Sophisticated storage systems used in large warehouses have evolved into smaller, smarter and lower cost versions for smaller operations. SSI Schaefer business development and marketing manager Mike Alibone explains.
Automation has been in use in large distribution centres and manufacturing operations for decades. What is new, however, is the way in which it has evolved, grown and diversified, particularly over the past five years.
The backbone of automation in large storage facilities, controlled by IT systems of varying degrees of complexity, has traditionally been provided either by pallet-based or smaller, container-based automated storage and retrieval systems (ASRS) and conveyors. Such installations have required considerable investment, resulting in a return on investment of anything between three and five years.
Using this as a foundation for further development, low-cost automation or “mechanisation” is now spreading from such facilities to smaller warehousing and storage operations in manufacturing industry. The key requirements of small and medium-sized operators revolve around economy of space, flexibility of internal transport and a rapid ROI. The use of “easy” automation to fulfil these requirements is on the increase as simple, smart storage systems with rapid installation times are introduced to make operations more productive and efficient.
No ceiling on storage
One such example is the vertical lift storage machine (VLM) which, occupying only a small area, makes full use of a building’s height, thereby using previously wasted space or the “fresh air” above conventional shelf-based systems.
As well as saving space, this type of machine increases picking speed by reducing the time operators spend walking to pick items. Effectively acting as a “mini-ASRS”, a VLM, such as SSI Schaefer’s LogiMat, employs an internal load-handling device which operates in the same manner as a crane, delivering the required products on trays to a ground-level picking window.
The VLM is ideal for storage of small parts as well as for long items, and it can be integrated into a warehouse management system or used on a stand-alone basis.
On track for just in time
VLMs are commonly used in conjunction with standard conveyors, both for stock replenishment and for transporting picked items to production or directly to shipping. More recently, however, their use has become associated with automated guided vehicles, which are being employed with increasing frequency to take components to production lines, as well as to serve other areas in the plant.
AGVs offer a more flexible alternative to transport than conveyors, which are restricted to fixed routes and present barriers to the flow of other vehicles and pedestrians. AGVs are basically robots, which use floor markers, wires, or laser vision to navigate through a building. Some are guided by magnetic floor tape, which means setting up and reconfiguring routes is simple.
Transponder tags are used to indicate when the AGV should stop or perform a specific action, such as increasing or decreasing speed, lifting or lowering. AGVs can interface with conveyors at docking stations to receive or deposit goods, and their load-carrying devices can be modified to carry hanging goods.
The advantages of using them to manage the flow to production lines without manual intervention is a boon to manufacturing. And with costs proportionally lower than more traditional forms of automation, sophisticated storage and handling systems based on this type of technology are realistically within the reach of progressively smaller operations.
Faster flow for Toolstream
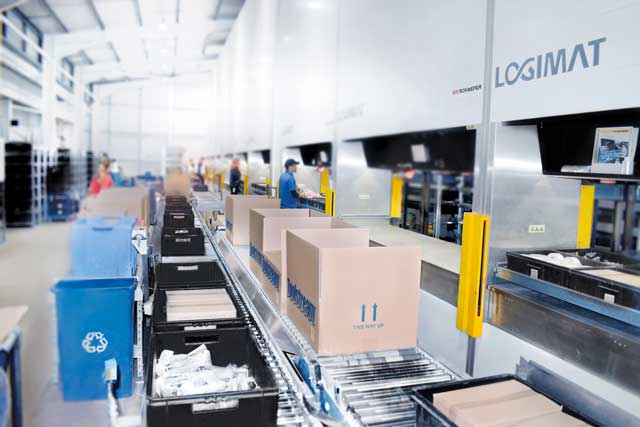
In 2015, SSI Schaefer undertook an analysis for Toolstream, sole distributor of more than 6,000 branded hand tools, power tools, hardware and fixings, of its operation in Yeovil and devised a solution to satisfy the increasing demand both for storage space and faster order processing. Prior to this, picking was carried out using trolleys in very narrow aisle, adjustable pallet racking. Though each trolley could accommodate up to ten orders simultaneously, pickers were walking over 1.2km per order, and trolleys would face queueing at packing benches, forming bottlenecks and slowing down despatch.
To overcome both issues, space was used more efficiently by installing a bank of 14 vertical lift LogiMat machines.
To improve the pick rate further, a conveyor system was installed alongside, and parallel to, the VLMs. The conveyors are fed by three carton-erector machines, bringing shipping cartons, automatically pre-labelled with unique, order-related barcodes, to pickers working at the LogiMats. This allows system-directed cartons and totes to be diverted from the conveyor to the correct VLM zone, where operators can scan their barcodes to see what products need to be picked into them, before returning them to the conveyor for transport to the next zone.
The whole process represents a considerable saving on packing and has enabled Toolstream to reduce more than 30 pack benches to only two. It has also removed the backlog of picked orders awaiting packing.