In your company have you ever taken the time to calculate the cost to the business of equipment failures? Most companies have not or, if they have, they do nothing about it.
Peter Gagg, CEO of MCP Consulting Group, explains how root cause analysis can help to cut this cost by helping you ask the right questions to identify causes of failures.
As a rule of thumb, taking the figure of £1,000 per hour as the total cost of downtime will give you enough incentive to take positive action. If you calculate the total downtime hours per year for each production line and then multiply by 1,000, the answer will be in six figures.
A recent example from the food industry
A food company operating 10 filling lines tracked the downtime due to all causes on each of the fillers for a period of 12 months; the results are shown in Figure 1. The total annual lost output was 17,000 tons at £1,000 per tonne, equating to £17m.
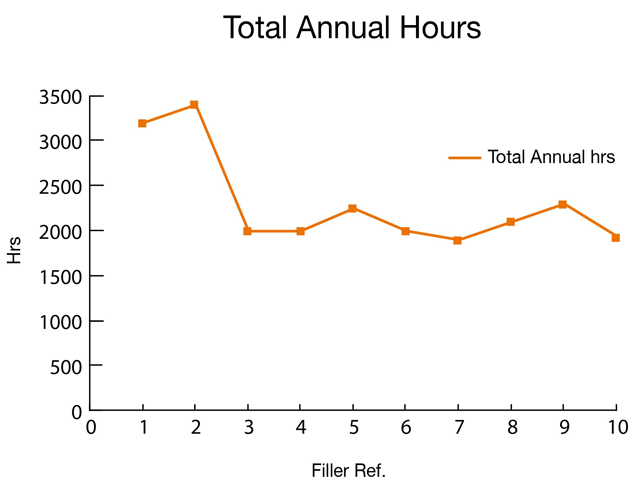
Using equipment performance data along with root cause analysis, improvements in performance and output can be achieved.
In this case, the food company set up a 12-week improvement project involving maintenance and production staff, with support from MCP. Analysis of existing maintenance data was followed by root cause analysis (RCA) techniques to determine the causes of downtime and the root failure causes.
After a deep dive analysis, which identified the lines with the biggest losses – lines 1 and 2 – action was taken to understand the reasons for the high losses on these two fillers and to identify any common issues affecting all ten fillers. Further analysis of the remaining fillers followed.
The result was a 25% reduction in downtime, which on an annualised basis equated to approximately 5,000 hours of extra production output, equivalent to 3,750 tonnes of product at a sales value of £3.75m.
The number of breakdowns decreased over the full year as shown in Figure 2, while the equipment reliability increased, shown in Figure 3.
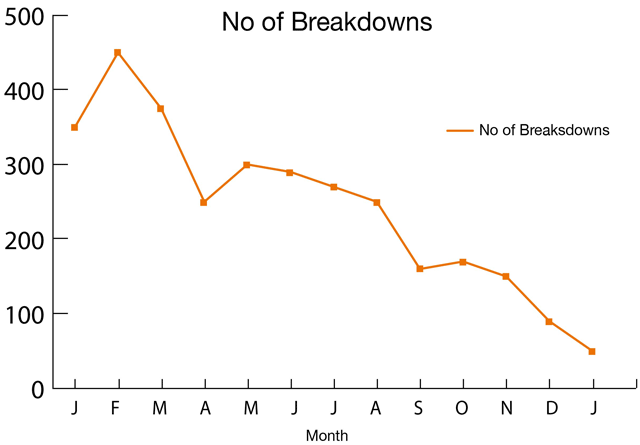
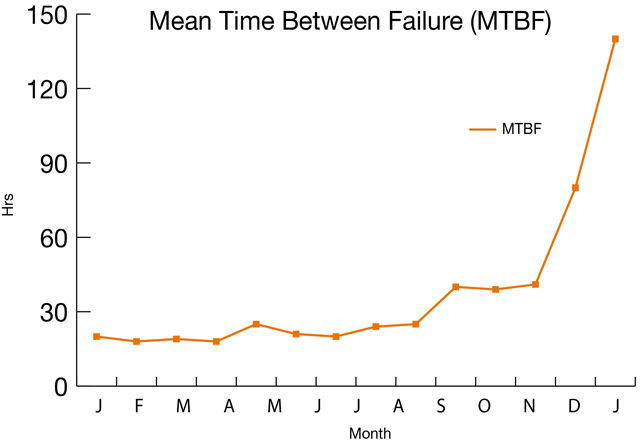
What is Root Cause Analysis?
Before its current form as a widely used problem-solving method throughout all industries, RCA’s first appearance was in the field of engineering. The method is credited to the founder of Toyota Industries, Sakichi Toyoda. It is a process which uses a variety of techniques to rapidly identify the true cause of any failure.
RCA is typically used as a reactive method of identifying causes of events, revealing problems and solving them. The analysis is done after an event has occurred. However, insights from RCA make it potentially useful as a pre-emptive method.
RCA is applied methodically to identify and correct the root causes of events, rather than to simply address the symptomatic result. Focusing correction on root causes has the goal of entirely preventing problem recurrence. Conversely, RCFA (root cause failure analysis) recognises that complete prevention of recurrence by one corrective action is not always possible.
Root cause analysis helps identify what happened, how it happened, and why it happened. It should not be mistaken for fault diagnosis, which is the first level of investigation. For example, if the line has stopped operating, the first step is to diagnose what has caused it to stop: is it the motor, the gearbox, the power supply, a sensor?
Problem solving
The next step is to use RCA to determine what caused the failure. The two stages are not necessarily activated consecutively. The priority has to be to get the line going again. The key to the RCA process is the structured analysis leading to identifying root causes.
Problem solving is key to this stage, and the tools available to complete an RCA include Pareto analysis, 5 Whys, fishbone diagrams; fault tree analysis; and REM (review of existing maintenance).
Just-do-it
If a solution is immediately obvious, then a “just-do-it” action may be appropriate. This should be a first challenge concerning what to do next in the decision making-process.
If no such solution is available, then the underlying causes can be determined using a cause-effect diagram (Figure 4) to structure the thinking involved.
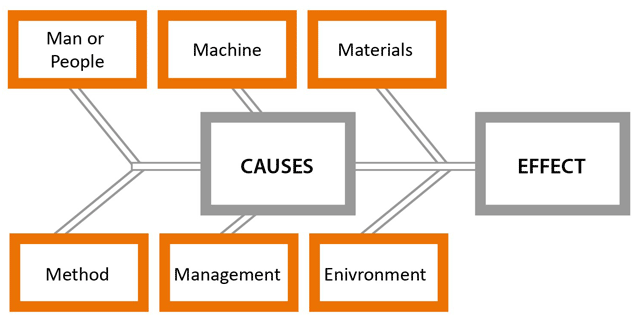
First introduced in 1968 by Kaoru Ishikawa in Japan, the six major causal elements that could contribute to an effect are collected in the diagram before failure analysis is conducted. The analysis is good for making sure that all avenues have been explored.
There can be several potential causes and each one needs to be investigated more closely to dig down to the root of the problem.
5 Whys technique
For each cause identified, the proven 5 Whys technique is often sufficient to uncover the root of the problem (Figure 5). It has been demonstrated that asking the question “why?” five times in succession is an effective way of getting down to the root cause of events.
This may seem too simple or superficial, but not according to world-class companies who use this initial discipline before referring to more complex techniques such as problem analysis models and Six Sigma.
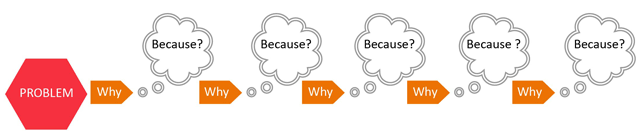
Cause Mapping
Increasingly, a combination of cause and effect, and 5 Whys, has emerged as a process called “Cause Mapping” (Figure 6).
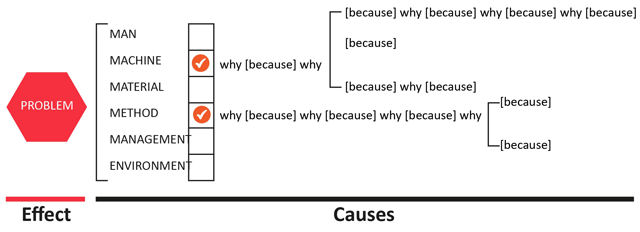
Note the reversal of the direction of thinking from the Ishikawa cause-and-affect diagram. This is because the Japanese write from right to left and it easier for westerners to think left to right.
RCA can also be used to analyse historical failures that are either one-time occurrences or frequently occurring. Quite often, frequent failures are not noticed, for a variety of reasons such as:
- People on different shifts have to deal with the same failures but there is no process for reporting them
- People accept failures as part of the job
- There is no process for the analysis of the work records in the computerised maintenance management system (CMMS) or the data is collected in such a way that does not allow for easy analysis and reporting.
The solutions to the above issues are:
- Establish a common process for reporting all failures including failure, cause and action codes
- Establish a failure reporting and corrective action system (FRACAS)
- Specify and make available the right management information required from your CMMS to identify both one-off and repetitive failures
- Use the CMMS to identify the top ten faults
- Take preventive measures to eliminate the failure occurring in the future.
In short, root cause analysis guides you in asking the right questions – without which you will be unlikely to get the right answer.
MCP provides on-site analysis and support to improve production performance and equipment reliability. In addition we offer City & Guilds certified training in RCA, Fault Finding and Maintenance Optimisation.