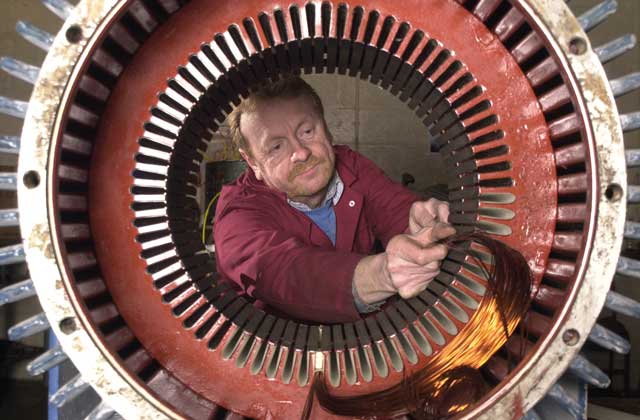
Correctly specified and maintained equipment does not cause explosions – but it is important that maintenance staff have the knowledge and competence to work in hazardous area installations, says Ron Sinclair of SGS Baseefa.
History has shown that almost all major explosions involving flammable gases, vapours or dusts arise as a result of actions (or failure of actions) by people rather than equipment.
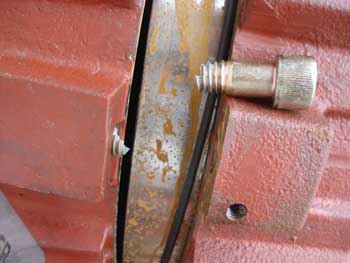
Consider the loss of life on Piper Alpha, or the largest peacetime explosion in Europe at the Buncefield oil storage terminal, or the 2015 wood dust explosion at Wood Flour Mills in Bosley, Cheshire which killed four people. There are many other examples from around the world, where the prime cause was failure to maintain or failure to communicate. Equipment that has been correctly selected for the zone of use, and has been correctly installed, inspected and maintained, does not cause explosions.
IECEx is the international certification scheme for equipment, service providers and people to give confidence that things are as they should be. Having IECEx certification is the easiest internationally accepted way of complying with national regulations, including in Europe and therefore in the UK, where the Dangerous Substances and Explosive Atmospheres Regulations (DSEAR), implementing the ATEX Directive 1999/92/EC, requires site owners to prove the competence of individuals and contractors working for them in hazardous areas.
One of the problems is that general inspection and maintenance staff do not always have the relevant technical background to enable them to understand important differences between an industrial installation and a hazardous area installation. The industrial trade skills are vital, but they are not enough on their own. There is no reason why a highly qualified industrial electrician should ever have previously met a compound filled barrier gland, so would not necessarily understand that an imperfect filling of the gland body has the potential to kill significant numbers of people. Losing a high tensile screw fastener and replacing it with a mild steel equivalent could be just as dangerous. Everyone entering a site that has the Ex hazard warning triangle at the gate immediately accepts additional responsibilities, whether the site is handling flammable dusts or explosive gases and vapours. A whisky distillery has both!
Demonstrating competence
The IECEx scheme for Certification of Personnel Competence has been running for a number of years and looks at the individual’s current work and experience, as well as testing them, both theoretically and on example tasks with practical equipment.
A problem with training courses that run a test at the end of the course is that this can be just a test of short-term memory. In the IECEx Scheme, the training and the testing are kept separate, with a suitable gap to make sure that the candidate is still aware of the requirements, and is capable of applying them, several months after the related training. Learning is a continuing process and competence only comes from application of that learning process. Certification confirms that competence has developed; it is essential for those leading the activities on site, and desirable for those wielding the tools.
In my role as chair of the IECEx Service Facility Certification Committee, I am overseeing the extension of the well accepted scheme for the certification of repair workshops to include companies that undertake installation, inspection and maintenance. The repair scheme grew from a local arrangement between Baseefa and the National Coal Board in the UK, at the time that the mining industry was beginning to outsource many of its workshop facilities and wanted an independent assessment of their continuing capabilities.
This was quickly taken up by the petrochemical industry in the UK, and Baseefa ran a national certification scheme for a number of years. With further development, this became the international scheme operated by IECEx, and SGS Baseefa remains one of the major certifiers of this activity around the world.
The aim of IECEx is to cover all aspects of the safety of equipment, from the original product certification scheme, now encompassing over 30,000 certificates for products made in all parts of the world, through to its installation, inspection, maintenance and repair, all based on international standards in the IEC 60079 series; international confidence applied at a local level.
Ron Sinclair is technical manager at SGS Baseefa and, in addition to his role as chair of the IECEx Service Facilities Certification Committee, he chairs the European Cenelec standards committee responsible for the publication of the IEC documents as EN standards, enabling many of them to become harmonised for the purpose of the ATEX Directive 2014/34/EU.