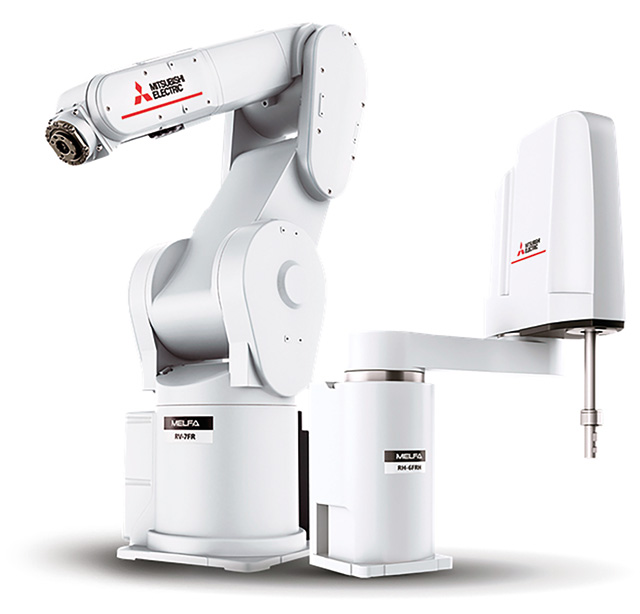
When using future-oriented automated technologies, such as robots, it is important to use equally advanced solutions to support their optimum operation and maximise service life. Barry Weller, Robotics Product Manager at Mitsubishi Electric, looks at why specifying robotic solutions that leverage predictive analytics for on-point maintenance is a must.
Robots are integral in helping companies grow in the market, and businesses across a multitude of industries are well aware of this; the number of robot installations in factories around the world grew by a record 31% in 2021. This new figure brings the total units currently in use up to 3.5 million, an estimated 24,445 of which are in the UK.
While industrial and collaborative robots are becoming increasingly popular on shop floors, it is still extremely important to look beyond the price tag. Companies should determine the payback period associated with the purchase of a robot and how to maximise their return on investment (ROI) before installing them.
Key aspects to consider include equipment service life and maintenance requirements as well as potential costs arising with unexpected downtime, repairs and replacement parts.
In practice, the average service life of a robot is estimated to be around 15 years and its maintenance cost tends to be incremental. In the first few years, the expenses are typically associated with preventative measures, such as lubrication and battery changes, but after long term use it is essential to replace worn components, such as drive belts.
Towards the end of a robot’s lifecycle, more considerable, costly activities are to be expected. For example, up to 50% of the robot’s asset value may be spent on refurbishment projects.
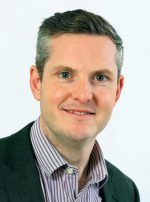
‘Selection of a robotic system with built-in advanced maintenance features can add value to industrial automation applications.’
Barry Weller,
Mitsubishi Electrics
Advanced solutions to save money
Well designed planned, preventative and corrective maintenance strategies can help users reduce a robot’s total cost of ownership (TCO), increasing its expected service life while ensuring peak performance throughout.
However, the use of cutting-edge, data-driven forecasting systems can deliver even greater benefits. These gather information on the status of the robot and its components, identify and evaluate the level of wear and other anomalies, predict when failure is likely to occur and offer a suitable maintenance schedule.
In addition, these solutions can be coupled with prescriptive tools, which explore and present mitigation recommendations to address equipment wear and failure. This, in turn, can streamline troubleshooting, servicing, repair and replacement activities.
Accurate predictive and prescriptive methods often rely on large volumes of data and state-of-the-art artificial intelligence, elements that require high levels of technical expertise and time. As such, it may be challenging for end users to set up future-oriented, competitive strategies to extend the service life and optimise the TCO of their robots.
Leveraging maintenance-oriented robots
The selection of a robotic system with built-in advanced maintenance features – for example condition monitoring, predictive analytics and prescriptive technologies – can add value to industrial automation applications.
To help companies benefit from state-of-the-art automated machines with a long service life and limited running costs, Mitsubishi Electric has developed the MELFA Smart Plus option. This can be added to any of the company’s industrial, collaborative and cooperative robots, offering condition monitoring and predictive maintenance functions.
MELFA Smart Plus is characterised by highly accurate predictive models that check the status of key robotic components and identify abnormalities. This is made possible by Mitsubishi Electric’s enormous library of data on robotic component wear, coupled with its artificial intelligence technology ‘Maisart’.
MELFA Smart Plus also enables prescriptive operations, as it is linked to the robot cloud maintenance solution, which suggests maintenance times and priorities for various parts. Thanks to these functions, companies can benefit from planned servicing, repairs and replacements before equipment fails, helping to optimise uptime and costs.