AMETEK Spiro Scientific Director, Product Management & Technical Sales, Dan Walsh and Reliability Consultant Ray Garvey argue that passionate technicians are one of the keys to successful lubrication and oil analysis.
Supply chain disruptions with materials and energy inflation hurt company profits more this year than in 40 years. Reliability of facilities and equipment is directly linked to financial performance as never before, and your lubrication and oil analysis programs are key to availability.
Lubrication
Proper Lubrication is an essential aspect of machine reliability. Oil lubricants literally support machine components, plus they do much more.
Functions of Lubricants
1. Provide fluid film
Lubricants provide anti-friction film to separate moving components, eliminate adhesion and reduce wear.
2. Provide Cooling
Lubricants reduce friction and transferring heat away.
3. Remove Contaminants
Lubricants clean surfaces and transfer contaminants for removal.
4. Protect and Seal
Lubricants provide barriers to seal components from exposure corrosive and abrasive substances.
5. Perform Work
Lubricants perform work by transferring compression force and eliminating shear force between very highly loaded moving components.
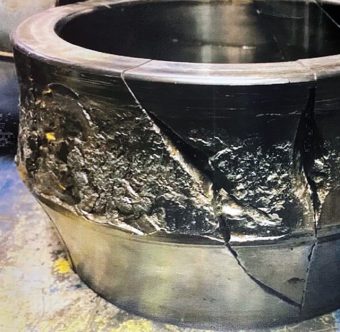
cracking
Inadequate lubrication occurs when the fluid film strength fails. Several causes lead to inadequate lubrication: low oil level, no oil, elevated temperature, wrong oil, slow speed, and excessive loading. Metal-to-metal contact from inadequate lubrication causes adhesion and severe sliding which produces metal oxides and metallic wear debris in the oil.
When lubricants fail to provide cooling, extreme temperatures cause adhesion, severe sliding, and catastrophic failure.
A clean lubricant is needed to clean machine components and transfer contaminants for removal in a compartment or filter. Target cleanliness levels (TCLs) specify allowable moisture and particulate contamination thresholds for effective removal of contaminants. Excessive moisture and dust contamination leads to corrosion and abrasion within machinery systems.
Inadequate protection and sealing of surfaces enables moisture and particulate contaminants to oxidize surfaces, promote stress corrosion cracking, support galvanic corrosion, and generate abrasive wear.
Inadequate work performance often occurs when oil lubricants are excessively contaminated with moisture and particulates or when varnish formation precipitates out of the oil. For example contaminants damage seals and varnish deposits deteriorate control valves.
Oil analysis
Oil analysis measures quality and performance of oil lubricants. “Every successful oil analysis program I have observed has passionate technicians performing the work. And almost without exception, each includes some degree of onsite oil analysis.”
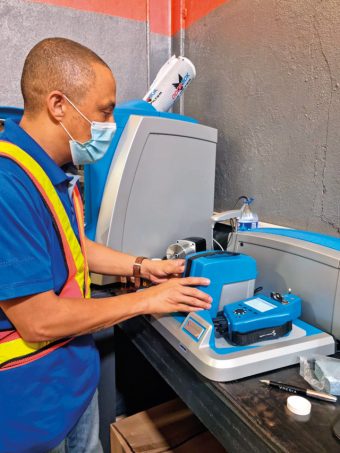
An advantage for onsite oil analysis compared with offsite laboratory analysis involves accumulation of valuable predictive maintenance know-how. There is no substitute for practiced firsthand experience, technical understanding, equipment manuals and specifications. Onsite analysts have ready access to databases that receive, accumulate, and report knowhow that would otherwise have been lost when individuals change jobs.
Onsite oil analysis is proactive. Root causes of issues are identified and corrected early. Acceptance testing is performed to verify identity, cleanliness, and to avoid misapplication. In-service lubricants are tested against target cleanliness levels (TCLs) for moisture and particulates. Also, correct oil levels are verified, desiccating breathers are inspected, and other problems are noted. When the plant maintenance staff pays particular attention to the condition of lubricants, they will surely notice common problems such as water-in-oil, wrong lube, or in rare instances, no lube at all.
Onsite oil analysis is predictive. Onset of damaging failure mechanisms are detected and wear progressions are trended. Parts per- million (PPM) of wear metal alloys such as iron (Fe), lead (Pb), copper (Cu), and tin (Sn) may identify wearing components. Total ferrous measurement and particle shape classification identify fatigue wear, severe sliding, and inadequate lubrication issues.
Motivated technicians with firsthand experience and technical understanding, use state of the art, automated minilab instruments to measure the effectiveness of contamination control initiatives, to prevent misapplication of lubricants, and to predict and plan for
component repairs. These planned repairs reduce likelihood of unplanned repairs that impact production.
www.spectrosci.com | sales.spectrosci@ametek.com | t: +1 (978) 486 0123