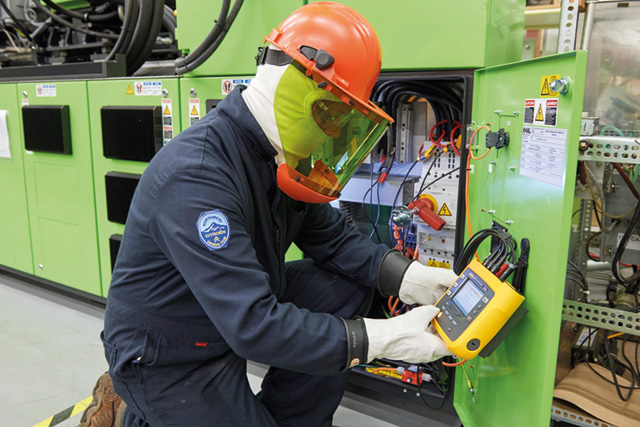
Automation of industrial processes brings with it many benefits, but it also presents new challenges, explains Fluke Reliability’s lead SME manager Frederic Baudart.
Huge amounts of time and effort can be saved with automation, particularly in tasks that are simple and repetitive. But the sheer complexity of modern systems can make fault diagnosis difficult.
Automation in itself is nothing new. The Ancient Greeks invented devices that made use of feedback control loops to drive mechanical components without human input. In the Industrial Revolution, the harnessing of water and steam ushered in a new era of productivity.
The mid 20th Century saw electrification of automated processes, laying the groundwork for computerised control systems. The Fourth Industrial Revolution – or ‘Industry 4.0’ – is an era of digitalisation and hyper-connectivity. Internet of Things enabled devices can talk to each other, and take action based on an almost infinite number of variables, autonomously or semi-autonomously.
New breakthroughs await. Innovations such as AI and Blockchain promise much in terms of productivity and efficiency, but are yet to reach critical mass. Crucially, almost every device across the modern factory requires power to at least some extent. Ensuring adequate power quality across an entire plant is vitally important.
Power quality issues
Automated equipment can be particularly sensitive to power quality issues. They can cause equipment to run erratically, inefficiently, or not at all.
There are several types of power quality event. These include:
• Voltage dips, swells and interruptions – variations in the supply voltage
• Transients – temporary unwanted voltages, which can vary in severity and duration
• Unbalance – inequality between phase voltages of a three-phase system
• Harmonics – distortion in the current and/or voltage, which causes the waveform to deviate
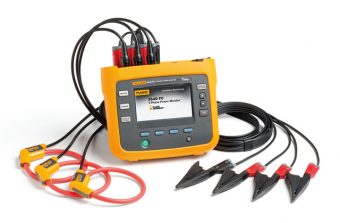
Most issues can be resolved relatively easily. However, they must be detected and diagnosed in the first place. With effective power quality monitoring systems, operators can access data they need to understand the issue, infer the cause, determine how long it has been present and come up with a solution.
Sensor technology and monitoring systems have become more sophisticated in recent decades.
Modern monitoring systems can combine historical, current and trend data to quickly and efficiently diagnose latent, emerging or unexpected issues. But it is advisable to follow established processes to ensure problems are investigated, diagnosed and remedied quickly. These include:
1. Gathering information – It is important to have access to monitoring data. Understanding what has happened before is crucial to understanding what is happening now. Also, human it comes to legacy equipment. Checking with those who know machinery intimately can help uncover issues. knowledge is as important now as it ever was, particularly when it comes to legacy equipment. Checking with those who know machinery intimately can help uncover issues.
2. Taking measurements – The next step involves taking measurements. An instrument such as a power quality analyzer can help find and fix problems quickly. If possible, it is good practice to install the power quality analyzer before switching the breaker back on. Once the tool is installed, be sure to double check the connections, while considering:
• Are the voltage leads connected to the right phases?
• Are the current probes connected to the right phases?
• Are the probes oriented correctly?
Check the reading on the measurement device. Modern analyzers, such as Fluke Reliability’s 3540 FC series of three-phase power monitors, will often have a feature that automatically indicates correct connection. This particular device measures power (A), voltage (V), power (W), frequency (Hz), apparent power (VA), reactive power (var) power factor (PP), and total harmonic distortion / THD (%) as either a mobile or stationary unit. If limits are exceeded or undercut, the system automatically issues an alarm.
3. Power up the system – Next, reset the breaker and return power to the system. At this point, it is important to consider:
• Is the voltage within the expected tolerance of +/- 10%?
• Is the current being drawn to the expected range?
If the voltage is outside of the expected tolerance or the current draw is too high, the breaker might trip. Power factor is also a consideration: a factor below 0.85 is wasteful, and can indicate loading problems. However, this is relatively easy to fix. Check the total harmonic distortion (THD) – this can indicate some loads are creating problems.
4. Leave the data analyzer in place – If you are no closer to finding the cause of a power quality issue, a further step can be to leave the data analyzer in place so continuous information can be logged. If the breaker trips a fourth time, the logger can capture everything that happens both before and after the trip. This can help provide a timeline of events and conditions that led up to the trip, which can then inform the correct solution to resolve it.
www.pruftechnik.com/en-GB | ptuk_sales@pruftechnik.com | t: 01543 417763
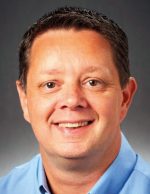
Frederic Baudart
Lead SME Manager
Fluke Reliability