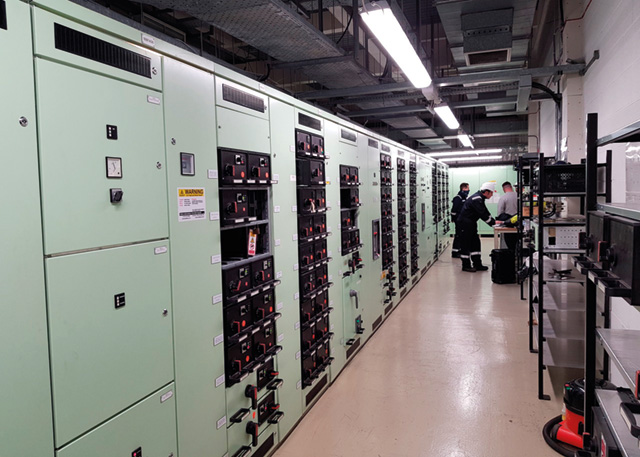
Geoff Walker of Faraday Predictive reports on how a new generation of condition monitoring technology is prompting a deeper understanding of machine behaviour.
Vibration Monitoring is often stated to be the most widely used form of condition monitoring. Since it first became a viable industrial method in the late 1960s/early 1970s, vibration monitoring techniques and technology have continued to develop, together with the associated understanding of machine behaviour.
The latest example of this is the torsional behaviour of machines being revealed by MBVI systems, which has led to in-depth mathematical research to explain these patterns of behaviour.
A brief History of Vibration-based Condition Monitoring
We can think about vibration monitoring as having developed in three separate phases – each one of which has led to significant scientific and mathematical R&D to understand what the sensors were telling us, and in the process, deepened our understanding of machine behaviour.
The first generation – Proximity probes for use in journal bearings prompted understanding of shaft bending resonant responses
Proximity probes such as those developed by Bently Nevada in the 1960s measure the radial movement of the shaft relative to the machine casing and bearing journals. These systems were mainly used to identify problems with large, supercritical machines where deflections of the entire shaft can be significant – effectively the shaft can be regarded as flexible.
Observations of the movement of the shaft position relative to the machine bearing housings led to the development of Rotor Dynamics as a separately identifiable mathematical discipline. A key area of this work focussed on the different lateral bending modes of shafts, each with their own distinct resonant frequency. This also led to new insights into understanding of elastohydrodynamic lubrication.
These systems are still used on large, highly critical, journal bearing machines.
The second generation – Seismic sensors prompt deeper understanding of rolling element bearing failures
Whereas prox probes measure relative movement between different parts of the machine, seismic sensors (including velocimeters and accelerometers) detect movement of the entire machine in space.
These proved to be much more useful for monitoring progressive deterioration of Rolling Element bearings. As detection techniques improved, earlier sensing became possible, and this deterioration was classified into four distinct phases, as shown in figure 1 below.
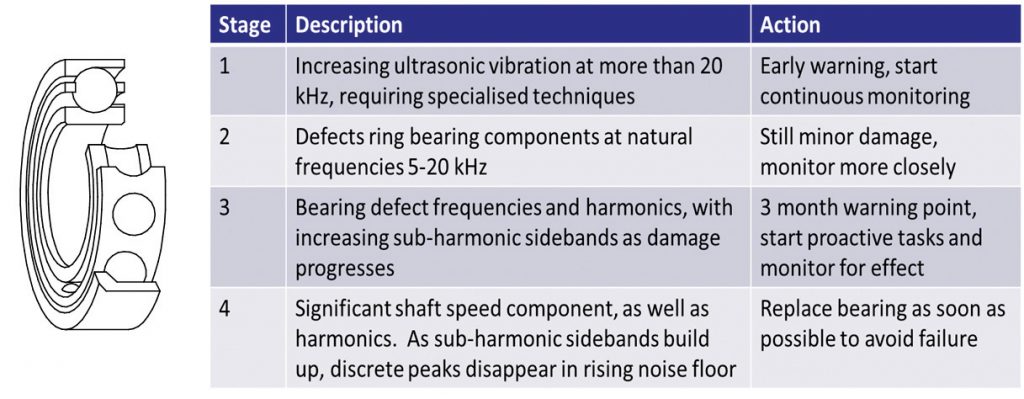
The third generation – MBVI systems, sensing changes in torsional behaviour using the electric drive motor as a sensor
NOW – the use of MBVI gives us an insight into torsional behaviour of machines, and is prompting mathematical work to understand subharmonic and non-linear behaviour of machines.
Model-Based Voltage and Current (MBVI) systems effectively use the motor as a sensor. The variation in motor current associated with variations in load create a signal related to torsional vibration.
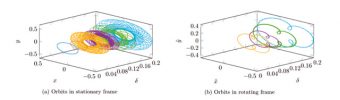
The same phenomena that are detected by conventional Vibration Analysis systems are also detected by MBVI systems, but with different sensitivities. Certain phenomena such as rubbing friction, flow turbulence and belt drive behaviour, show up much more clearly in the torsional domain, which results in new insights into machine behaviour.
These systems also detect signals subharmonic signals in a way not generally seen with conventional Vibration Analysis. Fundamental Mathematical Research to understand these phenomena shows some fascinating patterns of the way shafts behave, some of which are shown in figure 3.
Advantages of MBVI systems include the ability to monitor inaccessible assets – because sensing is done in the switchgear which is always accessible even when the machine itself isn’t; sensitivity to things conventional VA doesn’t see so clearly (torsional signals – including corrosion, belt drives, and rubbing; plus of course seeing electrical phenomena and energy consumption not visible to conventional Vibration Monitoring).
So What?
While there is no one Condition Monitoring technology that is perfect for every situation, MBVI systems offer a very wide range of coverage (Mechanical and Electrical and operational) across the entire machine (motor + transmission + driven equipment) all from one device, and have advantages when trying to monitor inaccessible machines. They also have advantages when monitoring Inverter driven machines.
www.faradaypredictive.com | info@faradaypredictive.com | t: 0333 772 0748