Air operated double diaphragm pumps are widely used because of their simple, portable construction and versatility. Peter Carfrae, AxFlow UK AODD product manager, offers a guide to their maintenance and repair.
The capabilities of the AODD pump are reflected in the fact that it can be used at every stage of the production cycle, from offloading raw ingredients from tankers to the final stage of the filling line. The AODD pump offers the ability to handle shear-sensitive fluids, keep thick and viscous fluids in motion and provide leak-free operation. Other benefits include the ability to be used in a wide range of pressure and flow specifications; self-priming and low-wear operation; ability to handle corrosive and abrasive solutions; improved energy efficiency; and overall low maintenance costs.
An AODD pump uses compressed air as its power source. It has two chambers each housing a reciprocating elastomeric diaphragm which pumps the fluid. A linked shaft allows the diaphragms to move simultaneously as compressed air is shifted from one chamber to the other. The back-and-forth motion forces liquid out of one chamber and into the discharge piping while the other chamber is being filled with liquid.
Repairing AODD pumps is an operation of three stages. First, there is the matter of removing the pump from the pipework and transferring it to a suitable workshop location where there is a compressed air supply. At this stage it is essential to identify the type of fluid that the pump has been handling, since this can reveal whether the pump model was the most appropriate.
Pump Examination
Once the pump has been removed from service and before it is subjected to any further handling, it is advisable to check it for evidence of external fluid leaks. Bear in mind that a leak may not be where fluid stains are found, so it is essential to check for drips and record where they have been identified.
The next stage is to drain the pump, attach the airline and commence air-testing. This is the most critical part of the operation because it ensures that all the issues can be identified.
The air-testing process entails opening the air regulator (if there is one), turning on the air and gradually increasing the pressure to 3-4 bar. The principal issues that are being checked for are: air leaks; liquid escaping from the exhaust; consistency of stroke; and the presence of both suction and discharge pressure. This last item entails holding a hand over the inlet and outlet to feel for both suction and discharge pressures.
Air leaks show that there may be leaking seals, loose bolts or clamp bands. Fluid escaping from the exhaust is evidence of diaphragm failure. If there’s no stroke at all then the air valve is possibly worn or the shaft O-rings are letting air through. An erratic stroke means that the diaphragm shaft seal and air valve need to be checked to make sure they are seated correctly and not obstructed.
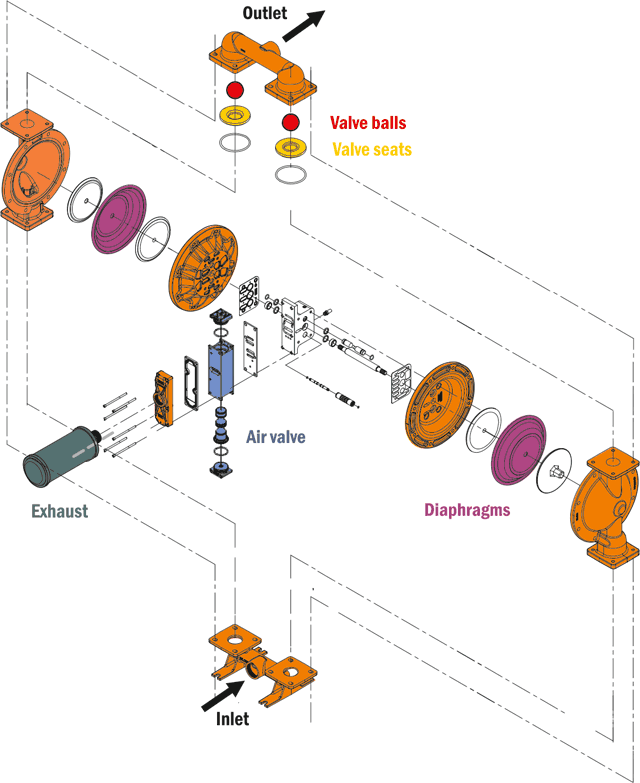
Taking the pump apart
If it is necessary to take the pump apart this should performed in a workshop or prepared area that allows all components to be laid out in an orderly manner. If the pump is used for hygienic applications it is essential that this is carried out in a fully equipped clean room.
Taking the pump apart starts with the removal of the wet sides and manifolds. It is very important to mark up the parts and keep the different sides separate because it is easier to replace the components in the same order as they were removed.
The next step is to check the valve balls for wear. This will require measuring their diameter and checking it against the manufacturer’s specifications, because valve balls usually wear evenly. The diaphragms should be inspected for wear and chemical attack, which may only be apparent as thin stress lines. Finally, the valve seat must be inspected for damage.
It is a good idea when using an AODD pump to fit it with an external air valve assembly. This allows it to be checked on a more regular basis because the whole pump does not need taking apart for this to be carried out.
Replacing faulty parts
Replacing parts that have been identified as at faulty through wear or damage should be done in accordance with the manufacturer’s instructions. If shaft seals are replaced they should feel slightly restricted on the shaft, as should the mechanical shaft seals if they too are replaced. Most importantly, PTFE seals must be replaced because they have no “memory” and will leak if reused. It is recommended that both diaphragms are changed, because they are the pump’s weak point and can cause catastrophic damage to the air side if they break.
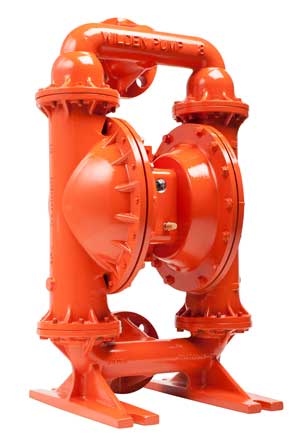
Air testing after reassembly
Once the pump is re-assembled it must be subjected to an air test to confirm that there are no air leaks and the pump runs evenly.
The suction vacuum can be checked by placing a hand across the inlet: you should feel a decent amount of suction and be left with a red ring on your palm. The process should then be repeated for the discharge, with a reasonable degree of pressure being felt. An alternative to this is to create what AxFlow calls a “gauge-ball” by making two holes in a soft ball, inserting a pressure gauge through them and then applying your DIY device to the inlet and outlet.
The final act is to run the pressure up to 8 bar and then dead head it at 8 bar for 30 minutes. This will check the integrity of the pump rebuild. Then re-torque all fasteners if required. If the pump passes all these checks, it is ready to be reconnected to the pipework.