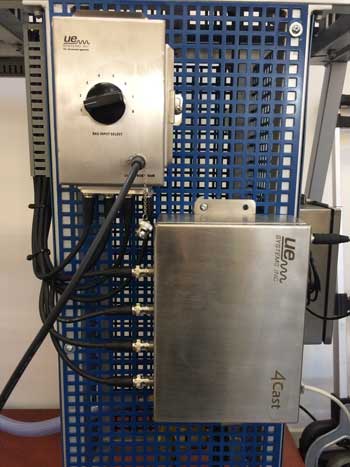
The ability to monitor the condition of assets continuously, from any location, is the established trend in maintenance practices. Adrian Messer of UE Systems says ultrasound, as a key technology in condition monitoring, has a crucial role to play.
Just as technology has been rapidly developing in fields like telecom, data analytics, smart devices and infrastructure, the same can be said of asset condition monitoring. For asset maintenance, the cutting edge development has been remote monitoring – the ability to collect and analyse data from a given asset without the need to be there in person.
Plant maintenance technicians have increasingly recognised the benefits of predictive maintenance in keeping equipment online and preventing unplanned shutdowns.
Ultrasound remote monitoring
Ultrasound technology has emerged as an essential tool. It’s no longer simply a leak detector – it is a valuable technology that allows maintenance teams to identify mechanical faults earlier in the P-F curve.
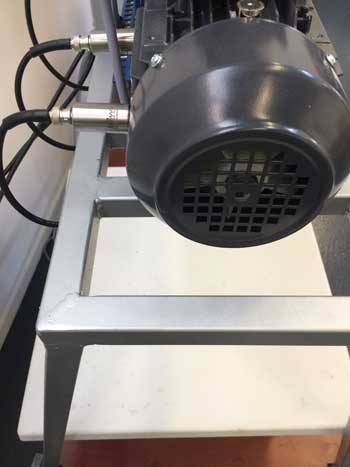
Coupling remote monitoring with ultrasound could prove to be a paradigm-shifting development. Ultrasound works best when you have as much information to work with as possible – that makes it easier to identify patterns, establish baselines and pinpoint inconsistencies. Moreover, as much as today’s maintenance technicians want to avoid reactive maintenance, there are certain assets that take priority over others. Anything that’s closer to failure will earn more attention, meaning other assets could be overlooked if they’re assumed to be newer and in better shape. Remote monitoring can give technicians a way to keep an eye on assets that aren’t being monitored. That’s true for both mechanical and electrical assets.
There are few limitations on the application of ultrasound remote monitoring. Any instance where maintenance professionals are collecting manual data through handheld devices might be an opportunity to monitor remotely. Equipment that is difficult to reach – dangerous, remote, isolated, submerged – can receive the type of regular monitoring that extends useful life. Slow speed assets are great candidates for remote monitoring because it would otherwise require the maintenance technician to take a longer time to gather enough information manually.
Beyond the advantages of larger data sets and remote collection, remote monitoring is easy to install and has the potential for wireless setup. Compared with other systems, ultrasound remote monitoring is a cost-effective choice.
Ultrasound use cases
These are some of the most common ways plant technicians use ultrasound maintenance to improve reliability.
Leak detection: Huge energy-saving potential in compressed air and gas leaks, steam trap testing and valve testing. This is the most common application and it gives the quickest return on investment. Some ultrasound tools can be coupled with a free leak reporting app in iTunes and Google Play, like UE Systems’ Leak Survey app.
Electrical inspection: For corona, tracking and arcing, ultrasound use is driven by safety, insurance agreements, standards and improved technology and software. Keep in mind that it’s a good idea to use more than one technology to avoid missing potential problems, especially corona.
Condition monitoring: Bearings, rotating equipment, and condition-based lubrication are all good candidates for regular remote ultrasound inspection. Best practice here is to establish a route, find baseline readings, determine trends and identify alarm levels. Ultrasound is particularly helpful with slow speed bearings.
The 4Cast and Remote Access Sensors
UE Systems’ remote monitoring tool, 4Cast, interfaces with a bearing asset to continuously collect data and send alerts to the technician’s route-planning software if any alarm levels are excceeded. It works together with ultrasonic remote access sensors (which can be very useful by themselves to inspect enclosed or hard-to-reach bearings) – the sensors, permanently mounted on the bearings, pick up the ultrasound emissions and send them to 4Cast, which then sends that information to data management software in the form of decibel readings. The tool collects these readings from the sensors on a regular basis, but allows the user to specify how often to send information to the software. It will also send a sound file to the Spectralyzer (software for deep sound analysis) when necessary.
With an available Ethernet connection, 4Cast sends all its readings and recordings using the plant’s network, so maintenance personnel can access these readings and sound files even outside the plant’s network – thus allowing for true 24/7 remote monitoring.
Today’s facilities should capitalise on the latest trend in reliable maintenance to get the most out of their assets. As technologies like remote monitoring emerge, they have a positive net effect on industry. Remote monitoring is the latest important plant maintenance technology, enhancing an already valuable tool and allowing plants to build a predictive maintenance culture.