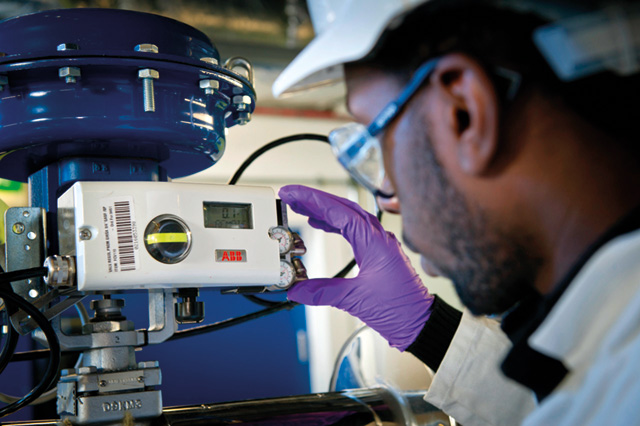
vibrations up to 10g and 80Hz
When it comes to boiler control, selecting the right types of valve actuators and positioners is key. Naas deJager, Global Product Manager for ABB’s actuator and positioner products, reviews the key challenges that can arise in boiler control applications.
Growing awareness of the impact of human activities on the environment, and tightening legislation, is putting industrial companies under increasing pressure to minimise emissions.
For companies that rely on combustion-based processes, there is a need to ensure the right conditions are achieved for optimum efficiency. Widely used throughout power plants to provide precise and continuous positioning of the final control elements used to control flows of air and other variables, actuators and positioners can make a big difference to combustion performance and ensure the highest levels of boiler control.
Start up and shutdown
As complex pressurised systems, boilers require careful handling during start-up and shutdown. Best practice for start-up requires small quantities of steam to be introduced over a prolonged period through accurate control of the start-up valve.
Valves used for start-up or shutdown remain in the same position for long periods, causing corrosion of the valve seats and increasing the amount of break-away force needed to actuate the valve.
One solution is to use a device with double-rated force/torque, such as ABB’s Contrac series. The variable force/torque design ensures that only the required energy is delivered, minimising the strain when varying the valve position. These types of actuators provide the high accuracy needed to ensure optimum control of steam and water flows during boiler start-up and shutdown.
Injection valve control
Injection valves are used to add cooling water at the superheater and reheater stages, reducing the temperature of superheated steam prior to it being introduced into the turbine. Various control measures are taken to maintain the steam temperature within a specified range.
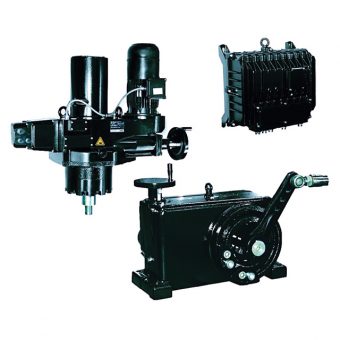
that only the required energy is delivered
Although these measures can help protect the superheater, turbine and secondary plant components against overload, they can also impact turbine efficiency. Typically, efficiency is reduced by around 0.05% for every 1°C reduction of the turbine inlet temperature. This can quickly add up resulting in significant economic losses.
Many operators unwittingly incur these losses by using the wrong actuators for injection valve control applications. Problems often arise where devices are selected with the wrong duty cycles – the ratio of on-time to off-time – and the wrong ambient temperature range. The solution is to use an actuator with S9 100% duty capable of operating at high ambient temperatures. A positioning accuracy of ±0.05%, can provide the precise control needed to enable the turbine to reach and maintain its operating setpoint.
Hitting the combustion sweet spot
Achieving optimum combustion efficiency requires the correct amount of air to be supplied to completely combust the fuel being used, an ideal situation known as the stoichiometric air/fuel mixture. The ability to hit the combustion sweet spot and burn the maximum amount of fuel is key to reducing unwanted by-products such as excess CO2 and NOx emissions that can arise with poor combustion control.
With fuel prices increasing, optimising the fuel/air mix can make financial sense too. A 1% reduction in excess air levels produces anything from a 0.25% to 1% increase in boiler efficiency. Using continuous electrical actuators can help provide the levels of precision and responsiveness needed.
A good position
Adverse operating conditions, such as high ambient temperatures inherent in boiler applications and process vibrations, can cause the accuracy of standard pneumatic positioners to drift, resulting in impaired damper control. Look for a positioner that can operate in ambient temperatures up to 100°C and offer immunity to vibrations up to 10g and 80Hz.
A high-performance positioner with a remote sensor which can be situated with the actuator up to 10m away from the positioner control module helps to improve access for maintenance.
Tried and tested
The harsh and demanding nature of boiler applications calls for valve control equipment that can keep on providing accurate and reliable performance with minimum requirement for maintenance. Seek tried and tested actuators and positioners that have demonstrated their ability to provide continuous, cost-effective operation with no deterioration in performance.
new.abb.com/products/measurement-products | enquiries.mp.uk@gb.abb.com | t: 0870 600 6122