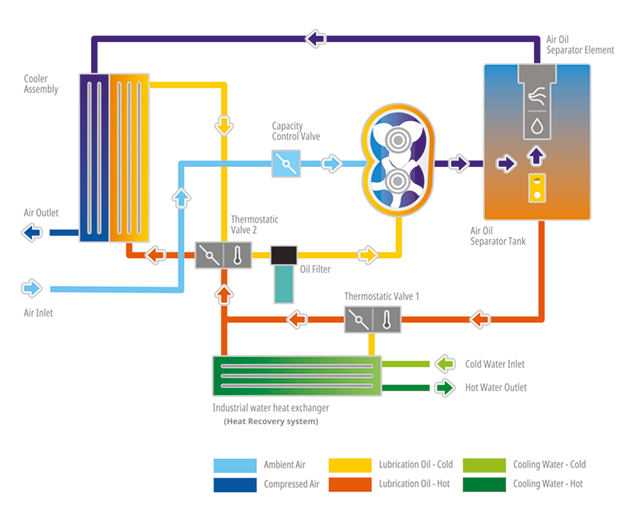
Operations of all sizes now have the tools required to improve energy efficiency and utilise heat from their compressed air systems, says David De Pril, Head of Product Management and Marketing, ELGi Europe.
Why aren’t more small and medium-sized manufacturing operations recovering the heat from their compressed air systems? Why has the usual ‘trickle-down’ effect from larger operations taken so long? The potential in energy savings is obvious. The emission reduction benefits are clear and the return on investment (ROI) is high in a short span of time.
All the talk is of energy efficiency and waste reduction or elimination – and for a good reason too! It is estimated that the industrial sector in the European Union is responsible for 20 to 25% of the total energy consumption. Eliminating waste energy is not only the right thing to do but makes good business sense too – no matter the size of your operations.
How much heat are we talking about?
In a typical oil-injected compressed air system, the theoretical recoverable heat is 96% of the overall electrical energy consumption. It consists of heat dissipated in the oil cooler (78%), the aftercooler (13%), and the heat radiated from the drive motor (5%).
The remaining 4% of heat cannot be recovered since 2% radiates through the canopy and the other 2% vents inside the canopy.
There is no one-size-fits-all approach for heat recovery. Factors such as the localisation of the air compressor to the process, hot water needs, or complete air system play a significant role, but so does the type of compressor running.
From the beginning
Using waste energy is of course not a new concept. For decades, energy savings were recognised by various industries where the immediate payback from a small initial investment was clear.
In fact, over the lifespan of a typical compressor, energy typically costs several times more than the purchase price of the compressor. The bottom line, maximising energy efficiency saves you money.
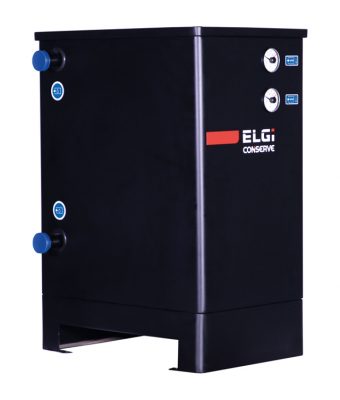
Heat recovery uses
Typically, operations that require process heat and have 24/7 operations will witness a significant return on investment from heat recovery – often in under a year and rarely in more than two years.
While not all recovered heat use is equal, there are still huge benefits to be had for other operations. Adoption during the winter months for example results in significant cost and carbon emissions benefits. These benefits have not been lost on some in the industry, with heat recovery applications for both space heating and water heating for human comfort, (facility heating) becoming increasingly popular in recent years.
In such cases, the heat is used as an additional heating source, which in turn reduces the requirements placed on traditional carbon-fed boilers thereby reducing separate heating fuel costs and resulting in reduced carbon emissions.
In cases where the recovered heat is used for heating water, we see an efficiency of upwards of 85%, rising to 96% in fully optimised operations, and in the case of space (air) heating, an efficiency of 60 to 70% can be achieved. With such results, operations will often see a short-term return on their investment of between one to three years.
Technology application
The compressed air industry has made great advances in improving the capacity, reliability, and energy efficiency of compressed air systems, addressing these priorities for operations of all sizes.
While the pace of this innovation continues unabated, ELGi is bringing cost-sensitive ‘plug and play’ Heat Recovery Systems to the market. Combined with a greater operational focus on energy auditing and system performance compliance with global standards on energy management (such as ISO50001), small and medium sized operations can reap the benefits of heat recovery more easily than ever before.
The maths are clear
The tools and technologies are available for operations of all sizes to benefit from heat recovery. A high return on investment brings immediate cost savings and more importantly, carbon emission reductions help you in lowering the company’s net carbon footprint. Heat recovery is not just the right thing to do for the future of our planet, but it makes good business sense too.
Small and medium-sized companies have the tools and opportunities now to stay ahead of any regulatory changes, to meet customer (and their downstream consumer) demands for improved sustainability, and ultimately improve their never-ending productivity targets.
www.elgi.com/eu | euenquiry@elgi.com | t: 0800 844 52 60