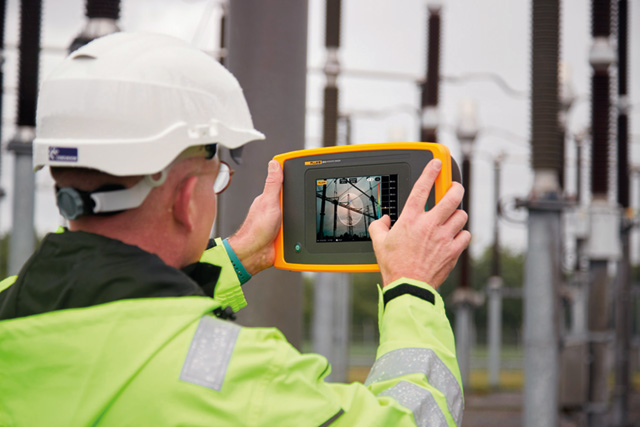
With partial discharge seen by many in the industry as the main cause of long-term damage and subsequent failure of electrical insulation, Alexander Bardakov, Industrial Imaging field application engineer at Fluke Corporation, takes a detailed look at the phenomenon and provides guidance on how to mitigate the issue.
Partial discharge
Partial discharge is an electrical discharge that does not completely bridge the space between two conductors and can occur in medium and high voltage electrical equipment. The phenomenon occurs on pieces of equipment such as high-voltage lines, transformers, turbines, bus-bars inside of cabinets, etc. The issue is commonly found at electricity generation facilities, transmission networks and distribution grids.
The implications
Typically caused by a minor defect and resulting in thousands of small repetitive discharges, a partial discharge grows over time. It can have many damaging effects on equipment because of mechanical, heat, and chemical damage to insulators and conductors. These can have significant safety, efficiency and financial implications.
The occurrence of partial discharge may indicate the conditions necessary for an arc flash which, although rare, can be considered a hazard. An arc flash occurs when due to the electrical break-down of the air, a plasma channel is created.
Partial discharge can have a significant impact on the maintenance schedule for utility companies and grid operators.
Over time partial discharges cause the degradation of components which can negatively impact the performance of equipment and infrastructure. Within these critical industries, equipment failure or unplanned downtime can have a significant social and economic impact.
As (ad-hoc) emergency maintenance comes at a higher cost, preventive maintenance is fundamental to a cost-effective maintenance program. Early insights from partial discharge detection equipment can help avoid equipment failure and ensure spare parts are available before a catastrophic failure.
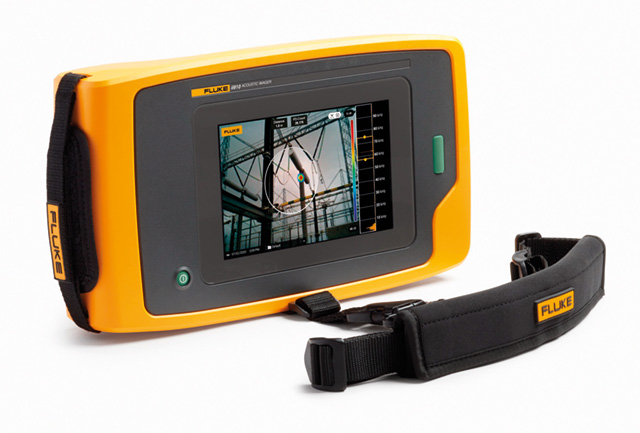
Identifying partial discharge
A visual inspection may reveal mechanical, thermal or chemical degradation caused by previously undetected partial discharge.
Oscilloscopes can be used to determine the presence of partial discharge. Whist with UV cameras engineers would often need to take numerous images of a power plant to identify the location of partial discharges. Each method requires advanced training for the engineer.
With this in mind, leading instrumentation companies have been looking at a new identification and analysis tool in the form of acoustic imagers. The vibrations caused by partial discharge are often beyond the range of human hearing. Acoustic imagers can help engineers quickly scan a power plant or electrical substation and easily identify the partial discharge places of concern. They also require minimal training ahead of use.
Advancements in detection
One instrumentation company that has developed a tool based on acoustic imaging technology is Fluke, which recently launched its ii910.
The durable, handheld casing of the Fluke ii910 has an LCD touchscreen which overlays a SoundMap™ image on a visual image for rapid identification of discharge between frequencies of 2-100kHZ. The array of integral microphones converts ultrasound signals into clear visual images on the backlit touchscreen.
Captured data can be transferred via an integral USB-C socket directly to a PC. Images and data can be uploaded to a reporting platform, which will provide analysis and insights into the type of partial discharge so that maintenance schedules can be prioritised.
A sound future
While partial discharge is a phenomenon that can cause catastrophic damage, these issues can be avoided if the partial discharge is identified early. While in the past engineers have found old identification methods slow and inefficient, a new wave of tools are now available which can aid them in their mission to optimise operations while minimising risk.
www.fluke.com | sales.uk@flukenetworks.com |
t: +44 (0)20 7942 0708