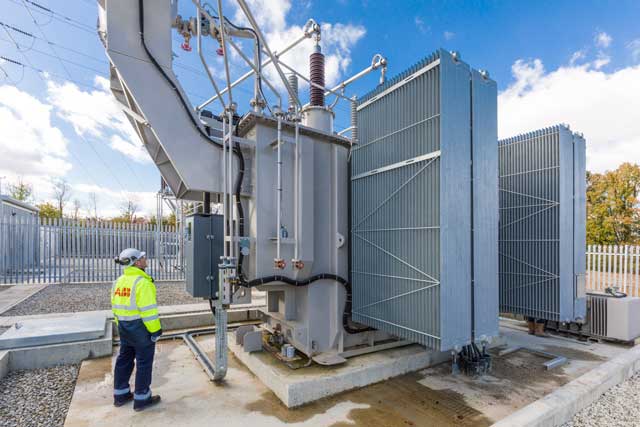
Sagnik Murthy, UK & Ireland Sales & Marketing Manager for ABB’s Transformer Components and Insulation product group, explains how a combination of the CoreTec online monitoring system, Comem eDevices and the CoreSense smart dissolved gas analysis sensor allows utility and industrial customers to optimise and manage power transformers rated from 11-400 kV.
ABB’s Transformer Intelligence is based on two monitoring solutions: CoreSense and CoreTec. CoreSense is a dissolved gas analysis sensor. CoreTec is a complete online monitoring system that keeps a close watch on a transformer’s mission-critical functions and performs a complete evaluation of its operating conditions. Through advanced algorithms, online data can be simulated and forecast to provide information on how transformer use can affect its lifetime, allowing predictive maintenance.
The CoreTec system is modular and expandable to suit a transformer operator’s current and future requirements. It is designed to be maintenance-free for up to 15 years, thanks to robust and proven components.
With its compact size and minimised cabling, CoreTec is easy and fast to install on both new and retrofit applications since only a few sensors are required. It can also be installed on any type and brand of transformer. The unit is easy to operate and displays a large number of operational parameters via a user-friendly and secure web interface.
Combining CoreTec with CoreSense and other sensors provides operators of transformers with a complete asset health monitoring solution and the confidence to schedule maintenance. ABB Comem eDevices are sensors with digital and analogue outputs, providing continuous monitoring of key transformer parameters. Integrating the signals from the Comem eDevices allows CoreTec to monitor over 30 parameters including load and peak load, top and bottom oil temperature, gas and moisture in the transformer oil, and tap changer position. It also provides DNP3 as well as IEC 61850 communication.
A particular advantage of CoreTec is its predictive loading capacity which offers improved control and greater assurance of the load capability of the transformer. If the overload capacity function is employed then it is possible to operate an air-cooled transformer safely at an overload of between 10 and 30% for a defined period of time. Advanced cooling control of a transformer is made possible by using the Comem eOTI sensor to monitor the rising oil temperature due to increasing electrical demand. In response to this input, CoreTec turns on the fans in the cooler banks fitted to the transformer radiators to cool down the oil.
The advantages of dissolved gas analysis
Transformer insulation is fundamentally composed of oil-impregnated cellulose paper surrounding conductors and the layers of multiple conductors that form the transformer windings. A large amount of cellulose is also present in pressboards, wood and mechanical supports used during the manufacturing process.
The entire structure is thoroughly impregnated by insulating oil which also serves as a cooling agent to extract heat from the windings during the operation of the transformer.
In normal operation of power transformers, natural ageing of the insulating system occurs due to its temperature and load cycling. Ageing produces some combustible and non-combustible gases that can be used as a method of determining the health of the transformer.
Cellulose is highly sensitive to heat, oxygen and moisture. The higher the temperature, the faster the ageing process of the paper. In the presence of higher amounts of oxygen and moisture, the paper breaks down through oxidation and hydrolytic processes, which generate additional moisture, acids and other components that accelerate the ageing process even further. The molecular structure of the insulating fluid also breaks down in the presence of higher temperatures and electrical faults such as partial discharges and arcing of several degrees of intensity.
Both cellulose and insulating oil may also degrade in the presence of contaminants such as moisture entering through leaks, or as a result of maintenance activities.
The formation of gases is common to almost all types of insulation degradation. The gases dissolve in the oil, allowing detection and analysis of the defect through monitoring of their levels and evolution. This procedure is known as dissolved gas analysis. The results of years of experience accumulated by the power industry in the application of DGA is well summarised in IEEE C57.104 and IEC60599.
Hydrogen is the fundamental gas that occurs in the presence of thermal and electrical issues leading to oil and cellulose degradation, and thus it plays a key role in the early detection of abnormal conditions or failure modes inside the transformer.
DGA is among the most powerful tools for detecting faults in power transformers. However, there are a number of difficulties associated with laboratory DGA:
- The cost, resources and time to collect samples, particularly in remote locations
- Sample contamination (during or after sampling on site)
- Sample degradation between the time of sampling and the time of analysis
- Laboratory precision (or repeatability) and accuracy
- Laboratory reproducibility.
Furthermore, DGA can only provide intermittent information, from the time that the oil sample was taken. That is why ABB has developed the CoreSense sensor to provide real-time transformer intelligence, online and all the time.
Online monitoring with CoreSense measures hydrogen and moisture
CoreSense uses two solid-state sensors to measure hydrogen and moisture directly in transformer insulating oil without the need for any complex sample handling to condition the oil or separate the dissolved gas from the oil. It addresses the issue of stagnant oil and representative sampling with an innovative thermal pump that makes sure fresh oil is always in contact with the sensors by forced convection. This approach is very simple and ultra-reliable since it has no membrane and no moving parts.
The CoreSense can be mounted safely on any type of valve since it does not create any intrusion into the valve or to the transformer. It is easy to install and requires no special protective action prior to oil treatment activities, a great plus over membrane-based systems that can easily be damaged by pressure fluctuations.
The solid-state hydrogen sensor used in the CoreSense has been extensively tested and characterised for long-term stability and reliability. It features a patented protective coating to avoid ageing and degradation effects from reactive gases, acids and other elements that can be present in transformer oil. It is temperature stabilised to avoid any thermal influence on hydrogen readings and makes use of a reversible hydrogen-specific phase change in a palladium metal alloy to detect hydrogen levels. In addition, the sensor does not consume hydrogen, which eliminates the possibility that the hydrogen reading could be incorrect due to local depletion.
The CoreSense has a built-in embedded computer that continuously monitors all its functions. It provides status at a glance via three LEDs that indicate the condition of the sensor, and hydrogen and moisture levels in the transformer oil. The CoreSense also has a built-in web server that provides a simple interface to allow local and remote network access to gas and moisture levels as well as the current status of the monitoring system.
The CoreSense is designed for durability and long life with no moving parts, solid state microelectronic gas-in-oil sensors that function directly in situ in transformer oil, and a robust all-metal IP67-rated submersible waterproof enclosure. This philosophy was applied to all aspects of the design, including the use of a supercapacitor to keep time in the event of a power interruption, instead of a battery that would have a finite lifetime and would need to be replaced at regular intervals.
The CoreSense accurately measures hydrogen in oil down to 25 ppm with an error of ±10 ppm, and a fast T90 time (the response time to display 90% of the actual concentration) of under one minute. It is designed to provide accurate readings for 10 to 15 years with no calibration or routine maintenance requirements and no consumables. These characteristics make the CoreSense ideal for large-scale deployments even in flood areas or remote, hard-to-access locations subject to extreme weather conditions.
A complement to laboratory analysis
CoreSense is not intended to replace offline laboratory transformer oil analysis, but to complement it. ABB works with a leading test laboratory to provide transformer condition assessment that offers a comprehensive assessment of the dielectric and mechanical state of the transformer including:
- Routine tests for moisture, acidity and dielectric breakdown
- PCB levels
- Dissolved Gas Analysis
- Furan analysis.
CoreTec and CoreSense are designed to be connected to ABB Asset Condition intelligence Solutions that provide a fleet condition dashboard with asset reliability and associated recommendations to mitigate risks.
http://new.abb.com/products/transformers/service/advanced-services/coretec
http://abb.com/transformercomponents