It’s impossible to truly future-proof technology – but machines designed to be upgraded will have a longer operational life and are easier to adapt to changing requirements, says Boge Compressors general manager Mark Whitmore
Predicting the future is a mug’s game; in an industrial context, attempting to judge future requirements against a backdrop of market and legislative uncertainties is a no less problematic activity. But preserving the integrity and safeguarding the long-term outcome of a capital investment is a serious business, so some forward thinking is necessary. Business leaders are therefore well advised to consider what the future might hold for their enterprises and how it might affect their investment plans.
The term “future-proofing” has become common currency nowadays. But how do you future-proof an item of industrial plant – a factory workhorse such as an air compressor, for example? It comes back to technology, and how it can be applied to traditional items of industrial plant in order to improve their performance and energy efficiency while extending their useful life.
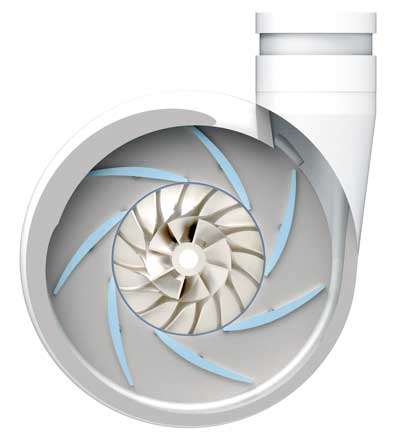
A good example is Boge’s latest generation of high-speed turbo compressors, which are designed and engineered so that critical components can be easily upgraded. This is possible thanks to the use of laser-metal additive manufacturing processes which can create custom parts in a fraction of the time it would take using more traditional production techniques.
As well as extending the life of the compressor, this approach allows the latest parts technology to be made available to the compressor user, giving them confidence that their machine will provide optimum performance, commensurate with current and future business needs and any upcoming regulatory requirements.
At the heart of HST compressor technology are two compact permanent magnet high-speed motors, each having a central rotor suspended on self-stabilising air bearings. Two precision-balanced titanium impellers of different sizes and blade arrangements are mounted at each end of each rotor. At rotational speeds typically in excess of 100,000rpm, air is drawn in via an intake funnel and a specially designed spiral casing to be boosted in three stages to reach operating pressures quickly and efficiently.
Energy losses are minimal thanks to the frictionless air bearing, which is virtually maintenance-free and, unlike a magnetic bearing, does not require power back-up in the event of a mains power failure.
Other efficiency improvements are derived from the impeller, diffuser and spiral casing design, which effectively reduces air pressure on the intake side. This has the effect of drawing cool ambient air through the motor, eliminating the need for a separate fan cooling motor and control unit. The inherently highly efficient motors are inverter controlled, allowing supply to be matched precisely and instantaneously to demand.
Though current HST technology significantly reduces energy consumption, there is still considerable room for future improvement as new technology emerges. It needn’t cost more to achieve better performance, as the cost of any upgrade is likely to be covered by the energy savings achieved by the upgrade itself. Moreover, HST users can take advantage of BOGE’s Continuous Improvement Programme, which frees owners from the expense, risk and inconvenience of compressor modification. CIP carries a guarantee that, if a more efficient configuration becomes available during the life of the installation, the necessary changes will be made with no investment cost to the owner of the system.
HST technology has created the first of a new generation of oil-free, Class 0 compressors that provide genuine benefits for users seeking to future-proof their compressor installations and share the cost of upgrades through effective energy management.